Lubricants are essential for the efficient operation of all machinery, to reduce friction, wear, and corrosion while ensuring smooth performance. These lubricants are made up of base oil and a package of additives. The base oil provides the most fundamental role of a lubricant via the viscosity to form a lubricant film that separates relative moving surfaces. Depending on the application, different additives are carefully selected to enhance lubricant performance. Each additive will either:
- Enhance a desirable property of the base oil
- Suppress an undesirable property of the base oil or
- Add a new property of which that base oil does not provide
These additives include oxidants inhibitors, corrosion inhibitors, viscosity index improvers, foam inhibitors, anti-wear additives, detergents, and more. Each serves a core function, typically indicated by its name. However, while each additive implies an ability to “inhibit” oxidation or “improve” the viscosity index, this ability is not unlimited and does not exist without a need for caution. Over time, additives are exposed to conditions which cause them to diminish their ability, or more simply, to deplete. Often, it’s the core purpose of the additive that can become its demise.
The Role of Additives in Lubricants
Additives are crucial in extending the life and performance of lubricants. Their functions are broadly categorized into three groups:
- Enhancing Properties: For instance, viscosity index improvers enhance the viscosity stability of the lubricant across a range of temperatures.
- Suppressing Undesirable Properties: Each oil has a pour point, which is the temperature at which the lubricant begins to solidify. This undesirable property is suppressed by pour point depressants helping maintain the oil’s fluidity down to a lower temperature.
- Adding New Properties: Anti-wear additives provide additional protection against surface wear, a property not inherent to the base oil at low relative surface velocity or too much load.
Despite their effectiveness, additives have limitations. They are subjected to various stressors within the machinery, which leads to their eventual depletion. Understanding the mechanisms behind this depletion is crucial for effective lubricant management.
Let’s Take for Example… Oxidation Inhibitors
Oxidation inhibitors, also known as antioxidants, are designed to delay the onset of oxidation and the resulting negative consequences including acid formation, varnish and the buildup of sludge. Oxidation occurs when the lubricant chemically reacts to oxygen, like when exposed to water and air seen in Figure 1. This decomposes the oil and turns it into a highly reactive molecule, such as a hydroperoxide. The reason the oxidation inhibitor delays oxidation instead of prevents oxidation, is because it is sacrificial and loses its functionality as it performs its job. The oxidation inhibitor stops the hydroperoxide from reacting further with other oil molecules (Figure 2.), halting the oxidative chemical chain reaction. But in the process, the oxidation inhibitor is sacrificed, and the bulk additive has become gradually depleted.


Similar to oxidation, most additives can become depleted over time due to their exposure to various conditions. This is both a good thing and a bad thing. A good thing, because in the short term it’s performing its function by delaying the oxidation of the lubricant. It’s bad because overtime, it has lost a percentage of its additive concentration. In the case of the antioxidant, it has lost “oxidative life” resulting in the build-up of sludge, tar, varnish and generate acids.
Mechanisms of Additive Depletion
Let’s cover the three primary mechanisms: decomposition, physical removal, and adsorption.
#1 - Decomposition:
Oxidation: Oxidation inhibitors, such as zinc dialkyldithiophosphate (ZDDP) and hindered phenols, are designed to delay the onset of oxidation (see oxidation inhibitor example above).
Hydrolysis: Water and heat cause the chemical breakdown of certain additives. For example, ZDDP can hydrolyze, leading to the formation of sulfuric acid and hydrogen sulfide, which can further degrade the lubricant.
Thermal Degradation: As operating temperatures increase, thermal degradation of additives can occur. This is particularly true for additives that are sensitive to heat, such as certain antioxidants and viscosity index improvers.
Neutralization: Certain additives, like over-based detergents, are designed to neutralize acids that come into the oil as contaminants. They sacrifice themselves in this process, depleting over time due to this exposure. If not monitored correctly, the oil can become corrosive to the machine if it continues in service after most of the over-based detergents are depleted.
Shear-Down: The larger the molecule, the more likely they will be susceptible to breaking of the molecular chains under shear effects. This is particularly true for viscosity index improvers.

#2 - Physical Removal (Mass Transfer):
Condensation Settling: If additives become insoluble due to contamination, temperature, or other operating conditions, they will become more prone to settling out by gravity to the bottom of a sump.
Filtration: Solid or condensed additives can be physically removed from the lubricant through filtration. Solid additives that may experience this include silicone Defoamants or Borate EP additives. In other cases, additives that are adsorptive to contaminants may also become trapped by the filter when the particles they are attached to are filtered out.
Centrifugation: High centrifugal forces can cause organometallic additives to separate from the lubricant. Centrifugal filtration used in some applications to remove contaminants may have this added consequence.
Evaporation: While uncommon, certain additives can evaporate, particularly when vacuum dehydrators are used to remove water from the lubricant.
#3 - Adsorption:
Surface Adsorption: Polar additives, like EP (extreme pressure) and AW (anti-wear) additives, can adhere to machine surfaces, forming soap-like boundary films to protect against friction and wear. While this provides immediate protection, it depletes the additive concentration in the lubricant as they make themselves ready to perform their job.
Particle Scrubbing: Additives can be attracted to particles due to additive polarity*, thus trapped and dragged to sump floors or filters. This process, known as particle scrubbing, removes additives from circulation within the lubricant.
*What is Additive Polarity? This is the natural directional attraction of additive molecules to other polar materials in contact with the oil and enables the additive to perform its primary role or attaching to surfaces, particles or other contaminants.
Water Washing: As water is a polar material, it can wash away additives, dragging them to the sump floor, especially in environments where water contamination is high.

