This past year Practicing Oil Analysis featured many end-user case studies documenting cost savings from oil analysis. Surprisingly, the majority of these studies describe the partnering of oil analysis with contamination control*. In this issue is yet another case study, by Weyerhaeuser, deploying this same strategic combination. It is unlikely that these are random events but rather a well-defined pattern. If so, exactly what is this lesson and what is its meaning to machine reliability?
To some it might seem a little like an old tune. After all, hasn't filtration been around nearly as long as lubrication? And, what's new that hasn't already been thoroughly explored and widely applied? For one, when it comes to cleanliness, knowing is definitely not doing. Many maintenance professionals know oil should be clean but the use of filtration and contamination control lacks rigor and discipline. Why?
Hidden behind steel plates, within the dark interior of our machine, the particles of dirt move about like a microscopic wrecking crew--invisible to the outside world. Even within a sample bottle they are too small to see. The dirt effectively is "out of sight" and therefore, usually also, "out of mind." People don't respond to what they don't see. As in most cases, embedded in the problem one finds the solution, or rather, opportunity. Simply stated, how do we turn the unseen into the seen?
For many world class organizations, when it comes to battling invisible particles, the preferred weapon is the invisible filter–a.k.a., the particle counter. Why is a particle counter called an invisible filter? Because it has the remarkable ability to change behavior. The old saying, "what gets measured gets done" says it well. Everything else left the same, the frequent use of a particle counter, with conspicuous reporting of results, often leads to an amazing downward trend in contamination.
Why? Because people are reacting to the feedback, by slowly altering past practices. When combined with education, little things and big things alike are done differently. For instance, greater care and attention is given to lubricant storage, cleanliness of oil cans and top-up containers is controlled, transfer systems are fitted with filters, tank hatches are sealed tightly, and breathers and filters are serviced regularly. In sum, the best filter is the unneeded filter, the invisible filter, the particle counter.
So, take the time to learn from the experience of others and develop a plan to emulate proven successes. To the astute, opportunity-seeking student of machine reliability, there are very few lessons so important.
Class dismissed.
*See Southern California Edison (Sept-Oct '98), Port of Tacoma (Nov-Dec '98), & Northampton Generating (May-Jun '99).
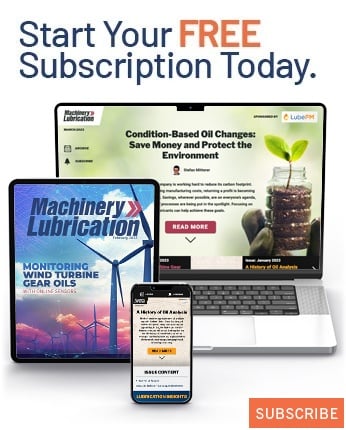