The Importance of Training in Machinery Lubrication
- Enhanced Equipment Performance: Well-trained lubrication technicians can identify the right lubricant for each piece of machinery, ensuring optimal performance and reducing downtime.
- Cost Savings: Proper training reduces the likelihood of equipment failure and unplanned maintenance, leading to significant cost savings in the long run.
- Safety and Compliance: Training ensures that all lubrication practices meet safety standards and regulatory compliance, reducing the risk of accidents and legal issues.
- Innovation and Adaptability: Continuous training helps technicians stay updated with the latest advancements in lubrication technology, enabling them to implement innovative solutions and adapt to new challenges.
Key Components of Effective Training Programs
- Hands-On Training: Practical, hands-on training is essential for technicians to gain real-world experience. This can include workshops, simulations, and on-the-job training sessions.
- Certification Courses: Enrolling technicians in certification courses from reputable organizations, such as the International Council for Machinery Lubrication (ICML), ensures they possess the necessary skills and knowledge.
- Continuous Learning: Training should not be a one-time event. Implementing continuous learning opportunities, such as refresher courses, webinars, and industry conferences, keeps technicians updated with the latest trends and technologies.
- Mentorship Programs: Pairing less experienced technicians with seasoned professionals fosters knowledge transfer and skill development, creating a robust talent pipeline.
Talent Management: Nurturing the Next Generation of Lubrication Experts
- Attracting Talent: Organizations must highlight the importance of lubrication roles and the potential for career growth to attract top talent. Partnering with technical schools and universities, offering internships, and participating in career fairs can help raise awareness and interest in lubrication careers.
- Developing Talent: Beyond initial training, providing career development opportunities is crucial. This can include advanced training programs, leadership development courses, and opportunities for cross-functional projects.
- Retaining Talent: Retention strategies should create a supportive and engaging work environment. Competitive compensation, recognition programs, and clear career paths increase job satisfaction and loyalty.
- Succession Planning: Identifying and grooming future leaders ensures continuity and long-term success. Succession planning involves assessing current talent, identifying potential leaders, and providing them with the necessary development opportunities.
Best Practices for Implementing Training & Talent Management Programs
- Needs Assessment: Conduct a thorough needs assessment to identify skill gaps and training requirements. This ensures that the training program is tailored to the organization's specific needs.
- Collaborative Approach: Involve key stakeholders, including senior management, HR, and technical experts, in the development and implementation of training programs. A collaborative approach ensures alignment with organizational goals and objectives.
- Utilize Technology: Leverage technology to enhance training and talent management efforts. Online learning platforms, virtual simulations, and data analytics can improve training effectiveness and track progress.
- Feedback and Evaluation: Regularly evaluate the effectiveness of training programs through feedback from participants and performance metrics. Continuous improvement ensures that training programs remain relevant and effective.
- Cultural Integration: Foster a culture of continuous learning and development. Encourage employees to take ownership of their professional growth and provide support through resources and incentives.
Conclusion
Supplier Spotlight
Pulsarlube USA 1480 Howard St., Elk Grove Village, IL 60007 847-593-5300 | Pulsarlube.com
Pulsarlube provides the most innovative and reliable Automatic single-point lubricator on the market. Backed by years of research and development, Pulsarlube offers a wide range of superior products to meet the needs of our customers. Pulsarlube provides high-quality products and services worldwide through its well-established distribution network.
Royal Purple One Royal Purple Lane, Porter, TX 77365 281-354-8600 | RoyalPurple.com/industrial/
Formulated for demanding industrial operation needs, Royal Purple® high-performance synthetic lubricants improve reliability, extend drain intervals, reduce lubricant consumption, lower operating temperatures, decrease downtime, and reduce maintenance and energy costs- transforming your Total Cost of Ownership into an investment in excellence.
Noria Education 1328 E. 43rd Court, Tulsa, OK 74105 800-597-5460 | Noria.com/Training
Take the guesswork out of machinery lubrication with Noria's education and training. Learn precision lubrication skills for maximizing machine reliability. Most maintenance programs achieve only 10 percent of the benefits available from oil analysis. Learn how to unlock the full potential of your oil analysis program.
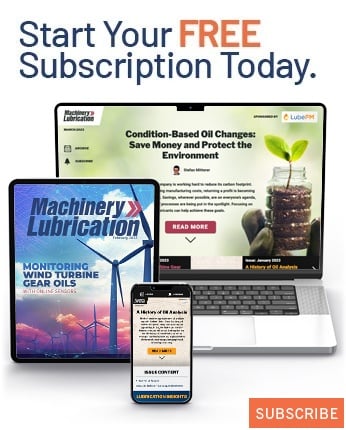