Having spent nearly my entire career in the field of lubrication, I’ve become increasingly aware that for many companies, the practice of neglecting lubrication has become deeply engrained in maintenance culture.
For these companies, changing such practices is like trying to turn an ocean liner. I’ve become convinced that their complacency is not simply a case of ignorance, but rather follows a pattern strangely similar to addiction.
After all, I’ve taught the virtues of modern lubrication to legends of organizations, only to see many of them quickly and irrationally relapse into their past destructive habits. This typifies addictive behavior.
These observations were the impetus for the topic of this column. In keeping with the addiction theme, I’ve modeled a plan for recovery using words and concepts resembling the highly successful 12-step program that serves as the cornerstone of recovery for the Alcoholics Anonymous (AA) organization. After all, if lubrication neglect is an addiction then perhaps it should be treated in similar fashion in a program of 12 steps.
For companies afflicted with this addiction, casual intervention may not simply be enough. Instead, an ultimatum must be declared. Otherwise, past practices and bad habits will gradually return. Like other addictions, denial is the heart of neglect. The 12-step program discussed below brings the denial issue front-and-center. Until denial is acknowledged and addressed, no other progress can logically be made.
12-Step Program to Recovery
1. Admitted we were powerless over our addiction to lubrication neglect – that our attempts to stabilize machine reliability had become unmanageable.
Most problems do not self-correct. Yet some companies seem to expect lubrication problems to vanish by themselves. Instead, they are more like a bad rash … they keep coming back. This first step requires a fundamental awakening that doing nothing (perpetuating neglect) is the root of the problem. In contrast, doing something often evokes fear of the unknown.
After all, it does involve risk and requires figure-it-out skills. Most importantly, the task must be purposeful and lasting. To accomplish these goals, we need to move further down the list of steps.
2. Came to believe that there is a greater maintenance intelligence than our own that could guide us in restoring our lubrication sanity.
Information and knowledge is all around us, but it must be sought and embraced to be useful. Repeating past practices and expecting a different result is often said to be the definition of insanity. Believing there is a better, more intelligent way to lubricate machinery fuels the progress toward change.
3. Made a decision to rid ourselves of stubborn resistance to change and to accept the guidance and wisdom from those who have made the transformation before us.
Charles Darwin once said, “It is not the strongest species that survive, nor the most intelligent, but the ones most responsive to change.”
4. Educate ourselves to the richness and rewarding world of modern lubrication. Made a searching and fearless inventory of our lubrication and maintenance failings based on this new knowledge.
Knowledge empowers people to leverage information in ways that improve their world. Knowledge also results in a loss of innocence (remember, “ignorance is bliss”). Education is an enabler. It enables us to see what’s wrong and know what needs to be changed. Taking inventory of what needs improvement gets the ball rolling.
5. Openly admitted to ourselves and others that we will no longer continue the destructive behavior of lubrication neglect.
Once we openly enunciate our plans to our organization, it’s harder to reverse course and transgress to our past addictive behavior. Merely announcing your plans, however, is not sufficient. It must be a willful, “burning bridges” type of declaration.
6. Begin to prepare ourselves for the journey of lubrication transformation by following a programmatic pathway that includes training, design, documentation, deployment and metrics.
Transforming past lubrication practices to a program of excellence requires a master plan - a great plan. We need to cross the deep chasm from “knowing” to “sustained doing”. That plan must include the following essential elements of lubrication success:
- Train for lubrication excellence
- Design for lubrication excellence
- Document for lubrication excellence
- Deploy for lubrication excellence
- Measure for lubrication excellence
7. Humbly ask support from managers, financial executives and fellow employees to join us on this transformation journey.
Reliability is everyone’s responsibility. Active and regular support is critical. So is the need to build team energy and excitement. Cultural unity enables cultural transformation. Fragmented efforts cannot transform anything.
8. Make a list of all the machines that have been abused by our addiction and become willing to make amends to them all.
Perhaps some machines were not neglected. By knowing which machines are most in need of modernized lubrication, the transformation master plan can begin in earnest. High-criticality and bad actor machines usually fall into this category. Others that are less obvious may need to be considered as well.
9. Make amends beginning with those machines most mistreated by removing the root of our lubrication evils and bringing forth appropriate modern practices in restitution for past acts of neglect.
Define the current and future states of lubrication for each of the machines in the transformation. A lubrication audit helps define current state, while a design activity helps characterize future state. Lubrication design includes lubricant selection, lubrication method, contamination control, lubricant sampling and analysis, inspection (PMs) and procedure documentation.
10. With a view toward continuous improvement, once again take a searching and fearless inventory of lubrication shortcomings. Aided by persistent study and the vision of trusted advisors, find new ways to overcome remaining incompetencies.
Knowledge is like compound interest, it builds on itself. First, we start in total darkness – not knowing what we don’t know. Next, we gain awareness through training which teaches us what we don’t know. Combining the new awareness with judgment and purpose, we select specific value-generating topics we need to know.
Finally, we seek and receive the specific knowledge that we targeted. This becomes our new core competency and empowers even greater awareness (of what we still don’t know). The new awareness brings us back to the beginning, in a circular fashion. Therefore, knowledge and core competency (lubrication proficiency) builds over time, just like compound interest.
11. Fend off the allure of transgression by posting continuous reminders of the costs and anguish of past lubrication practices and by keeping these 12 steps ever-present in our work environment.
Relapse and failure are always lurking. Our defense is never letting our guard down by both staying alert through constant reminders and by continuous improvement. While improvement may no longer be a compelling need, it does control relapse risk. After all, if we are moving forward, even slowly, we are not sliding backward (into addictive habits).
12. Having had an almost spiritual awakening on the virtuous state of machine reliability, pledge to carry this 12-step message to other addicts of lubrication neglect and most importantly, ceaselessly practice these principles with vigilance and resolve in all future maintenance affairs.
Those organizations that have crossed the chasm to lubrication excellence have the responsibility to serve as the role model and mentor for others who have yet to begin the journey. Be a great teacher by inspiring others and sharing these 12 steps. You are now a sober recovering addict of lubrication neglect.
Read more on lubrication program best practices:
10 Lubrication Best Practices for Improved Equipment Reliability
How to Get Buy-in for Your Lubrication Program
39 Current Trends in Lubrication and Oil Analysis
The Business Case for Lubrication Excellence
Editor’s Note:
The editorial staff respects the mission of Alcoholics Anonymous and other 12-step programs.
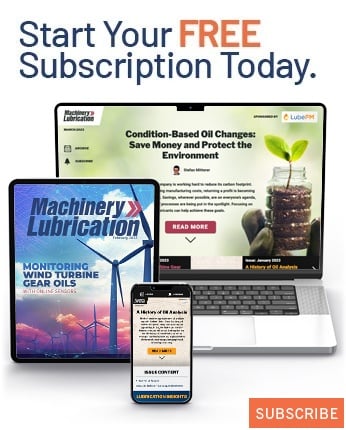