An effective quality control process ensures that incoming lubricants are inspected, evaluated and deemed fit for service. Incoming lubricants are a pathway for contaminants, and failure to prevent contaminated lubricants from entering machines can hinder an entire lubrication program. Here are some tips for implementing efficient and effective quality control practices:
-
Ensure that every drum of oil received is labeled correctly; six out of every 100 drums are mislabeled or improperly labeled.
-
Ensure that all of the grease tubes received do not have any base oil bleeding from the package. Greases that have no base oil are not properly lubricating their assigned application. Remember, the base oil and additives are what lubricate. Thickeners just hold the lubricant in place.
-
5S every detail of your lubrication program, especially the lubricant reception area. Immediately take the lubricant to the properly marked lubricant storage area. Any world-class lube room has a specific area for every little thing, especially for drum storage. As we always say, 5S the lube room to the extreme. Make storage of lubricants and parts easy, where anyone off the street could walk in and know exactly where every tool and container goes.
-
Take a proper sample from each drum of oil that goes into critical equipment. Coinciding with tip number one, drums of oil are frequently mislabeled. If we are talking about a world-class lubrication program, then sampling new drums is simply a no-brainer. The two primary reasons to sample new drums are to check for the correct oil and get a good particle count of that new oil. New oil is not clean oil, and if the plant has cleanliness and dryness targets (an essential part of being a world-class plant), then we need to know how dirty that new oil is and how much moisture is in that oil. After figuring that out, we can determine how much the lubricant needs to be filtered and dehydrated before being put into service.
-
Have written procedures posted conspicuously on the walls, in the digital receiving system and pretty much anywhere else that you could possibly put a document where it will be viewed often in the receiving area. When personnel see the procedure constantly, it becomes second nature. Psychologically, there is something to constant reinforcement of change. When you walk through the door at work, and everyone is talking about the new way to do things, and everyone is on board with the new way, then that becomes the way.
-
Speaking of “the new way,” effective quality control starts with culture, and culture starts with morale. If the workplace's morale is low, personnel will be more resistant to change. If the morale is high, they will be more receptive to change. For example, if morale is low, then employees are more likely to have a “don’t care” attitude. A demoralized workplace is one of the most depressing environments to be in, and it becomes contagious; on the other hand, so does a positive workplace.
-
Trust and verify. Trust that your technicians are doing the correct procedures and taking precautions when it comes to receiving new lubricants. However, always verify that they are upholding the standards set by the facility on receiving new lubricants. After all, a lube program is only as strong as the foundation allows it to be.
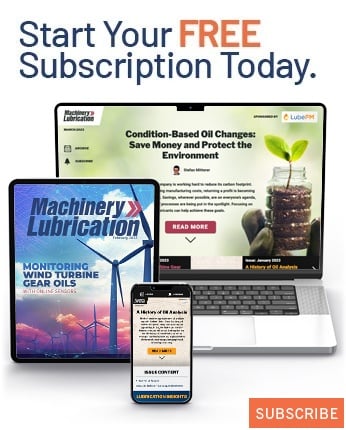