Lubrication is full of metrics. Whether it’s oil analysis, equipment uptime, filtration or route compliance, all have a role to play. There is one metric in lubrication that has proven extremely important and effective at revealing hidden lubricant-and equipment-related issues. This metric is known as Lubricant Utilization.
In short, this is a Key Performance Indicator (KPI) based on the volume of lubricant applied to machines, relative to the amount of lubricants that have been disposed of over a period of time. But more importantly, the data collected on Lubricant Utilization is directly associated with other important metrics and KPIs across all stages of the lubricant and can define some KPIs for the lubrication program. Some of these indicators may focus on controlling overall lubricant expenditures while others focus more on minimizing risk and reliability issues. Regardless of the indicator, it must begin with establishing the metrics and tracking good data.
Tracking the Application of the Lubricant
Lubricants, like many other consumables, are likely monitored by some sort of inventory tracking system, usually starting in a warehouse. Here, the warehouse management tracks the reception of each lubricant, by container or in batches as they arrive and are put into a storage location. Lubricants can be delivered in many different containers, such as pails and boxes of tubes for grease or in drums, totes or quart/gallon-size bottles for oil. But regardless of how it is contained, an amount of total lubricant delivered should always be known and recorded. Knowing this total delivered amount and associated costs are metrics by themselves, as well as monitoring when each lubricant reaches inventory minimums and maximums. But there’s more.
Warehouse metrics are more than just the inventory of your lubricants in storage. It can be an important piece of data that stretches across your entire plant’s overall equipment reliability and helps monitor plant performance. As these lubricants become needed for equipment, inventory management can monitor their exits from the warehouse with date, time, by user, which machine(s) it will be used in, how much, how often, and so on. As this data is collected, it populates the first important piece of useful information for Lubricant Utilization.
Tracking the Removal of the Lubricant
For a variety of reasons, lubricants become removed from the machines they are used in. The most obvious and preferable reason is because they are intentionally drained by maintenance during oil change procedures. This happens either because of a scheduled oil change as a PM task or because compromised conditions of the lubricant have triggered a condition-based oil change. When this happens, the volume of oil is collected in an appropriate waste container which is subsequently disposed of in a larger waste oil storage tank. During this process, the volume of disposed oil should be noted as part of the maintenance activity. This can be estimated by using volume markings on the sides of the disposal container, or any other suitable means. Oil disposal is going to be easier to track, but it is important to note that grease can sometimes be tracked as well.
Is the lubricant applied to the machine always the same as the lubricant disposed of? Not always. There are many reasons for this expected discrepancy. Exploring these reasons and tracking lubricant consumption can be important. In one way or another, the constituents that make up the lubricant end up somewhere. When the lubricant is removed from the machine for unknown reasons, it also removes its ability to provide key lubrication functions and risks lubricant starvation on the equipment. Aside from scheduled oil drains, here are some examples of possible lubricant removal mechanisms that may occur:
- Dripped out by gravity from leak points
- Pushed out in pressurized systems from seals
- Sucked out into product suction lines through seals
- Evaporated out by volatilization of oil molecules
- Burned out by other hot machine surfaces or microdieseling
- Absorbed out by rubber and other elastomeric materials (seals)
- Adsorbed out by contaminants and other materials as polar additives and other polar oil molecules hitch a ride when they are trapped and removed by filtration
- Foamed out by stable foam generation and escape from a breather port
- Splashed out in highly agitated and open top sumps
- Extracted out for lubricant sampling
- Flung out by high centrifugal force on open-air components (open gears, chains, etc.)
