In industrial manufacturing, condition monitoring is a critical process that can help ensure equipment reliability, maximize operational efficiency, and avoid costly unplanned downtime and repairs.
Through continuous tracking of equipment and asset health, condition monitoring provides the foundation for predictive maintenance strategies that enable early detection of potential issues — allowing operations to address problems before they escalate. This approach not only extends equipment life but also reduces unplanned outages, leading to more cost-effective operations.
Condition Monitoring and Predictive Maintenance
To use a sports analogy, using condition monitoring and predictive maintenance is like playing offense instead of defense with your equipment. Traditional preventive maintenance is a reactive strategy and mindset, where predictive maintenance is proactive.
At the heart of conditioning monitoring is data-driven analysis — collecting and using data to make better informed decisions about how to operate equipment and the overall manufacturing operation. This may include process data that helps evaluate the overall manufacturing process as well as equipment and asset data for each machine that can answer questions about throughput rates and asset health.
Predictive maintenance uses sensors and technology to take in data at a high rate, often continuously in real time. This allows operations to make informed, planned maintenance decisions based on actual equipment health. The data can also be used to adjust the overall manufacturing process to improve efficiency, productivity, and throughput.
Benefits of Condition Monitoring
Industrial operations that use condition monitoring and predictive maintenance can see several significant benefits, including:
-
Improvedequipment reliability and lifespan, increasingthe amount of time between failures.
-
Decreased unplanned downtime and maintenance costs.
-
Greater production due to improveduptime and equipment availability.
-
Improved safety and compliance, since employees can check equipment health without exposing themselves to high-risk environments.
-
A shift away from stressful, reactive break-fix situations with down equipment to proactive maintenance practices.
-
Reduced part inventory, allowing companies to be as efficient as possible with order costs and the manpower schedule for part changeover and repairs.
-
Ensured compliance with industry standards and regulations using condition monitoring and data tracking.
All of these benefits tie directly back to improving the overall effectiveness and efficiency of the operation. In addition, giving maintenance personnel the tools for more proactive equipment upkeep is especially critical in large facilities where there are hundreds or even thousands of machines to maintain.
In one real-world example, a large aluminum mill facility installed torque sensors on their reversing mill drive shafts. An analysis of the data provided insight into component trends and suggested the need for a targeted inspection. The company was able to plan the inspection and have the necessary parts on hand — and they were able to swap the coupling components before failure occurred. Prior to the use of the sensors for condition monitoring, the facility averaged four component failures annually that cost $350,000 each in hardware and rebuilding costs. Since they began using data for predictive maintenance, they have had zero catastrophic failures on that equipment, saving more than $1 million per year.
Best Practices for Implementing Condition Monitoring
When determining a strategy for implementing condition monitoring and predictive maintenance, these best practices can help you optimize the outcomes and achieve success.
Tip 1: Define your goals
First, identify and understand your operational challenges and whether condition monitoring can help mitigate them. Then determine the goals and outcomes you have for condition monitoring. Are you looking for improved operational efficiency, reduced uncontrolled downtime, or greater throughput? Identifying your success criteria and priorities will help in finding the right solution that is tailored for your needs.
Tip 2: Develop a comprehensive strategy
Next, document your planned strategy for implementing condition monitoring and predictive maintenance. This is an important step to ensure that the strategy aligns with your broader business objectives. Lay out your goals, KPIs, and any performance metrics. This is key to building the right foundation for your monitoring strategy and delivering a return on investment. Your current maintenance and inventory strategy can help you identify the most impactful opportunities for condition monitoring based on equipment criticality and overall risk to production output. There is no one-size-fits-all strategy.
Tip 3: Focus on shifting the mindset
Moving from preventive maintenance to predictive maintenance often involves a change in the mindset of the various employee groups involved. From equipment maintenance staff up to the C-suite, this is a multistep process that involves internal adoption and buy-in to achieve success. Training and workforce development are key to helping staff understand the benefits this process can provide, both to their role and the overall operation. The maintenance staff may already be doing a good job with preventive maintenance, but they need to understand how this process takes it a step further into predictive maintenance. Perhaps they use vibration sensing equipment, but that data is not being analyzed to determine trends. Without proper analysis, they are still in a reactive maintenance mindset.
Tip 4: Choose the right partner
Looking for a condition monitoring solutions provider that is also a partner will help you optimize the data gathered, as well as the analysis of that data and results of the process. Choosing the lowest-cost solution may not always provide the best ROI, as it may provide basic information but not the in-depth insight and analysis that a more experienced partner can provide. Look for a partner with deep industry expertise and a diverse portfolio of tested components and capabilities. This will allow you to get multiple technologies and solutions, as well as support, from a single source.
Future Trends in Condition Monitoring
Emerging technologies in condition monitoring and predictive maintenance will continue to have an impact on these applications in the coming years. As technology advances, there will be even faster data collection and greater cross-communication between platforms and devices.
Companies that invest in condition monitoring now can position themselves to take advantage of the next generation of this technology and maximize the benefits of future advancements. This forward-thinking approach can improve current operational efficiencies and also ensure readiness for the technologies on the horizon.
As expected, the falling costs of sensors, improvement in battery capabilities, and advances in wireless technologies have enabled sensors to be deployed in ways that have previously been considered cost prohibitive. This will continue with wireless vibration and temperature sensors and will also continue to expand into other sensing modalities. Especially with rotating equipment, wireless sensors will also open new possibilities where wired solutions may have been impractical or impossible.
The growth of AI is another factor that cannot be ignored. While some people fear that AI will take away jobs, it is much more likely that AI will significantly enhance the productivity of existing resources in these applications, allowing people to do more than they could have previously imagined. This ties into the focus of Industry 5.0: enabling people to get more done more efficiently.
The Evolution of Machine Maintenance
The rise of condition monitoring and predictive maintenance is an evolution in how companies handle asset maintenance — and how they can become more efficient in these efforts. Incorporating condition monitoring into a strategic maintenance plan can significantly improve equipment reliability, reduce unexpected downtime, and drive operational efficiency. Embracing these practices not only strengthens productivity but also supports long-term sustainability and competitiveness in the industry.
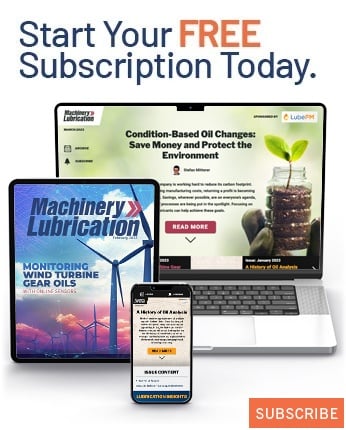