Being a consultant in the reliability field, you often get to see the latest and greatest in condition-monitoring tools and predictive data. It is very easy to get hung up on these tools and overlook simple machine inspections as a source of valuable information. If you have ever sat through one of my presentations or courses, you will often hear me refer to lessons taught to me by my grandfather. Perhaps one of the most influential came when I was a senior in high school working on my Suburban that was giving me problems.
After what seemed like days pouring through a Chilton manual and trying to diagnose some erratic noises and performance issues, my grandfather came to the shop to see how it was going. He asked me to start the vehicle. He listened to if for a moment and then pulled a dollar bill out of his wallet. He placed the dollar bill over the exhaust pipe and watched how it moved. He then put the bill back in his wallet and informed me that I had a burned valve. With that he left the shop and I was left to ponder what just happened. Come to find out, he was right, and I was amazed.
Some of the most impactful machine inspections can be carried out with minimal instrumentation, but it does require an individual that knows what they are looking for. While routine monitoring using vibration analysis, ultrasound, infrared, oil analysis and a litany of other technologies will always be important in providing hard, quantifiable data. The importance of daily inspections by operators and craftspeople cannot be overstated. Having a technician that is around the equipment daily is truly the first line of detection for abnormal conditions.
Early detection of potential failure is the key to minimizing the impact of those failures. While instrumentation will be able to detect faults with more granularity, few pieces of equipment get monitored everyday with these technologies. With the use of real time sensors is gaining popularity, these devices are often reserved for the critical 1-5% of machines. The remaining majority of the equipment falls into routine analysis that may be anywhere from weekly to quarterly analysis. This leaves far too much time between events and the likely hood of catching a failure early is greatly diminished.
However, by training the appropriate equipment on proper inspections; we now have the opportunity to watch the equipment in near real time. It is important to point out that during the failure mechanisms; the goal is to catch the failure as high up on the PF curve as possible. Predictive tools, when used correctly, can certainly catch a failure very high on this curve. Simple machine inspections can catch them high as well, provided they are doing the inspections to a high degree of thoroughness. Simply looking at oil levels and checking for leaks will not likely result in an early catch, but likely result in a “surprise” failure if not corrected.
Inspections can be thought about like using your senses to determine what is going on with your equipment. Often times when the term inspections is used, most tend to think only about visual inspections. While the majority of inspections will have a visual component to them, that is far from the only sense that should be used when ensuring equipment is functioning correctly. Your sense of smell, hearing, and touch are all just as powerful. We will breakdown inspection types by the different senses and discuss what can be determined using each of them.
Visual inspections
Visually inspecting a piece of equipment is more than just what you see, it should also include what you don’t see. As a machine operates, several things in and around it will likely change that indicate potential failures or faults. We can typically lump visual inspections into two categories; internal machine inspections and external machine inspections. Both can be performed at the equipment, but some are more intrusive than others. We want to minimize the exposure of the equipment to the outside environment as much as possible so many of these inspections will require modification of the equipment.
Internal Machine Inspections:
- Check working surfaces – by utilizing inspection windows or during normal maintenance, the internal frictional surfaces should be inspected wear and abnormal deposits. Common surfaces that would be inspected are gears, shafts, bearings and equipment casings. Any showing signs of wear, varnish, scorching or any other defect should be noted and further analyzed before returning to service.
- Magnetic plugs – these simple devices are great for the quick indication of ferrous debris in the systems. While they are crude, it is worth installing them on equipment, especially those that may not be included in a condition-monitoring program. The ferrous debris build-up is certainly a lagging indicator of an issue, but it can be checked and may provide insight into a problem before it turns catastrophic.
- Varnish – as lubricants age and begin to breakdown they produce polar “soft” impurities that exist in a dissolved state with the oil. Once they build to the point that the oil can no longer dissolve them, they become insoluble and begin to build up on machine surfaces. Over time these polar contaminants cure into a hard lacquer-like finish that may require mechanical cleaning to remove. The varnish builds up and impairs movement of the lubricant and even of the machine parts themselves. It can also decrease the heat-transfer capabilities of the equipment.