- Purged out by maintenance on bottom sediment and waterbowls
- Trapped out in closed off pipes and hoses
- Spilled out by overfilled systems by maintenance or when contaminants significantly contribute to volume control issues
- Siphoned out through pipes, hoses and other absorbent materials
- Drained out due to other maintenance activities or abnormal events, such as
- Sudden component failures
- Component replacement
- Machines going out of service
Some of these lubricant removal mechanisms may be ordinary or seem negligible in volume, but it could still become a root cause for equipment issues. Some of these mechanisms may be highly aberrant and even difficult to quantify in terms of volume for some of the more unique removal mechanisms. Nevertheless, awareness of these possible events is important and should considered during investigation.
In some machines (particularly smaller sumps), every drop is a critical contribution to effective lubrication and when it is lost, it can put the equipment at risk. Tracking the known quantities of lubricant drained becomes an excellent indicator of the unknown and unexpected quantities of lubricant loss.
Calculating Lubricant Utilization Metrics
From a plantwide perspective (as a macro metric), quantifying the total volume purchase or segmented by totals for each lubricant type should be easy. This data can then be compared against either the known volume of lubricant disposed of (to calculate the Lubricant Utilization Ratio) or the total machine charge in the plant (to calculate the Lubricant Consumption Ratio), all over a fixed time interval, such as yearly. Here is a further explanation of these two ratios.
- Lubricant Utilization Ratio is a calculated ratio between the lubricant purchased volume versus the lubricant disposed volume across the plant. If done correctly, this should be a number greater than one. The higher the number, the more oil is going unused or unaccounted for by one or more removal mechanism, including any untracked volumes of oil drained that may have never made it into a machine. A number close to one suggests that most oil applied to machines eventually finds its way to an appropriate disposal container. And while a number less than one is not common, it might be justified, such as when a large number of machines are going into repairs or out of service. Applying data from a greater period of time can minimized the influence from these unique events for this metric. A good goal for the Lubricant Utilization Ratio is about 1.5 or 2.0, but this will vary based on industry and equipment type.
- Oil Consumption Ratio is a calculated ratio between the lubricant purchased volume versus the total lubricant machine charge (not considering lubricant removal mechanisms). This ratio provides a different consideration on lubricant utilization by observing how effective the lubricant and the lubrication system is over a period of time. In the example data below, the consumption ratio started out as a 2.4. Working towards a lower number would mean that the oil has a longer life in the machine. Some reasons the life of the oil in the machines are increased could be because:
- The oil was better selected for the applications, thus reducing the lubricant degradation rates.
- Oil changes are more condition-based, rather than scheduled where oil may be prematurely drained.
- The machines are operating more efficiently, not needing more shutdowns (and oil drains)
- Less leaks or other unknown lubricant removal mechanism
Note: An increase in lubricant life assumes there is also condition monitoring in place. Otherwise, simply leaving the oil in the machine longer will put the machine at risk of failure. For this reason, the Oil Consumption Ratio must be monitored alongside condition monitoring and failure rates KPIs.
A common Oil Consumption Ratio goal would be a reduction of 50% each year until a Consumption Ratio approaches 0.2, which will also vary by industry and equipment type. By year three in the example, the ratio was reduced to 0.29 which was a total reduction of oil consumption of more than 85% across the plant.
From a machine-specific perspective (as a micro metric), quantifying the total volume applied to each machine or group of similar machines over an oil change interval is usually achievable. Rather than a lubricant purchase volume, this includes the initial volume of oil put into the machine(s) and any subsequent top-ups until the schedule oil change. Similar to the macro version of this metric, this data can then be compared against the known volume of lubricant from the machine(s) that was disposed of to calculate the Lubricant Utilization Ratio or compared against the lubricant charge per machine to calculate the Lubricant Consumption Ratio. Since these metrics are calculated for specific machines, the reasons for a higher or lower ratio value can be more exclusively observed.
These are examples of metrics that can be developed as important performance indicators of the lubrication program. If abnormal data trends are discovered, this can help uncover a lubricant removal mechanism taking place and reveal hidden problems within the machine.
