Hydraulic power is a very useful part of industrial machine operation, but it is a mystery to most plant technicians and engineers. There is very little formal training, and most people are given the responsibility of maintaining and upgrading the equipment without the proper tools to handle the job. To ensure they have the right hydraulic system, they must rely on the supplier who provides the unit. This article will not make you a system design expert, but it will increase your understanding of what will make your systems more reliable.
General
In an industrial environment, hydraulic power is used for many functions, such as actuator movement, clamping, pressing, moving heavy loads, transferring product and much more. The system normally is comprised of a fluid container or reservoir, a motor and pump group, filtration, and valves for controlling different functions. There are also fittings, piping, hoses and other electronic monitoring devices. So, how do you determine if the system you have, or the one being proposed by a vendor, is the right system?
First, you need to determine what your system must be able to do. If you know the flow rate and pressure requirements, then you are ready to determine what size motor and pump are required for your system. Identify the flow rate (Q) and the system pressure (p). For example, if you require 10 gallons per minute (gpm) at a pressure of 2,000 pounds per square inch (psi), you will be able to determine the type of pump and horsepower required.
Motor-Pump Group
The type of pump will be determined by the flow and pressure. A fixed displacement pump will provide constant flow at the set system pressure. Although this is generally a cheaper option than a variable displacement pump, it can generate heat in the system that will need to be removed. It also will need to dump power when not needed. This can result in wasted power. A variable displacement pump provides flow and pressure as required. When not needed, the pump will de-stroke, thereby saving energy and not adding heat into the system. Once the pump type has been set, move to the horsepower required.
You can determine horsepower by using the following formula:
HP = Q(gpm) * p(psi)/1714*Eff
Where:
HP = horsepower
Q = flow rate in gallons per minute (gpm)
p = pressure in pounds per inch squared (psi)
Eff = Pump efficiency (A general rule of thumb is 92 percent for most variable displacement pumps and 85 percent for fixed displacement pumps)
Using the above example with a variable displacement pump, you will find your system needs 12.68 hp. This means your system should have a 15-hp motor on it. If the motor horsepower required is slightly over a nominal size, i.e., 16 hp is required and the nominal size is 15 hp, some designers will use the lower hp motor and use up the motor service factor. While this can be done under certain circumstances, it will reduce the life of the motor and the life of system components, such as coupling inserts. Although the cost may be slightly higher, it is usually better to upsize the motor to increase the life and reliability of your system.
Reservoir
Next, determine your reservoir size. Typically, reservoirs are designed to be a minimum of two to four times the pump flow. They must also be able to hold the total amount of fluid in the system. I typically use three times the pump flow as a minimum. In our example, this would mean 3 x 10 or 30 gallons. Most standard reservoirs are in 10-gallon increments. This would require a 30-gallon reservoir. The style of reservoir could be determined by your space constraints or pump manufacturer requirements. A typical flat top or JIC style would mount all components on the top of the reservoir. An L-shape has a deck next to the tank and allows for flooded suction.
The interior of the tank should also be examined. Tanks should be equipped with a minimum of one internal baffle. This will keep the dirty return oil from being immediately pulled into the pump suction line. It will also allow for the settling of contamination in an area away from the pump suction and time for the oil to deaerate. In some tanks, a baffle is not practical, such as in a small vertical tank. In these instances, ensure the return line and suction lines are as far apart as practical. You may also consider using a diffuser. All suction and return lines should be installed so that the fluid is returned below the oil level in the reservoir. Return lines should also be cut at an angle. The pipe should be installed so the angle faces the outer tank wall. This will force the return oil against the tank wall and aid in the separation of return contamination.
Connectors and Conductors
Connectors and conductors (hoses and piping) are another area to check your design. The conductors should be sized to minimize pressure drop. There are general rules of thumb for suction, pressure and return line velocities. For a suction line, the pipe should be sized to a velocity of 2-4 feet per second (fps). For most pressure lines, the velocity should be in the 15-20 fps range. The return line should have a velocity of 10 fps. To determine if your conductors are sized properly, use the following formula:
V=0.3208 *Q/A
Where:
V = Velocity in feet per sec (fps)
Q = flow rate in gallons per minute (gpm)
A = Area of the conductor in square inches
To find the conductor area:
A=0.7854*D2
Where D is the inside diameter in inches.
Now, if I want to determine if the line size is correct for my pressure line, I would manipulate the formula and come up with the following:
D=√{(0.4085*Q)/V}
For our example of a 10-gpm system with a velocity max of 20 fps, the tubing inner diameter would be 0.452 inches, or you would look for a ½-inch diameter pipe.
The other fluid conductor that should be looked at is the hose. Hoses are used to allow for movement of components. They should typically be installed where a rigid connection would cause undue strain and result in possible leakage or failure by fatigue. On an industrial power unit, you should find them on the suction line to the pump, the pump discharge and the pump case drain. You can use the hose’s layline to determine if you have the right hose, the right size and if it is plumbed correctly. The hose is supposed to be marked according to SAE J517. The marking will tell you the 100R number, the hose type when applicable and the hose dash size.
