While individual predictive maintenance (PdM) technologies can function properly alone, they only truly flourish when working in unison. Gaining an understanding of this maintenance strategy, along with which technologies are utilized and how they can function together to drive results, can often help identify and resolve equipment reliability issues.
Predictive Maintenance Strategies
Predictive maintenance is an approach designed to determine the condition of equipment in order to forecast when maintenance should be executed. Failure is monitored through vibration, lubrication, infrared thermography and other technologies over time. Work is then scheduled to be performed before extensive component breakdown occurs.
There are several advantages to applying a predictive maintenance strategy. A reduction in spare parts inventory can be noted due to issues with components being identified weeks or even months before the failure is likely to occur. This insight allows maintenance planning to minimize parts on the shelf and reduce stocked overhead.
A reduction in maintenance labor costs can also be recognized as the need for unplanned overtime due to emergent work is lessened. One additional benefit is the decrease in repair time. As failures are caught earlier, fewer catastrophic failures occur, driving down the number of components to be repaired and maintenance hours spent on equipment.
While there are several advantages to this strategy, there are also a couple of disadvantages to mention as well. First, it can be expensive to implement due to the initial training and upfront costs of the technology-specific tools. It also requires time for personnel to master any given technology.
Although the predictive strategy will only be discussed here, proactive, preventive and reactive strategies should all play a role in day-to-day maintenance operations. It is simply a matter of identifying where and when each one should be employed.
Predictive Technologies
Within the realm of predictive maintenance, several technologies can be used. The three primary technologies that will be reviewed here are lubrication, vibration and infrared thermography. Other technologies, such as ultrasound, motor current analysis and motion amplification, can also play an important role depending on the component and application.
Lubricant Analysis
Lubricant analysis is one of the oldest technologies that is still currently applied. A lubricant's function is to control friction, wear, corrosion, temperature and contaminants as well as transmit power. Simply put, the objective should be to preserve a clean, cool and dry environment.
This is achieved by maintaining the condition of the lubricant, the lubrication system and the machine. Lubricant analysis can be broken down into grease and oil, with three specific focus groups: fluid properties, contamination and wear debris.
Several different tests can be performed in each group, depending on the conditions mentioned above. Some of the most common tests performed on a routine basis are viscosity, moisture content and particle count.
Vibration Analysis
Vibration analysis is the process of monitoring anomalies and rates of change in a system’s signature. As the signature begins to change, the condition of the equipment also begins to change. These changes are primary monitored in spectral and waveform data, but phase can also be utilized depending on the application.
Waveform data is a measurement of acceleration over time, while spectral data is the measurement of amplitude over frequency. Phase is essentially the relationship that exists between two entities.
It is important to understand which unit one is looking at regarding frequency, as this plays a key role in analysis. Frequency is commonly viewed in either cycles/revolutions per minute (CPM/RPM), hertz (Hz) or orders (run speed response). As mentioned above, sources of vibration can be found in spectral, waveform and phase analysis, but the majority of analysis is often performed in the spectrum.
Equipment vibration symptoms noted during analysis are divided into three sections: sub-synchronous, synchronous and non-synchronous. Symptoms noted in the sub-synchronous section occur at a greater rate than turning speed.
Some examples might include oil whirl or belt vibration. Symptoms that are synchronous occur at or a multiple of turning speed. The majority of issues noted in vibration typically fall in this realm. Examples of synchronous issues would include imbalance, misalignment and looseness.
Non-synchronous symptoms would be any items above running speed that are not a multiple of running speed. A few examples of non-synchronous symptoms would be resonance, cavitation and bearing faults.
Understanding when to collect vibration data is also important. Baseline vibration data is generally collected at the installation of the equipment. After the baseline is developed, a frequency at which you collect general vibration data should be set and the values should be referenced against the baseline for comparison.
Other vibration tests that might be performed to better understand issues once noted include high-resolution data, resonance testing and cross-channel phase.
Infrared Thermography
Infrared thermography analysis can be described as the detection of radiation energy emitted, transmitted and reflected, then converted to a temperature display from a non-contact device. The primary objective with this technology should be to identify change in radiation variance, distinguish thermal anomalies and drive replacement before significant maintenance work or equipment downtime takes place.
Comprehending where infrared energy resides on the electromagnetic spectrum allows users to better understand how visible light relates to infrared. The wavelength band for visible light that our eyes have the ability to perceive ranges just less than 1 micron. Just past visible light, infrared comes into play at slightly longer wavelengths.
