![]() |
Submitted by |
History:
-
Seminole Electric is a 1300 MW coal-fired power plant located in Palatka, Fla.
-
Seminole recently converted its scrubber effluent from landfill material into synthetic gypsum. Many new types of equipment were installed for this conversion process; some old equipment was required to run in and out of the original design parameter.
-
132-M, paddle mixer, gear reducer, was one such piece of equipment. In its new operating parameter, it was failing on average every three to four weeks, sometimes sooner.
-
The average cost per failure was about $5,000 for the swap out and rebuild of the failed unit. Replacement of the mixer with a different style had been considered at a cost of around $100,000, not including labor.
Laboratory Lubricant Analysis:
-
The sample was collected from a midpoint oil level plug after the plug was pulled and fluid was flushed and allowed to run out so that a clean sample could be collected.
-
Lab performed spectrometric analysis, FTIR, viscosity and particle count. The technician requested a ferrogram and wear debris analysis because metal particles were detected during visual inspection.
![]() |
![]() |
![]() |
Evaluation:
-
Rubbing wear was found in the sample, in addition to moderate nonmetallic inorganic particles.
-
Suspecting fly-ash as the contaminant after reading the results, the Seminole technician ran a patch test and his assumption was confirmed.
-
The input gear was apparently wearing down until no gear mesh was left, resulting in the final stripping of the teeth. Significant damage to the bearings had also been seen from a lapping compound formed when the fly-ash mixed with the oil.
Solution:
-
The first line of defense was to select an increase in oil viscosity. This gear reducer had been running eight to ten hours per day and was now operating up to 24 hours per day. Due to the load and temperature changes, the ISO 150 EP gear oil was increased to ISO 320 EP gear oil. At the same time, a 2-micron moisture-removing breather was installed ($46).
-
While the breather helped, the shaft seals were still the main area of ingression. To correct this, bearing isolators were installed, on all three shafts for $949. Though expensive, these seals worked great. During the first six weeks of operation with the bearing isolators installed, oil samples were taken at one week, two weeks and four weeks. The samples were very clean. Compared to previous samples, you could still see through them. There were slight traces of metal from the gear-mesh, however, this was considered as a possible normal gear break-in effect.
-
A kidney-loop filtration unit with 10- and 3-micron nominal filters, $2,070, was installed next. This was temporarily wired and is run each time the mixer is in use.
-
Final plans are to have this wired in through the PLC, so it will automatically run and shut down when the mixer is in service.
Impact:
-
$3,065 was the total bill for the improvements made. The mixer gear reducer has now been in use for more than six months, and has surpassed previous mixer gear reducer longevity.
-
The oil was changed after three months while the plant was down.
-
Upon visual inspection, the sample looks as good as new oil and will be sent to the lab for further evaluation.
-
This gear reducer, which started at an ISO code of 25/22, is now running at a code of 20/17 and has already realized eight times the initial investment in savings.
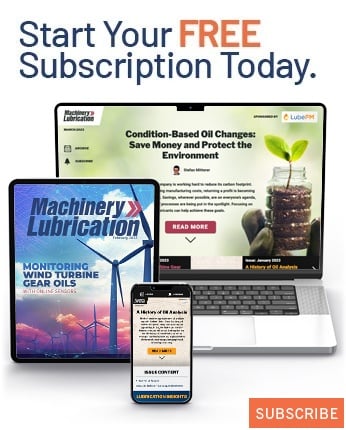