Let’s be real—when many people hear the words “lubrication program,” they picture a dusty grease gun in the back of the maintenance shop or a drum of oil collecting grime in a corner. But a properly functioning lube program can be the heartbeat of your plant – quite literally. And within that program, the proper handling and application of lubricants is where the magic—or the mayhem—really begins. Think of it like cooking a great meal: You can have the finest ingredients (in our case, our carefully selected lubricants) with the potential to make a world-class meal, but if you don’t store them carefully, toss them around carelessly, or inappropriately mix them, the end result can become an unappetizing mess in a hurry.
So let’s break down what this whole handling-and-application business really means and why it’s the unsung hero of your reliability efforts.
What Are We Actually Talking About?
Lubricant handling refers to the way lubricants are received, stored, transferred, and transported within a facility. Application, on the other hand, is the moment of truth—it’s how that lubricant is actually introduced to the machine: what lubricant, how much, how often, and where.
Together, they form the backbone of a successful lubrication program. Or, to keep with our previous analogy: handling is your prep work, and application is the actual cooking. You mess up either one, and you’re serving up reliability issues with a side of downtime.
Why It Matters
Lubricants are engineered to work a certain way, in a certain environment, on certain components. Contaminate them, store them wrong, or dump in too much (or too little), and suddenly you’re no longer preventing friction—you’re inviting failure.
Water, dirt, and air are the biggest villains—they cause oxidation, corrosion, and wear before the oil even hits the asset. Improper handling and sloppy application allow these contaminants into the oil and can turn perfectly good lubricants into ticking time bombs.
The Perks of Doing It Right
Proper handling and careful application put a shield around your assets, keeping contaminants out, your lubricant films intact, and preventing premature degradation. When lubricant handling and application are done right, everything just works better.
- Machines run smoother and longer.
- Unplanned downtime takes a nosedive.
- Maintenance teams can stop fighting fires and start preventing them.
- Money gets saved in buckets, not drips.
It’s not just about extending the life of the oil, either. It’s about extending the life of your assets. Proper handling and application means bearings don’t fail early. Pumps don’t seize up. Motors don’t overheat. Basically, you're giving your equipment the VIP treatment, and it pays off.
The Hurdles to Getting It Right
Of course, if it were easy, everyone would already be doing it. The truth is, good handling and application take a bit of discipline and planning.
Some of the usual suspects holding people back:
- Lack of training: People can’t follow best practices if they’ve never been taught what they are.
- Improper storage: Oils stored outdoors, in the wrong containers, or near contamination sources are already compromised.
- Time pressure: When equipment is down, there’s a temptation to cut corners and “just get it running.”
- Equipment gaps: No labeling system, no color coding, no dedicated transfer containers? You’re asking for cross-contamination.
Fixing these isn’t impossible—it just takes commitment and some upfront effort.
What “Good” Looks Like
So what does proper lubricant handling and application actually look like in the wild?
It starts with keeping your lubricants clean, cool, dry, and clearly labeled. That means a clean, orderly and organized lube room. That means sealed, climate-controlled storage. That means using tools like filter carts and dedicated transfer containers (not that old coffee can) to keep oil clean even during transfer.
Once at the asset, you apply lubricants based on hard data like OEM specs or oil analysis—not gut feel. You apply them with calibrated tools using a purposeful process. You document quantities and intervals.
And when you really dial it in, the entire team knows what lubricant goes where, how often, and why it matters. Eventually, it becomes second nature—like checking the oil in your car before a road trip.
Building a Plan That Works
Want to get started with proper handling and application procedures at your own site? The easiest way is to start small, but smart.
Walk through your current process like a detective—where does oil go from the time it arrives to the moment it hits a machine? Identify the sketchy spots: Is the storage area dirty? Are open containers common? Is there a labeling system, or is everything labeled “Misc. Oil”?
Once you know the gaps, begin drafting your plan:
- Where and how should lubricants be stored?
- What transfer tools will you use?
- How will application be trained for and tracked?
It’s also imperative to loop in your team early—they’re the ones who’ll make or break the plan in real life. Offer them training, not just rules. Show them the “why,” not just the “what.” Finally, measure the results and be sure to celebrate wins like cleaner oil, fewer failures, and smoother operations.
Bottom line? Handling and applying lubricants the right way isn’t just a checkbox. It’s the difference between subpar (or at best, average) uptime and truly excellent reliability. Like a great chef respects the ingredients, a great maintenance team respects the oil. And when you do that, your machines—and your bottom line—will thank you.
Supplier Spotlight
Noria Academy 1328 E. 43rd Court, Tulsa, OK 74105 800-597-5460 | Noria.com/Academy
Obtaining certification can be a challenge; new terms, concepts and topics can overwhelm even the most experienced reliability professionals. Training experts all agree that extending the learning beyond the classroom dramatically increases knowledge retention. To aid in this retention and create an innovative student experience, Noria is pleased to offer the Noria Academy app.
RelaWorks 1328 E. 43rd Court, Tulsa, OK 74145 918-392-5058 | RelaWorks.com
Finding the right products can be difficult. Every industry and application is unique. Over-spending and guess work is common. At RelaWorks, we help reliability professionals solve this challenge. Our mission is to provide products for your unique needs and budget. Backed by Noria Corporation’s expertise and legendary customer service, we’re excited to help your reliability program succeed.
LubePM 1328 E. 43rd Court, Tulsa, OK 74105 800-597-5460 | LubePM.com
As a Lubrication Management System (LMS) engineered by lubrication professionals, LubePM helps an organization create accountability to ensure that every lubrication point is carefully maintained, inspected and measured. Ready to take your facility’s Lubrication Management System to the next level with LubePM? We’re ready to help. Simply request more information or schedule a demo.
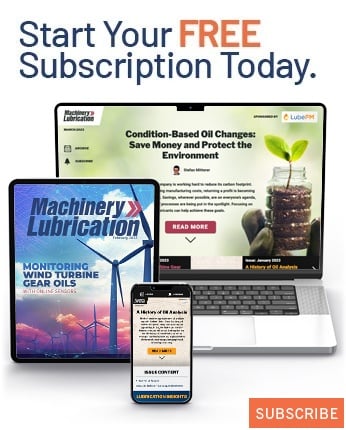