- Reservoir deposits – the inside of the reservoir should be checked periodically for any buildup of sediment on the bottom, or signs of varnish or rusting on the sides. If the oil has been impaired or grossly contaminated it is common to find a “bathtub ring” along the top side of where the fluid level normally resides. You should also be checking the fluid surface for signs of foaming, air entrainment and emulsified water.
- Filter deposits – filters are like bank vaults filled with valuable information about how our machine is operating as well as how well our contamination control efforts are working. By cutting open and inspecting used filters, you will be looking at what has been flowing through the system and what the machine parts have been exposed to. You would obviously want to look for any metal debris in the filter as well as any unusual contaminants such as paint chips, fibers, or lint. Knowing what is in the filter will allow you to adjust your contamination control strategy.
- Corrosion probes – a common approach to understanding if a lubricant is staying healthy or if water contamination is taking place is by utilizing a corrosion probe in contact with the oil in a system. This probe is periodically checked for signs of varnish build up or rust. Probes of different material such as steel or copper can be used to match the most common metallurgy of the equipment to provide insight into what may be happening on the machine working surfaces that are harder to inspect.
External Machine Inspections
- Oil level sight glasses – while most check these devices quickly just to make sure the oil is at the proper level; there is much more that you can learn by looking at them. You should be looking at the color and clarity of the fluid to see if there is any noticeable darkening of clouding associated with contamination and failure of the lubricant. Also look for indications of foam or emulsions. If you have a laser pointer, shining it into the sight glass will help identify the presence of wear debris as there will be a noticeable sparkling visible.
- Breather ports – most pieces of equipment will have a port through which air is allowed to pass. This is to keep the headspace from becoming pressurized or developing a vacuum which could impact performance and damage components such as seals. The ports themselves should be inspected for evidence of dirt build up or oil misting. Oftentimes the oil will escape the breather port and there will be a spot of dirt that is sticking to the oil wetted surface. You may notice this in areas other than the breather port such as any loose fasteners holding down a hatch. These are good indications that your contamination control strategy likely needs to be improved and the machine might need modification to ensure the breathing is occurring through a breather.
- Breathers – similar to the discussion on breather ports we should inspect the breathers themselves. For canister-style breathers we should check for any signs of oil misting from them and signs of blockage. They should have a date of install written on them and we should be sure they are changed accordingly. For desiccant breathers, we would also want to inspect the color of the silica desiccant inside of them. Most will have a color-change guide of when they are saturated and require changing. A deeper inspection would be looking at the direction of the color change to see if it is indicating the dehumidification of the headspace or dehumidification of the incoming air. Depending on the direction of change, this could give you early warning to a moisture problem inside the machine.
- BS&W bowls – most contaminants are heavier than the surrounding oil and tend to settle to the bottom of equipment housings and reservoirs. Having a window into the bottom regions of the machine allows for the early visual detection of issues. The bottom sediment and water bowl typically thread into a drain port and is a crucial part of any world-class inspection program. These devices will show any water, wear debris, and solid contaminants visually. It also serves as a location to drain accumulated water and take bottom samples if you were to do in-depth analysis on the wear debris.
- Cleanliness – general machine cleanliness should be checked to make sure there is no evidence of an issue such as oil leaks, process leaks, or product accumulation. A machine that is clean and free of debris around it is more likely to run cooler and the lubricant inside is more likely to stay clean. It is very common to walk around equipment and find small drips or product piled up around them. These are early warning signs of seal issues or process leaks that if left unchecked would lead to more disastrous consequences.
- Smoke – while this one is obvious it can often be overlooked. Most think about looking at the smoke or color of the smoke coming out of an exhaust pipe of an engine, but you can also be looking for smoke out of other types of machines. Smoke or steam can be caused by something running very hot and evaporating out water or evaporating oil from the system. The smoke and steam may be very faint but taking your time and looking for it can let you know if the lubricant is performing satisfactorily or if there is moisture contamination. Of course, for engines the smoke is a byproduct of combustion so look at both the color and volume of smoke produced for normal operation.
