In today's fast-paced industrial environment, machinery efficiency and longevity are paramount. One critical factor in achieving this is a well-structured lubrication program. Lubrication programs are not just about applying oil or grease; they are comprehensive strategies to ensure machinery operates smoothly, reduce downtime, and extend equipment life. This article delves into best practices for developing a robust lubrication program, the necessary training, and the steps to implement it effectively.
The Importance of Lubrication Programs

Developing a Lubrication Program
Assessment and Planning
- Machinery Audit: Begin with a thorough audit of all machinery and equipment. Identify lubrication points, types of lubricants required, and current lubrication practices.
- Objective Setting: Define clear objectives for your lubrication program. These include reducing downtime, extending equipment life, or improving energy efficiency.
Lubricant Selection
- Compatibility: Choose lubricants compatible with your machinery and operating conditions. Consider factors like temperature, load, speed, and environmental conditions.
- Supplier Collaboration: Work closely with lubricant suppliers to ensure you use the best products.
Lubrication Schedule
- Regular Intervals: Establish a lubrication schedule based on the manufacturer's recommendations and your machinery's operating conditions. Regular lubrication prevents wear and tear.
- Automated Systems: Consider implementing automated lubrication systems for continuous and precise lubrication, reducing the risk of human error.
Documentation and Record-Keeping
- Lubrication Logs: Maintain detailed logs of lubrication activities, including dates, types of lubricants used, and observations about machinery performance.
- Software Tools: Utilize lubrication management software to streamline record-keeping and ensure consistency.
Monitoring and Analysis
- Oil Analysis: Regularly conduct oil analysis to monitor the condition of lubricants and detect potential issues before they become critical.
-
Trend Analysis: Analyze trends in lubrication data to identify patterns and make informed decisions about maintenance and lubricant selection.

Training and Education
Basic Training
- Lubrication Fundamentals: Train staff on the basics of lubrication, including types of lubricants, their properties, and how they interact with different machinery components.
- Application Techniques: Educate on proper lubrication techniques, ensuring the right amount of lubricant is applied at the correct intervals.
Advanced Training
- Oil Analysis: Provide advanced training on oil analysis techniques, enabling staff to interpret results and take proactive measures.
- Troubleshooting: Equip your team with the skills to troubleshoot lubrication-related issues, such as identifying the causes of lubricant degradation or contamination.
Continuous Education
- Workshops and Classes: Encourage participation in industry workshops and classes to stay updated on the latest lubrication technologies and best practices.
-
Certifications: Support staff in obtaining certifications from recognized bodies like the International Council for Machinery Lubrication (ICML).

Best Practices for Lubrication Programs
Standardization
- Lubrication Standards: Develop and adhere to lubrication standards across your organization. Standardization ensures consistency and reduces the risk of errors.
Cross-Functional Collaboration
- Team Effort: Involve cross-functional teams in developing and maintaining the lubrication program. Collaboration between maintenance, operations, and procurement ensures all aspects of lubrication are considered.
Continuous Improvement
- Feedback Loops: Establish feedback loops to assess and improve your lubrication program continuously. Regularly review performance data and adjust practices as needed.
- Innovation: Stay open to adopting new lubrication technologies and practices to enhance your program's effectiveness.
Safety and Environmental Considerations
- Safety Protocols: Implement safety protocols to protect personnel during lubrication activities. This includes proper handling and disposal of lubricants.
-
Environmental Impact: Consider the environmental impact of your lubrication practices. Opt for eco-friendly lubricants and practices that minimize waste.
Conclusion
Supplier Spotlight
Pulsarlube USA 1480 Howard St., Elk Grove Village, IL 60007 847-593-5300 | Pulsarlube.com
Pulsarlube provides the most innovative and reliable Automatic single-point lubricator on the market. Backed by years of research and development, Pulsarlube offers a wide range of superior products to meet the needs of our customers. Pulsarlube provides high-quality products and services worldwide through its well-established distribution network.
Fluid Metrics 4514 Chamblee Dunwoody Rd. #252, Dunwoody, GA 30338 p: 770-393-8636, f: 770-393-8631 | FluidMetrics.com
Founded in 2003 by a compressor industry veteran, Fluid Metrics utilizes the latest lubrication technologies to maximize compressor performance and reliability. When combined with a proactive, condition-based maintenance plan, our advanced compressor oils, purifiers, and conditioners are proven to dramatically increase compressor reliability, slash your oil and parts consumption, and save you time and money. Give us a call today to learn how much easier and better compressor oil maintenance can be.
Royal Purple One Royal Purple Lane, Porter, TX 77365 281-354-8600 | RoyalPurple.com/industrial/
Formulated for demanding industrial operation needs, Royal Purple® high-performance synthetic lubricants improve reliability, extend drain intervals, reduce lubricant consumption, lower operating temperatures, decrease downtime, and reduce maintenance and energy costs- transforming your Total Cost of Ownership into an investment in excellence.
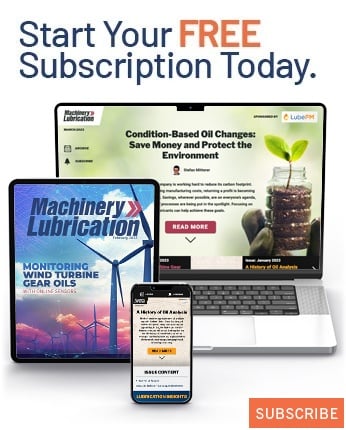