Monitoring and Managing Additive Levels
To ensure the lubricant continues to provide the longevity and effectiveness over its intended service interval, it is essential to regularly monitor additive levels through oil analysis and take proactive measures if they are nearing depletion.
Best Practices to monitor or maintain additive levels:
- Regular Lubricant Analysis: Testing instruments such as Fourier Transform Infrared Spectroscopy (FTIR), elemental analysis, and Linear Sweep Voltammetry (LSV) can monitor the conditions of certain additives depending on the elemental or molecular structure. FTIR, for example, can monitor multiple oil parameters, including additive molecules (like antioxidants and dispersants) and the consequences of depleted additives (such as oxidized oil molecules).
- Using High-Quality Lubricants: Opting for lubricants with more robust additive packages can enhance resistance to depletion and extend the life of the oil to match an intended service interval.
- Proper Storage and Handling: Maintaining optimal storage conditions and handling procedures minimizes the risk of contamination and unfavorable conditions that could lead to additive depletion or degradation.
Monitoring additive performance can also be measured through tests designed to calculate the lubricant's overall robustness. For example, Rotating Pressure Vessel Oxidation Test (RPVOT) can measure the remaining oxidative life of the lubricant by evaluating its resistance to oxidation under controlled scenarios. This often correlates very closely with the depletion of all types of antioxidants in the oil.
Proactive Measures
Perhaps the most effective way to mitigate the negative effects of additive depletion is to minimize what is first known as the root cause leading to additive depletion. You’ll notice this often relates to the contaminant influences during storage, transfer, and the machinery’s operating environment. Maintaining recommended parameters reduces stress on the lubricant and its additives.
Reducing the ingression of water and particulate contamination helps preserve additive presence and effectiveness when they are most needed. Temperature also has a dramatic effect on additive depletion, particularly those that relate to decomposition. This is because decomposition is a chemical reaction and it is known through the Arrhenius Rate Rule that these reactions will occur twice as fast for every 10° Celsius increase.
Case Studies and Data
Case Study 1: Trending an Oil’s RPVOT Life
Scenario: Monitoring the RPVOT life of a slow-speed high-horsepower oil-lubricated motor bearing oil.
Findings: The new oil had an RPVOT value of 600 minutes. While the used oil showed a gradual decline, the measurement after a few months was down to 330 minutes. This trend indicated progressive depletion of antioxidants and indicating about a 55% Remaining Useful Life (RUL) of the oil, necessitating timely intervention to replenish or replace the lubricant.
Case Study 2: Risks of Mixing Lubricants
Scenario: Mixing lubricants from different brands and formulations.
Findings: The mixture of two oils in a gearbox was initially viewed as inconsequential as the two were intended for the same application. Although, when they are mixed, the additives became antagonistic to each other. This led to a steady additive precipitation, loss of anti-wear performance, and reduced oxidation stability. The gradual nature of this depletion resulted in the life of the oil to be reduced by 75%. But given the effects were not immediate, the failure mode was not recognized, and the scenario was unfortunately repeated on other similar machines at the plant. This was not recognized until oil analysis trends were scrutinized, realizing the effects of mixing oils. To avoid such issues, it is crucial to test planned mixtures for compatibility and retest frequently.
What to Take Away
Understanding how additive depletion occurs in lubricants is vital for maintaining machinery reliability and performance. By recognizing the mechanisms behind additive depletion and implementing best practices for monitoring and managing additive levels, industries can extend the life of their lubricants and ensure optimal machinery operation. Learn the skills and benefits of properly performing regular oil analysis and implement proactive measures that address the root cause. Preventing the adverse effects of additive depletion ultimately leads to improved efficiency and reduced maintenance costs.
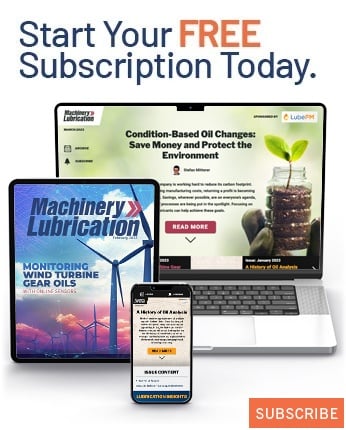