Audible Inspections
When visiting different facilities and touring them with a seasoned maintenance or reliability professional; it never ceases to amaze me when they stop, pause and say “this machine doesn’t sound right.” Each machine has its own unique sound or serious of noises as it cycles through its operation, and subtle changes in those sounds may indicate an impending failure. While the use of listening devices such as ultrasound has gained popularity and is a great tool, just using a sounding rod, stethoscope, or the naked ear can provide useful information.
- Gear meshing – as gear teeth meet and rotate there is a normal tone that is produced. As this tone shifts to more of “growling” noise it may indicate an issue with backlash within the gearing. Depending on the speed and load of the gears, the noise can be very pronounced. If there are solid contaminants building up in the teeth, you may also hear a popping or crunching noise indicating the breaking down of these solids.
- Cavitation – often described as a banging or marbles rolling in a can noise, this is very pronounced in pumps. Especially if there is water and/or air contamination moving through the pump as well. The collapsing air bubbles or flash vaporization of water to steam makes a very loud noise as it is mechanically damaging the internal pump surfaces. If bad enough, you’ll be able to hear this occurring from several feet away from the pump. In less extreme cases the use of a sounding rod or stethoscope may be needed to determine if it is occurring.
- Engines – if you have driven the same vehicle for an extended amount of time you become familiar with the sounds the engine makes during different speeds and driving conditions. The same is true with stationary engines found in most industrial facilities. You will be listening for any obvious sounds of sputtering or miss-firing, but also listen if you hear any knocking or tapping noises during operations. Any of there can be indicative of a potential mechanical or lubrication issue.
- Bearings – similar to gearing, bearings will produce noise during operation. Being cognizant of what abnormal noises are is the key to early detection. If a bearing is grease lubricated, as the grease dries out the cage of the bearing will begin to rattle. This noise may be minute but is a tell-tale that regreasing needs to occur immediately. Other noises such as growling or chattering may indicate wear on the elements or race and can be further diagnosed with more in-depth analysis.
Tactile Inspections
While being in close proximity of moving equipment does present some safety concerns, your sense of touch can be extremely sensitive to different common failure modes and symptoms of failures. Being safe is paramount when performing these types of inspections and you should always adhere to company policies regarding equipment and wear the proper personal protective equipment. Some of the many conditions you can monitor using touch are:
- Heat – a common symptom of machine failure is the generation of excess heat. While some machines may normally operate at high temperature levels, those that don’t can be monitored for abnormal heat. Using the back of your hand, you can lightly touch a surface to gauge how hot or cold it is. Remember, some machines may be incredibly hot so it is best to quickly touch something and if you are uncertain how hot something may be, use a non-contact thermometer to collect your temperature information instead.
- Contaminants – if done correctly you can capture purged grease or sludge from a system in a plastic bag. You would then roll the bag between your fingers trying to determine if you feel any solid contaminants and try to isolate them. To increase the power of this simple experiment you can use latex gloves and swirl the lubricant between your fingers. Your fingertips are incredibly sensitive to any grit or debris that may exist in the lubricant. Using a magnet in concert with this inspection can help determine is the solid is ferrous debris or not.
- Lubricant – while wearing gloves, you can inspect both greases and oils to crudely determine if they are still fit for service or not. When feeling greases, you would want to ensure that the mixture is smooth and doesn’t crack or bleed excessively when moving it through your fingers. Oils should be slick and not overly tacky. Comparing in service lubricants to new lubricants will provide useful insights to how the lubricant may have changed during service.
- Vibration – most people equate vibration analysis with collecting data and then analyzing the waveform back in the office. You can also inspect for abnormal vibration in the field using your hand or screwdriver. By placing your hand on the house of a machine you will feel the operational vibration of the equipment, as you move your hand from the inboard side of the machine to the outboard side, try to feel for any change in this vibration. By using something like a screwdriver and placing the tip on the machine, this vibration is transmitted to the handle which may make it more sensitive to determining if there is an issue.
Olfactory Inspections
Don’t overlook your sense of smell during your inspection rounds. This is a powerful tool, especially when it comes to diagnosing issues with lubricants. Many different compounds can be generated and exist within lubricants, all with their unique odor that, with time, can be identified. Perhaps one of the most common expressions heard when dealing with failed equipment is, “something smells burned.” This is an inspection type that does require some caution and it is always best to gently waft the smell towards your nose as opposed to bringing in a big breath. This is also an inspection that is best done from oil in a sample bottle as opposed to being in the field because of added vapors or fumes that may be present that could impact the sensitivity of your nose.
