Not long ago, I was called to a paper mill to diagnose a winder with a cylinder that moved at different speeds whenever the weight of its load changed. The cylinder was operated by a proportional valve, so the speed should have been determined solely by the command signal applied to the valve. Now the whole purpose of a proportional valve is to provide accurate speed control.
A standard directional valve is always either fully open or fully closed, but a proportional valve will open by an amount proportional to the electronic command signal applied, hence its name. The more the valve spool opens, the greater flow is delivered to the actuator and the faster it will move. In order to maintain production until the problem was located, the command signal to the proportional valve had to be manually adjusted whenever the load weight on the cylinder changed enough to adversely affect its performance.
The first action the technician took was to replace the (very expensive) valve, assuming that the speed variation must have been caused by incorrect shifting of the valve spool. He was quite disappointed to find that this did not correct the problem. Actually, this unnecessary component replacement could have easily been avoided by checking the valve with a test box.
This particular proportional valve was equipped with a linear variable displacement transducer (LVDT), which electronically feeds back the actual position of the valve spool. The test box could have been connected to drive the valve either by the programmable logic controller (PLC) or an external signal generated by the box and measuring the LVDT feedback. If the valve behaves the same when driven by the test box and the LVDT feedback corresponds correctly to the command signal, the proportional valve is very unlikely to be bad.
When I arrived, we tested the valve, its amplifier and the PLC signal to the valve. We found all of these to be good. So why was the actuator slowing down under heavier loads and speeding up under lighter loads? The problem turned out to be a bad hydrostat module. The module had not been replaced because the valve was assumed to be a pressure-reducing valve based on its hydraulic symbol. Since the pressure downstream of the valve stack seemed normal, they thought the pressure-reducing valve was functioning properly.
Figure 1. (Left) A typical pressure-reducing valve installation
Figure 2. (Right) A common hydrostat configuration
Understanding Hydrostats
Hydrostats are often misunderstood, and mistaking them for pressure-reducing valves is not uncommon. The schematic symbol for a hydrostat is indeed the same as that for a pressure-reducing valve, and in fact that is exactly what the hydrostat is. It’s easy to miss the way the hydrostat is connected, particularly on the hydraulic installation schematics made by the equipment manufacturer.
In Figure 1, a typical pressure-reducing valve installation is depicted. Figure 2 shows a common hydrostat configuration. Notice that the drain line of the pressure- reducing valve goes directly to the tank, whereas the drain line of the hydrostat is connected in the line to the full piston side of the cylinder. Whatever pressure is exerted to extend the cylinder will also be applied to move the hydrostat toward its closed position.
Thus, the heavier the load on the cylinder, the more pressure is applied to close the hydrostat. The result will be that the pressure drop across the proportional valve will be equal to the spring setting of the hydrostat.
For example, if the weight of the load requires 500 pounds per square inch (PSI) to move (as in Figure 3), the hydrostat setting is 200 PSI and the pump compensator is set to 1,500 PSI, the pressure upstream of the proportional valve will be regulated to 700 PSI. If the load weight increases to 1,100 PSI (Figure 4), the hydrostat will regulate the pressure upstream of the proportional valve to 1,300 PSI.
Figure 3. (Left) With the weight of the load requiring 500 PSI to move, the hydrostat setting at 200 PSI and the pump compensator at 1,500 PSI, the pressure upstream of the proportional valve is regulated to 700 PSI.
Figure 4. (Right) When the load weight increases to 1,100 PSI, the hydrostat regulates the pressure upstream of the proportional valve to 1,300 PSI.
Using a Hydrostat Module
So what does all of this have to do with the speed of the actuator? Isn’t speed determined by volume, not pressure? To comprehend this fully, you must first understand how the pressure drop across an orifice affects flow. Essentially, the higher the pressure drop across an orifice, the more flow will be delivered through it. A proportional valve functions exactly the same as a variable orifice flow control.
The greater the command signal, the more the proportional valve will open, the more flow is delivered and the faster the actuator moves. Just as with any other orifice, the greater the pressure drop across a proportional valve, the more flow will pass. Using a hydrostat module effectively converts the proportional valve to a pressure-compensating flow control so that the flow through the valve will not be affected by changes in pressure.
Back to the paper mill, when we tried to adjust the hydrostat, we found that it would not adjust. The internal spool was stuck. The hydrostat was replaced, and the cylinder on the winder moved at a constant speed, regardless of the weight of the load.
In conclusion, don’t overlook the importance of your hydrostats. These modules are essential for regulating pressure when the weight of the load changes. Be sure to keep them adjusted for the minimum acceptable pressure drop so you can ensure your hydraulic systems run smoothly.
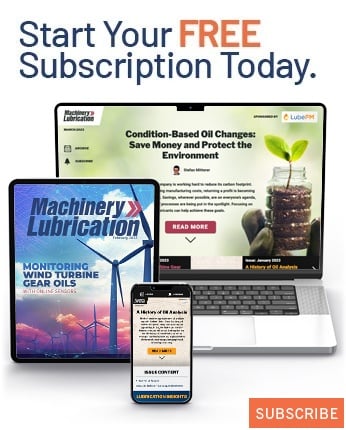