Typically, infrared thermography analysis is operated at 3 to 5 microns for mid-range applications and 8 to 15 microns for long-range applications. Infrared devices with sensors have the ability to detect the radiation in this range due to the fact that their sensitivity encompasses the near infrared.
Infrared surveys typically are performed at the completion of the equipment installation or when it is placed back into service to identify a reference point. Surveys usually are completed at a routine frequency after this, depending on the equipment’s criticality and operating state.
It is common to see abnormal, alert and alarm ranges set on equipment as identifiers of when to act. Infrared thermography, like all other technologies, can be used as a cross-reference tool as well as to help troubleshoot component-related issues.
Using Predictive Technologies
Now that you have an understanding of what a predictive maintenance strategy is and the technologies that fall under its umbrella, it is time to determine how you can utilize these technologies in conjunction to yield better results in the field.
Bearing, gearbox, misalignment and pump failures are recurring issues that often challenge reliability and can be significantly minimized through the collaboration of predictive maintenance strategies.
Bearing Issues
Bearing issues often arise in the form of overheating, false brinelling, particle contamination, corrosion, misalignment and typical fatigue over time. Applying lubricant, vibration and infrared analysis in accordance can help identify and troubleshoot these issues.
From a lubricant analysis perspective, one might want to perform particle counting, elemental analysis and analytical ferrography on the lubricant. Vibration concerns in regard to bearings frequently would show up at certain bearing fault frequencies for the inner race, outer race, cage or bearing balls, as well as two times the run speed for a cocked bearing. Infrared analysis is another cross-reference option.
As the bearing begins to degrade, one should see a noticeable increase in temperature pertaining to the nameplate specification over ambient or against other common redundant equipment. It is always good practice to keep in mind the Arrhenius rate rule with bearings. It essentially states that for every increase in temperature of 10 degrees C, one cuts the life of the bearing in half.
Gearbox Failures
Gearbox failure is another repeat offender for downtime at many plants. These failures frequently occur due to misaligned and eccentric gears, fretting or scuffing wear, pitting of gear teeth, and prolonged bending fatigue. Lubricant tests to consider with this type of failure would include particle counting and elemental analysis.
Vibration most likely would show up in the spectrum at the gear mesh frequency as well as the harmonics associated with them. It can also be detected through waveform analysis. Infrared analysis results should often show signs of elevated temperature from one gear stage to another or one end to another.
Alignment Failures
Alignment failures routinely take place through offset or angular misalignment, soft or sprung foot conditions, rotor bow conditions, or voided bases. Test options for lubrication related to alignment concerns would include grease hardening and elemental analysis.
The vibration signature to consider would be one and two times the run speed, depending on whether it is angular or parallel misalignment. Cross-channel phase would be another useful tool for misalignment. Performing phase checks across the motor, coupling and feet are all extremely useful options.
Alignment issues can also easily be diagnosed by infrared thermography through elevated readings at the direct area of concern on the inboard of the driver or driven equipment.
Pump Failures
Finally, pump failures mainly transpire due to cavitation, recirculation, turbulence, rotating looseness and element wear. The primary lubricant tests to perform would be particle counting and analytical ferrography.
Vibration signatures to consider would include elevated noise floors due to cavitation, pump vane pass frequency, the number of pump vanes multiplied by the run speed, and rotating looseness at run speed harmonics. As with vibration and lubrication, infrared thermography plays a role as well through anomalies noted with liner wear in the pump housing and bearing case temperatures.
In conclusion, although one technology can function properly alone, it is often best practice to utilize multiple technologies to troubleshoot issues. By gaining an understanding of the predictive maintenance strategy, which technologies can be utilized and how they function together to drive results, you can significantly help identify and resolve equipment reliability issues.
This article was previously published in the 2018 Machinery Lubrication Conference Proceedings.
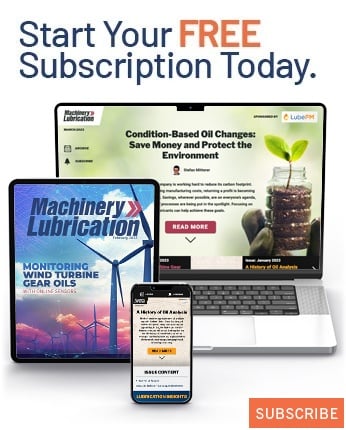