Unfortunately, depending on where your hose was cut from the reel and how long the hose is, the SAE marking may not be on your hose. You should be able to get this from the supplier. Also, the layline can be used to determine if your hose is installed correctly. If the layline is twisted, then your hose is twisted and could prematurely fail. If the layline is kinked, then your hose would be kinked, and its life would be shortened.
If two wrenches are not used to install a hose assembly, there is a good chance that the hose assembly will be twisted. A twist as little as 5 degrees can result in a 70 percent loss of service life, but a 7-degree twist will cause as much as a 90 percent loss of service life to a hose. Before start-up, perform a visible inspection of the layline to determine if there is hose twist.
The installed connectors or fittings should be leak-free and reliable. The common types you should see in your system are shown below:
O-ring Face Seal SAE Straight JIC
Combining these with a “bite” type of connector on the tubing side will result in a leak-free system. Pipe thread should be avoided on hydraulic units. Overtime, these fittings will become loose and leak.
Accessories
There are other components required to make your system safe and reliable. First, your system should have a pressure relief valve. This will reduce the risk of overpressurizing the system and will keep your system and personnel safer. The relief valve should be located just upstream of your pump and have a clean, dedicated line back to the tank. The line should be sized to allow for full pump flow without any chance of back pressure.
Your system should have a pressure gauge to determine the pressure your system is reaching. The gauge should be large enough to read with ease. Normally, it is recommended that this gauge be liquid-filled. This type of gauge, versus a dry gauge, is more reliable and less susceptible to vibrations or pressure fluctuations, which can occur due to normal system operation or outside environmental influences. It should also be equipped with an isolation valve.
The unit should have a temperature gauge or switch installed. If practical, a pressure switch is preferred. The switch can be set for a maximum temperature. This will keep your unit from getting too hot and degrading the fluid or damaging other components within your system. In addition to the temperature switch, a level switch should be included. The level switch should be used to indicate either a full reservoir, a low level warning or a low level shutdown. This switch will keep you from overfilling your reservoir. It will also keep the pump from operating in a cavitation situation.
Filtration
Contamination can enter a fluid system in many different ways, such as during routine maintenance, through cylinder rod seals, from added fluid and even from component wear. To improve system reliability, this contamination should be addressed through filtration. There are three main areas of filtration in an industrial system to be considered: headspace (reservoir air space), inline (pressure and return filtration), and offline (kidney loop). The headspace filter will be a filter located on the reservoir to ensure the headspace is clean and the air being exchanged between the headspace and the atmosphere is clean and dry. If possible, the best possible solution would be to use a desiccant breather. This breather will keep the moisture out of the headspace in your reservoir and reduce contamination.
The use of a pressure filter is optional but always a best practice. A pressure filter would be installed after the pump but before other components in the system. The filter is used to remove contamination from the fluid before it passes through the system components. If you have components with tight tolerances, such as a proportional or servo valve, a pressure filter should be used. The filter should be sized for minimal pressure drop in the system.
A return filter should always be used. The return filter will capture the contamination that occurs during system operation. If possible, an in-tank filter is the best type. This will allow for the largest surface area and dirt-holding capability while minimizing back pressure on tank lines. All filters should have a bypass and some type of indicator to show when the filter has reached the end of its useful life. The best filtration available is worthless if the filter element is dirty and the system is in bypass.
The final method of filtering the system is an offline system, more commonly referred to as a kidney loop. This method utilizes a dedicated low-pressure pump and filter/cooler combination to maintain a more accurate cooling as well as continuous filtration. The system would be designed to turn the contents of the reservoir every 10 to 15 minutes to ensure the desired ISO particulate range is achieved.
You should also consider the filter the company is recommending. Will it provide the proper cleanliness level and contamination holding capacity? Don’t overlook the filter’s beta ratio. Beta ratio is a way to determine how efficient you filter is. It is a measurement of the number of a certain size particle entering a filter compared to the number of the same size particles in the oil leaving the filter.
Summary
There are many other considerations to review when evaluating a hydraulic power unit. Is the reservoir designed to take out the proper amount of heat? Do I need to add a heat exchanger? Should I run a variable frequency drive? Can I use accumulators to avoid system delays? Am I using a fluid other than a mineral-based oil?
The best way to achieve reliability in a system is to have a qualified designer create your system. Ensure you have trained technicians maintaining your system. Stick to a strict, rigid maintenance plan. And, just like you do with your car, when something needs to be addressed or corrected, take care of it in a timely manner. Following best practices and improving your education are the best ways to ensure your system is clean, quiet and reliable. No one cares more about your system than you.
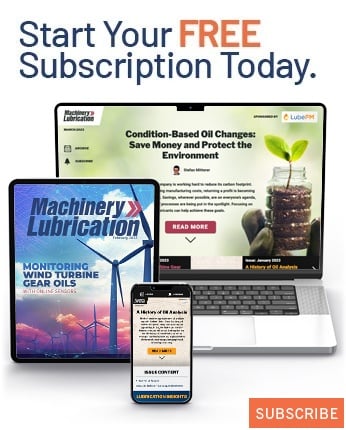