- Contaminants – some volatile contaminants are very easily detected by sniffing the oil sample. Things like fuels (diesel and gasoline), solvents and light hydrocarbons are easily found during this type of inspection. The smell test can be further confirmed by looking at viscosity or flashpoint which would both indicate the contamination by a drop in their values.
- Microbials – in equipment that is commonly contaminated with water and/or food materials, it is possible for the lubricant to promote the growth of bacteria or microbes. Left unchecked these contaminants can turn the lubricant incredibly acidic and begin to clog passageways restricting oil flow. During a smell test, you can identify these contaminants by a very noticeable rotting smell or road-kill smell.
- Oxidation – this is the primary failure mechanism for base oils and as such, there are many ways to inspect for it. Using your sense of smell you will be able to identify a distinct burned smell that is somewhat pungent. To confirm that oxidation is the issue, perform a quick visual inspection. If the oil sample is dark and has a pungent odor, oxidation is the most likely issue.
- Thermal – similar to oxidation this process will involve a darkening of the oil. However, during a thermal failure there will be no distinguishable smell. In some thermal failures, the volatile components of the lubricant have all be evaporated so what is left will be devoid of an odor. If you have a dark oil sample and no odor, check for contaminants or a thermal failure as the cause.
Modifications
As discussed, many pieces of equipment come with the proper accessories to be properly or even easily inspected while they are in services. Thankfully there are many devices that can be retrofitted to most equipment to make these inspections a reality. While some may require more modification than others, there are many relatively simple modifications that can greatly enhance your inspection program.
- Sightglasses with marks – anything used to determine the proper oil level should be marked with the normal running (“hot”) oil level as well as the off (“cold”) oil level. Simply putting a pencil or ink mark on the glass is not good enough and may cause confusion.
- Breathers with vacuum/pressure gauges – breathers that don’t have a change indicator built in should be equipped with an external vacuum or pressure gauge. This will indicate if the breather is plugged and not breathing correctly. Even desiccant breathers should be outfitted with one as they can become clogged before the desiccant is saturated and a color change occurs.
- Expanded metal – replacing sheet metal guards with expanded metal will allow for the visual inspections to occur without introducing a safety issue. For added ease, paint the expanded metal black to allow your eyes and camera lenses to see past the guards to the equipment more easily.
- Leak absorbent materials – by placing oil absorbent matts or pads under oil-filled equipment, it will provide for a quick visual reference point if there are any leaks coming from the housing. Sometimes small leaks can blend in with the adjacent concrete. The absorbent material often provides better contrast to highlight even minute drips.
- Gauges (orientation, go-no-go) – gauge faces should indicate normal levels or even be highlighted green for normal operation and red for abnormal operation. Any filter systems should be outfitted with differential pressure gauges or at a minimum a “go-no-go” pop-up style indicator. Some may wish to turn the orientation of the gauge such that the needle will be at the 12 o’clock position during normal operation so a quick glance can identify any needles that are not perfectly vertical.
By taking a step back from your current practices and designing a new inspection program utilizing some of these recommendations, you can expect to have a better insight into how your equipment is operating. While some of these may be easy to implement, most will require some additional training for maintenance, reliability, operations, or whomever is actually performing the inspections. Remember, each set of eyeballs that goes onto the plant floor is an inspector and as such, they should know what they are looking for!
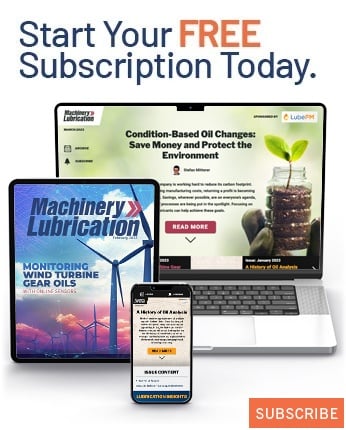