It is desirable to assemble any component or system with clean parts in a controlled manufacturing environment. However, this may not always be possible. It is sometimes necessary for the entire hydraulic system to undergo a cleanup process after final assembly to reach the desired roll-off cleanliness level.
This article provides a theoretical calculation of appropriate flushing requirements. Adherence to established roll-off cleanliness levels will provide the OEM with a better product and fewer warranty claims.
Experts estimate that 75 percent of hydraulic component and system failures are caused by contamination. Contamination causes premature wear and lost efficiency which can result in catastrophic failure. Typically, sources of contamination can be characterized as:
Built-In
Inadvertent contamination left in the system or a component during initial assembly or a system rebuild. Examples include weld splatter and cleaning rag fibers.
Generated
Contaminants internally generated during system operation, or caused by wear, corrosion, agitation, oxidation or fluid degradation.
Ingested
Externally introduced contamination that enters a system from various openings such as breathers, worn cylinder wipers, improperly sealed access covers, etc.
This article discusses built-in contamination, specifically particulate contaminants, and how to clean up the system following final assembly. Typically, particulate contaminants include weld splatter, dust, fibers, paint chips and other undesirable and potentially abrasive particles. Many of these particles are below the human visual threshold of 40 microns. Although they cannot be seen, they can be damaging to a system.
Click here to see Table 1. Current and Pending Standards.
Roll-off Cleanliness
The main purpose of roll-off cleanliness is to minimize damage to the various system components in their infancy. To underscore the importance of establishing roll-off cleanliness standards, the International Organization for Standardization (ISO) is developing new standards outlining the cleaning of components and systems. One draft standard, ISO/WD 16431, describes “roll-off cleanliness of an assembled hydraulic system upon release from the production area.” This title may change as the document is finalized, but it is obvious that the target is to provide the cleanest possible equipment to the customer.
Figure 1. Hydraulic System Lines, Fittings
and Components That Come in Contact with Fluid
Cleaning Methods
There are many ways to clean a system, and it is up to the manufacturing group of a company to decide which method(s) to use. The ultimate goal is to reach the desired cleanliness level at the most reasonable cost and minimum time interval. Some methods of achieving this are:
-
Let the system run through its normal operating cycle and allow the system filter(s) to clean the fluid. The system will operate at low pressure during the cleaning/flushing process. The main advantage of this method is simplicity. However, one disadvantage is that the system filter(s) might not have sufficient dirt-holding capacity to last through one cleaning. Several element changes may be necessary to clean a dirty system. This method may also damage system components if the initial contamination level is too high.
-
Use a filter cart, sometimes referred to as filter buggy or kidney loop (following the idea of kidney dialysis). This mobile, self-contained unit filters the fluid off-line using its own pump, motor and filter. It is designed to operate at a low pressure, usually less than 100 psi. The best way to use this device is to attach its suction and return hoses to the reservoir with fluid fittings and let it run while the system is running at a low pressure. Oil returning to the reservoir from the return line will now be filtered through the filter cart. This off-line process supplements system filter(s) and decreases cleanup time. This method may also damage system components.
-
Design an off-line filter that can be attached to the system at system pressure. It can be connected to the system in such a way that it becomes the power supply. The equipment can be cycled using hydraulic power from the off-line system. The main system does not need to be run except to remove oil from the lines that are not in circulation. The cart flow is not required to be as large as the system flow. The idea is to cycle the system for flushing purposes but not necessarily as fast as normal operating speed. This method minimizes damages to system components.
Figure 2. Off-line Filtration System
It is not economically feasible to remove all contaminants from a system. Most systems operate trouble-free with a small amount of contamination present. The amount of contamination that can be tolerated in a system depends upon the sensitivity of the most critical component. System reliability continues to improve, however, as ideal conditions are reached. Diminishing returns on increasing effort is the limiting consideration. This threshold for the contamination level is established by the component manufacturer and ultimately by the system builder.
The size and type of filter used are important in making calculations for cleaning a system. The analysis presented here makes use of the following assumptions:
-
Contaminants are uniformly distributed in the fluid.
-
During roll-off cleaning, no additional contaminants enter the system and no contamination is ingressed.
-
The filter exhibits uniform efficiency throughout its working life.
-
The filter does not go into bypass. If it does, the element is replaced. In order to avoid filter element change during the roll-off cleanup, the filter must be adequately sized. It has been observed that contamination may inadvertently be added to the system during element changes.
Real applications will vary from this idealization to some degree, but the variation is not expected to significantly affect the results.
Figure 3. Off-line Filter and Power Source
to Cycle the System
The classic filtration equation that applies to roll-off cleanliness is:
Simplifying the filtration equation using the assumptions above:
Where:
No = initial particle count @ x micron per ml
Nd = downstream particle count @ x micron per ml
V = system volume in gallons
Q = flow rate through filter in gpm
b = Beta ratio
R = rate of ingression
t = time in minutes
These equations can be further simplified by assuming no ingression. By substituting R = 0:
Solving this equation for 5 m and 15 m particle sizes and using Beta ratios at these sizes, the downstream count in a system can be obtained. This can be related to the ISO 4406 contamination code. The same iteration can be used for 4 mm(c), 6 mm(c) and 14 mm(c) size particles to obtain the ISO Code per the ISO 4406-19991 standard. It is important to use the proper Beta ratios, which correspond to old or new particle size references. ISO 4572 (defunct) and 168892 provide multipass testing standards.
Calculations can be complex and time consuming. Some programs will return theoretical particle counts at 4 mm(c), 6 mm(c) and 14 mm(c) sizes and the ISO 4406-1999 contamination codes after certain key parameters are entered. Run the system and take periodic samples during roll-off. When specified cleanliness levels are reached, the equipment may then be certified for shipment.
This subject becomes complicated when additional dirt is introduced to the system during cleanup. The advanced mathematical models used for further analysis are beyond the scope of this article. Such models have been developed by other sources and may be used to solve complex systems.
Proper roll-off cleanliness procedures protect equipment in its infancy and provide for fewer warranty claims. The end-customer is provided with a high-quality system with clean components that meet his initial use needs. Roll-off cleaning however, is only the starting point for trouble-free system operation. The final responsibility in controlling contamination lies with the user. Users must maintain proper filtration and practice responsible contamination control in the system to keep the hydraulic fluid clean.
Note: Author recommends consulting reference nos. 4 and 5 for information on how to clean various hydraulic systems.
References
- ISO 4406:99, Method for Coding the Level of Contamination by Solid Particles.
- ISO 16889, Multipass method for Evaluating Filtration Performance of a Filter Element. (This standard replaces ISO 4572 on the same subject.)
- Wait, Jay. “Contamination Control Needs.” NFPA Contamination/ Filtration: Issues and Perspective seminar, January 1998.
- BFPA/P9-1991, Guidelines for the Flushing of a Hydraulic System.
- Schroeder Industries roll-off cleanliness program.
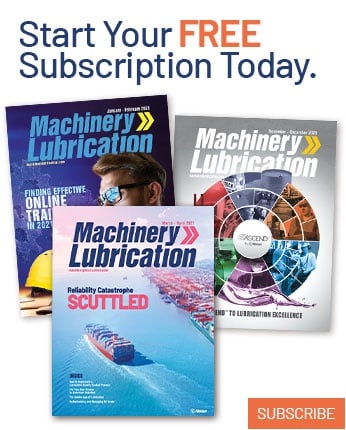