Many incorrect assumptions exist with regard to the greasing of bearings. Heightened awareness about the importance of proper greasing procedures could be the simplest vehicle for creating a positive impact on your company’s bottom line. To maximize its effectiveness, consistent maintenance methods should be implemented as described below.

Figure 1. The listening device is integrated with a standard grease gun.
Clearly, it is critical to provide lubrication technicians with sufficient information about lubricants and proper lubrication. Likewise, a product must be specified that employs the appropriate base oil, additive package and thickener, and considers the challenges like heat and contamination that the environment introduces to achieve effective lubrication.
How can lubrication deficiencies be detected? Lubrication charts and calculated intervals provide only estimates because they assume every bearing of the same size, running for an equal amount of time will use the same amount of grease. Precision lubrication demands more. Where possible, measurement and feedback from the machine is needed to drive maintenance actions, including greasing bearings.
Testing has revealed that all bearings are not created equal. Each one requires individual attention, with regard to lubrication, due to varying conditions of use. Depending on its placement, a bearing will be subject to different levels of stress, such as varying weight loads, different levels of contamination, bearing condition when installed and temperature, to name a few.
Therefore, every bearing needs to be analyzed separately to determine the amount of grease required. To date, determining when a bearing needed grease and if, in fact, the grease reached it when applied, has been mostly guesswork correlated with the temperature rise of the bearing. The listening device offers improved ways to determine if the bearing needs grease, and how much is required.
The technology used at Algoma Steel combines a sensitive listening device tuned to the 20Hz to 20kHz range with a conventional grease gun (Figure 1). By affixing the grease gun to a Zerk or other grease fitting, the technician can “listen” to the bearing. If the bearing quiets upon applying a shot of grease, it needs lubrication. If it does not, the bearing is adequately lubricated. If the bearing does not quiet upon applying grease, or quiets and then quickly becomes noisy again, the bearing may be damaged and require further analysis (see flow model in Figure 2).

Figure 2. Flow model for employing a listening device to guide bearing lubrication.
The Algoma Experience
As the Algoma Steel plant began to improve its greasing program, a startling discovery was found with the vibration analysis equipment. The acceleration envelope reading for early bearing detection, taken on the vibration monitoring data collector, displayed the increase in bearing noise level and thus signaled the need for grease.
Personnel could then see in detail what the listening device was hearing. So then, why did the plant still require the listening device? The original vision saw every area of the plant using the listening device in both mechanical and electrical maintenance. That vision still holds true, but the condition-monitoring (CM) group got involved by identifying lubrication issues and reporting them to each area of the plant. It is the responsibility of the maintenance technicians to carry out the greasing.
The CM group provides training by working with technicians on specific problems in their area as well as offering seminars. Once the technicians have a solid grasp of the basic concepts, they are on their own to grease those bearings reported with high noise levels, as well as other problem bearings they find on equipment not regularly monitored. Occasional follow-up is important to keep the program on track and allow for the exchange of new ideas.
Cultural Change
Since adopting this technology, a new view of machines has emerged. The CM group used to lump together all machine issues such as balance, alignment, coupling and bearings as one issue. Now bearings are viewed as a separate entity. For example, at the start-up of a new or existing machine, that machine can be said to run smoothly from the standpoint of balance, alignment and coupling issues, but may not be smooth due to noise levels in a bearing.
The next step is to determine the solution to the separate bearing issue, which many times is as simple as a few shots of grease. This was a big step toward preventing “infant mortality” at start-up and providing a smooth operation.
Now that it is possible to measure the noise level in a bearing, a new approach to preventive maintenance (PM) can emerge. Along the lines of the old adage “If it ain’t broke, don’t fix it,” consider the saying “If it’s running smoothly, don’t disturb it.” Most companies clean and repack split pillow block bearings on a six-month basis. Inspect bearings that are determined to be running smoothly to check for the correct amount and condition of the grease.
If that is good, then replace the cap and run it. A few shots of grease can be added using the listening device after the machine is running. Repacking the bearing can introduce contaminants into the rolling elements that will shorten bearing life. High heat resulting from repacking can also increase the potential for failure.
Success Stories at Algoma Steel
Following are some case studies which illustrate the value of improved greasing techniques.
Case Study 1 - 3000 hp Induced Draft Fan
Through vibration monitoring, the nondrive end bearing of the motor was found to have an elevated noise floor. Dryness in the bearing was suspected so the listening device was used to grease the bearing. As an experiment, envelope acceleration readings were taken before and during the greasing process.
The technician, using the grease gun, was amazed at what he heard. The bearing noise dropped dramatically after adding a small amount of grease. This is demonstrated in Figure 3 through the arrangement of progressive signatures in a waterfall display.

