Many vehicles, pieces of equipment and industrial machines use hydraulic hoses. These hoses generally are quite durable and reliable, but if you work or drive long enough, eventually one will leak or break, leading to decreased production efficiency, increased costs, or even environmental or worksite hazards. When this happens, it is best to contact a certified professional who specializes in testing and repairing hydraulic hoses.
However, in a pinch you may need to perform a field repair until you can reach a professional. Temporarily fixing a hydraulic hose is not as daunting of a task as one may think. Once the process is broken down into its six steps, the repair can be quite easy.
1. Identify the Correct Hose
Most heavy equipment can perform several functions (i.e., lifting, pushing, pulling, or cutting), and each of these functions may require a different minimal pressure tolerance. Because of this, there may also be different types of hydraulic hoses with various minimal pressure ratings on a single piece of equipment.
Therefore, it is always best to identify which specification the hose needing repair must meet. In most cases, the hose assembly is made to a specific length, and you will need to splice in a shorter assembly to make up for what is cut away during repair.
Keep in mind that it is extremely dangerous to substitute an incorrect hose even in a temporary capacity. All hydraulic hoses are required to state the minimum operating and maximum burst pressures on the hose. Consult with a trained professional if you have any doubts.
2. Remove the Damaged Area
Once you have completed step one, you will need to cut out the damaged area of the hose. Even if the only issue is that the coupling on the end of the hose is leaking, you must cut off the defective end. Thoroughly clean the area around the cut end of the hose. Clear the area of any dust, dirt or other contaminants, as they could contaminate the hydraulic fluid.
Even a tiny speck of dirt could damage internal components and lead to a costly breakdown. Thus, it is critical to ensure both the fittings and the cut hose ends are clean before proceeding with the rest of the repair.
3. Use an Adapter to Complete Installation
In some instances, a hydraulic adapter will be required to complete the installation of a repaired hose. Since it is not always possible to carry every type of hydraulic coupling, an acceptable solution is to have a kit with a variety of adapters. If needed, install the adapters into the appropriate ports, making sure a solid connection has been made.
Proper tightening (or torquing) of the adapters and couplings is an essential part of the repair process. Over- and under-torquing could have an adverse impact on the hydraulic system. If you are unsure how much torque to apply, consult with the system manufacturer or a trained professional before proceeding.
4. Confirm the Correct Length
Next, place the hose assembly into its position and confirm that the length is sufficient. An overstretched or poorly routed hose will be subject to additional pressure and fatigue. Although it is better to have too much hose rather than too little, it is ideal to have the correct length that allows proper routing according to NAHAD (National Association for Hose & Accessories Distribution) and manufacturer guidelines. Hydraulic systems are constantly under pressure, and a hose that is too short will be more prone to a dangerous (and costly) failure.
Once the hose is the appropriate length, be sure that it is properly routed. This will enable the rest of the hydraulic system to function normally. Many pieces of equipment use angled fittings to route their hoses and allow hydraulic oil to flow more freely. If an angled adapter or coupling is required, install the angled fitting first to ensure correct positioning. Once the angled adapter is in place, the end of the hose assembly can be threaded onto the adapter or port.
5. Ensure a Proper Seal
Thread the remaining end of the hose assembly onto or into the opposite port, verifying that a proper seal is created. Even a small gap or imperfection in the seal can cause problems for the hydraulic system, so double-check the tightness of the seal before proceeding. Remember, the seal should be secure but not overly tight. Never twist or torque the hose when putting it in place. Use a wrench to tighten the fitting, being careful not to overtighten the seal.
6. Circulate Fluid at Low Pressure to Check for Leaks
Finally, turn on the hydraulic system and circulate the oil or hydraulic fluid at low pressure. This will make it easier to spot potential leaks and any damaged connections. Circulating the hydraulic fluid under low pressure will also purge any remaining air. Air in the system could reduce performance or damage pumps and other delicate components.
Continue to run the hydraulic system for several minutes and then check again for leaks. Never use your hand to check for leaks, as this can cause a fluid injection injury. Instead, use cardboard or a sheet of paper. It may take a few minutes for a leak to become apparent, so always double-check the system before driving the vehicle or using the machinery.
Dyed hydraulic fluid,like CITGO’s Mystik® JT-9™ LeakShield® AW Hydraulic Oil, comes pre-dyed in a distinctive color to help staff detect any possible leakages. Eye-catching lubricants can speed field repairs along when staff can easily identify areas of concern.
Making simple repairs to your hydraulic hoses is not as difficult as you may think. However, it is recommended that you have a professional inspect your work. This helps guarantee that mistakes have not been made and limits the occurrence of future problems.
If you suspect a hydraulic hose is leaking or otherwise damaged, act quicklyand make the necessary repairs or replacements right away. Allowing a leak to go unattended and unrepaired could cause significant damage to the entire system and leave a big hole in your wallet. Whether you are working with a farm tractor, a delivery truck or an industrial machine, the integrity of the hydraulic system is only as good as the quality of the hose.
Read more on hydraulics best practices:
Detecting and Managing Hydraulic System Leakage
Hydraulic Systems and Fluid Selection
6 Major Cost Impacts of Hydraulic Leaks
Top 5 Hydraulic Mistakes and Best Solutions
11 Simple Steps for Flushing a Hydraulic System
10 Hydraulic Reliability Checks You Probably Aren't Making
About the Author
Brent Harrison is the business development manager at Max Industrial Solutions. He has been in the hydraulic hose industry for six years.
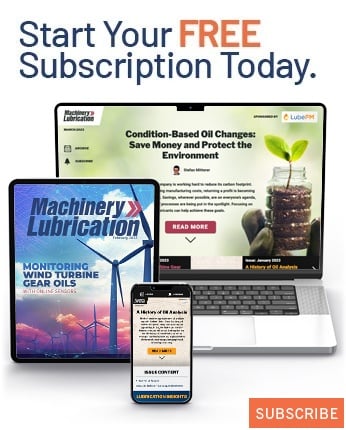