What is a Single-Point Lubricator?
A single-point lubricator is a device engineered to attach to a single unit to regularly and automatically deliver a small amount of clean grease or lubricating oil to a specific area. It is often used to keep bearings lubricated but can also be used to lubricate pumps, electric motors, fans, chains and conveyors, among other applications. Manually greasing bearings often result in over- and under-greasing, eventually leading to premature bearing wear. Single-point lubricators can be configured to dispense the correct lubricant quantity to a single point for a predetermined period. Single-point lubricators are a popular method of extending the life of bearings and other components and preventing extended downtime due to lubrication-related failures. While there are many types, the most common are spring-loaded, electrochemical and electromechanical.
Figure 1: A spring-loaded single-point lubricator.
Figure 2: An electromechanical single-point lubricator.
Figure 3: An electrochemical single-point lubricator.
Why use a Single-Point Lubricator?
Single-point lubricators are designed to give a consistent, measured and continuous supply of fresh grease or lubricating oil. Some applications are hard to reach, unsafe to get to or may require a lot of excess grease. You will use a single-point lubricator to add the grease more frequently than if you could do it manually. Some suitable environments for single-point lubricators include:
-
Harsh environments
-
Inaccessible or hard-to-reach areas
-
Food processing and pharmaceutical industries
-
High-contamination environments
-
Remote or unmanned locations
-
Automated production lines
-
High-vibration environments
-
Outdoor installations
It's essential to select the right type of single-point lubricator for each specific environment and application to ensure optimal performance, equipment protection and cost-effectiveness.
Why inspect a Single-Point Lubricator
Inspecting a single-point lubricator is important for several reasons:
-
Ensuring proper lubrication: Regular inspection helps ensure that the lubricatordispensesg the correct amount of lubricant to the designated point, which is crucial for maintaining optimal equipment performance and reducing friction between moving parts.
-
Detecting leaks or blockages: By inspecting the lubricator, you can detect any leaks or blockages that might hinder the lubrication process, leading to inadequate lubrication and potential equipment damage.
-
Monitoring lubricant levels: Inspecting the lubricator allows you to check the lubricant level, ensuring there's enough lubricant available for the required application. This helps prevent the equipment from running dry and causing premature wear or failure.
-
Verifying lubricant quality: Over time, lubricants can degrade or become contaminated, which can negatively impact their performance. Inspecting the lubricator allows you to assess the quality of the lubricant and determine if it needs to be replaced.
-
Maintaining equipment reliability: Proper lubrication is essential for maintaining the reliability and longevity of your equipment. Regularly inspecting the single-point lubricator helps identify potential issues before they escalate into costly equipment failure or downtime.
-
Complying with maintenance schedules: By inspecting the lubricator, you can ensure that you are adhering to the recommended maintenance schedules, which can help extend the life of your equipment and minimize the risk of unexpected breakdowns.
-
Maximizing cost-effectiveness: Efficient lubrication helps reduce energy consumption and overall operating costs. By inspecting the single-point lubricator, you can ensure that it is functioning optimally, which in turn contributes to cost savings for your business.
Inspecting a Single-Point Lubricator
Step 1: Gather the appropriate tools required to perform the procedure
Step 2: Clean the outside of the single-point lubricator with a lint-free, industrial towel
Step 3: Examine the purge point and clean any purge lubricant; clean with a pipe cleaner if there is an obstruction
Step 4: Inspect the single-point lubricator
Step 5: Activate the test function to check performance
Step 6: Verify the timer is adjusted according to the correct lubrication frequency
Step 7: Check for overgreasing and make a note
Step 8: If any abnormal condition is found, report it
Step 9: Check the grease level in the single-point lubricator and report
Step 10: Note the date of the last inspection and confirm the lubricant consumption is according to the time elapsed
Step 11: Note the date and level of the current inspection
Don't forget to collect all tools used during the procedure, wipe up any spilled lubricant and dispose of all consumables used in the inspection.
Key Takeaways
-
Verify you have the correct single-point lubricator
-
Mark the amount with a permanent marker
-
Make sure the unit is operating as intended
-
Be aware of vibration and temperature
-
Keep it clean
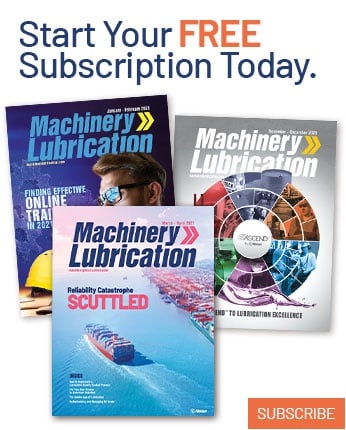