Figure 3.
Before greasing, there was a high noise level at 10 gs (0 shots of grease). After only 8 shots of grease, the noise level dropped dramatically to 1.5 gs (8 shots). After a few minutes, the noise increased slightly to 2.5 gs (8 shots). Only four more shots of grease were added and the noise was reduced and remained low (12 shots).
The noise level in this bearing rose again every three to four weeks. The technician could grease it with four to six shots of grease and know when it was quiet again. This bearing could have failed due to a lack of grease which would have resulted in the shutdown of primary steel production at a cost of $1 million every eight hours. This motor was eventually removed on a scheduled shutdown for repairs.
It is a fact that bearings can fail at very low levels of vibration, as the only initial sign of failure is internal noise. Detecting and lowering the noise level of bearings is therefore a crucial proactive step to preventing failures.
The bearing on the other end of this motor continued to run smoothly and did not require attention. Under the old PM method of greasing, both bearings would receive 20 shots of grease every six months. In this case, one bearing would have been underlubricated and the other bearing would have been overlubricated.
This motor issue then triggered the question of consistency in greasing. Due to a resistance to a change in culture, one supervisor thought the mill should return to a consistent method of greasing on a PM schedule every six months. It was then explained that the new system of greasing on an as-needed basis rather than by a schedule creates true consistency and longer bearing life, and he could not disagree.
Case Study 2 - Greasing of Pillow Block Bearings on an Overhung Fan
The progression of two different bearings on the same fan was studied over an 18-month period. The fan-side bearing was a 2-row spherical with a grease groove in the center while the drive-side bearing was a 2-row ball bearing with no center grease groove. Both bearings began with the same low noise levels as seen in Figures 4 and 5.
![]() |
Figure 4. Fan-side Bearing - Beginning Vibration
|
![]() |
Figure 5. Drive-side Bearing - Beginning Vibration
|
It was possible to grease the 2-row spherical (fan-side) bearing through the center but not the 2-row ball (drive-side) bearing. This meant that the new grease for the ball bearing had to be injected into the cavity of the pillow block. As the technician monitored the bearings using the listening device and greased as required, the noise levels in the ball bearing did not subside while the noise in the spherical bearing was controllable.
Over time, there were indications of looseness in the ball bearing, as a lack of direct lubrication resulted in dryness causing it to spin in the fit of the pillow block. Figures 6 and 7 compare readings on the two bearings after 18 months.
![]() |
Figure 6. Fan-side Bearing - 18 Months Later
|
![]() |
Figure 7. Drive-side Bearing - 18 Months Later
|
The only way the ball bearing could be greased properly was to repack it on a scheduled shutdown. Historically, failures such as this have occurred without any indication of the root cause. This is just one example of the importance grease path has on successful lubrication.
Case Study 3 - Greasing of Conveyors
The CM group cannot monitor all of the conveyor bearings in the plant, so it is the responsibility of the technician to grease the conveyors on a preventive basis. Before the existence of the listening device, the technician had to carry a packsack full of extra grease for the many head pulleys and guide rollers.
Now that he can listen to each bearing, and grease only those that require it, he carries only one extra tube of grease to cover the entire conveyor system. Using the listening device to detect failed bearings on the conveyor system has averted breakdowns.
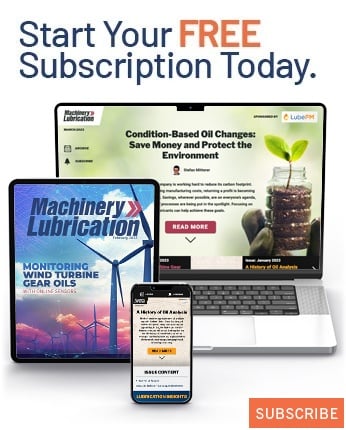