Creating Key Performance Indicators by monitoring Lubricant Utilization
From the initial delivery of the lubricant to the eventual lubricant disposal and removal from the plant, there are many metrics and key performance indicators that are directly connected to Lubricant Utilization. Here are a few examples, as well as where they are connected to each of the six lifecycle stages in the Ascend™ Methodology:
- Lubricants must meet standards before they are applied to machines, thus there are key performance indicators connected to lubricant quality control (Ascend™ Factor R1P) and the Supplier Selection (S2P). If the oil analysis results for new oil testing are often finding issues regarding lubricant meeting specification and cleanliness requirements, then this needs to be addressed. Otherwise, this will impact the lubricant’s ability to maintain equipment reliability.
- There are many metrics related to lubricant storage practices in the warehouse and in the lube room (R2P) and inventory management (R4M). This includes tracking data such as shelf life and inventory volume changes with minimums and maximums. When this data is compared to specific times each amount of lubricant is brought out to the machines, key performance indicators can be defined. What could cause any discrepancies or unusual trends in the lubricant volumes and inventory control? Maybe lubricants are not being properly tracked upon exit. Maybe lubricants are being stored too long or compromised and never used in machines. Looking for trends and abnormalities in this data is not unlike other types of condition monitoring.
- When lubricants are transported and applied to machines, using appropriate top-up containers (H3P), filter carts, grease guns or other replenishment methods, the volumes can be tracked for suspicious use and activity. Both excessive use and or lack of use are important considerations. These can be linked to a number of possible machine issues or possibly even personnel-related issues.
- Tracking lubricants in use can be compared to how lubricants are becoming filtered or reconditioned (C2P). Machines with larger sumps that may require more complex contamination control strategies could impact the volume control of the lubricant. Some contamination removal strategies even remove a volume of lubricant temporarily or permanently, and this could present some risks to the machines. On the other hand, some lubricants have their life extended as they are reconditioned and reapplied, a good performance indicator of lubricant use.
- When oil analysis is chosen for certain machines (A1P), the decision factors stem from the opportunity to increase machine reliability through careful monitoring of lubricant properties, contaminants and wear debris. Effective oil analysis data interpretation (A6M) is necessary to build confidence. We should expect the occasional justification of preventative actions to remediate oil at risk of degradation and schedule more precise oil changes. When this happens, Lubricant Utilization is improved.
- Leakage management (E3M) always comes to mind when monitoring lubricant volumes and improving overall Lubricant Utilization. There are many possible metrics on leaks, such as tracking leak rates, total volumes lost, time until remediated, lubricant type, machine type, environmental and health exposures, the cost associated to the lubricant lost, the cost associated to any machine related failures or downtime and so on. Every plant faces different challenges with leakage control, but the goal should always be to minimize this when possible, particularly when the risks are high.
Conclusion;
Analyzing Lubricant Utilization within the plant is an important metric for revealing many hidden problems at all stages of the lubricant lifecycle. First, steps must be taken to collect good data, which might be easy in some areas but more challenging in others. Certain data will never be fully collected, such as with some of the lubricant removal mechanisms mentioned. But there is good news. While putting the practices in place to collect and track volume use, where possible, you will uncover opportunities for improved lubrication along the way and start to see how the benefits of corrective actions can already be achieved. In fact, implementation may be an ongoing effort. Regardless, Lubricant Utilization is more than just a metric. It has a lifetime of benefits and has proven to be a powerful performance indicator for the entire lubrication program.
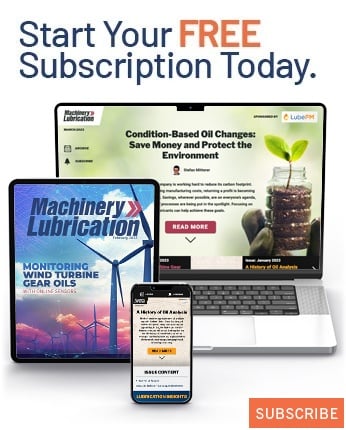