Survey Participants: Michael Bryson, San Onofre Nuclear Generating Stations, Southern California Edison; Brian Goff, Cargill; David Laguardia, Predictive Maintenance Analyst, Florida Power & Light Co.; and Gerry Trodd, Millar Western
Has oil analysis uncovered or helped you better understand lubricant selection problems that ultimately led to a change in lubricant specification? If so, please describe one or more of these instances. If not, please describe the manner in which you believe oil analysis should be more actively incorporated in your organization’s lubricant selection decisions.
Michael
Definitely! Our reactor coolant pumps and steam generator snubbers use GE-1154 (a polydimethyldiphenyl siloxane fluid). In the past, I have been told that this fluid was hard to come by and extremely expensive. I agree with the latter, this fluid is expensive. Our normal new fluid use per refueling outage was 35 to 55 gallons and San Onofre Nuclear Generating Station (SONGS) paid $2,000 and $2,500 per gallon to the local supplier. You do the math.
As it comes out, our vendor was “qualifying” the fluid to the snubber manufacturer’s specification, ensuring proper viscosity, acid number, water content and cleanliness. If the factory fluid cleanliness or water levels were out of spec, the vendor would filter and dehydrate the fluid until it met our site specifications.
I contacted GE directly to get more information on this product and I’m glad I did. The myth of this fluid wasn’t true at all. If purchased directly from GE, the fluid cost about $400 per gallon, the lead-time for a five-gallon pail was only three days, and for a 55-gallon barrel was just more than a month. The point here is that in the past, we did not feel comfortable assuming the liability of qualifying the fluid in-house, even though we were using the same lab as our local supplier for some of our lube oil samples. Our lack of understanding of lubricant selection and the required testing necessary to meet the manufacturer’s specification justified the amount paid to our local supplier. SONGS’ lubrication team has been empowered by this process and information. We now have the ability to buy direct and qualify the oil in-house. We also have a fresh approach to doing business in an old industry.
Brian
Yes. One case in particular comes to mind. Our facility had just rebuilt two Eagle Iron Works gearboxes for our double-screw washers. Oil analysis (ICP and DR tests) indicated we had high iron content after only about 250 hours of operation. Assuming this was normal run-in, we flushed the gearboxes and refilled them with the lubricant our supplier recommended, as we do with our other machinery. Again, after about 250 hours of operation, we had high iron content in the oil. Not knowing if it was from gear or bearing wear, we ordered analytical ferrography. The microscope images showed it was indeed gear wear, suggesting we had an insufficient lubricant in the unit. Further investigation revealed the original equipment manufacturer (OEM) recommendation called for an ISO VG 220 EP lubricant and our supplier had specified only an ISO VG 150 AW lubricant, as every other gearbox on our site requires. We changed the lubricant and no longer have the wear problem we saw initially. The money spent on analytical ferrography just to tell us if we had gear or bearing wear justified the expensive tests. It really pointed us in the right direction.
Gerry
Yes, as we have extended our oil drain intervals across all components within the plant, our oil analysis assists in us justifying or not justifying (in most cases) the additional cost of using synthetic fluids.
David
We are requiring our oil supplier to certify the new oil to ISO particle count cleanliness limits.
Has oil analysis helped you uncover or better understand opportunities to upgrade or implement contamination control measures on a machine that will ultimately increase machine life? If so, please describe one or more of these instances. If not, please describe how oil analysis might be used to support such decisions in your organization.
Michael
There is a myth that new oil is clean oil. We have proven this to be wrong. We randomly sample new shipments, measuring cleanliness levels, water and acid number. We also perform random spectro-chemical analysis. The random sampling results have forced us to make a commitment to oil cleanliness. We are in the process of establishing an onsite (within our protected area) oil lab, and have our maintenance department’s commitments to tighten oil cleanliness by filtering all new oil to an ISO 14/10 level. Implementing this process will not only establish a clear component baseline, but will extend oil changes and bearing degradation due to particle contamination. We have our design engineers working on installation specifications to sample valves (minimess style) and will begin eliminating open-to-atmosphere casing vents. This will take some time; however, when completed, every oil-lubricated component will have a better chance of meeting its full life expectancy.
Brian
Yes. On numerous occasions, our site has realized the benefits from better contamination control measures. We routinely filter very large mobile equipment hydraulic systems off-line during normal servicing. When we sampled hydraulic oils before and after filtering, we found a system will typically come in for service at a cleanliness level of 22/20 and when it leaves the shop, the cleanliness level is about 16/14. This has extended hydraulic component life considerably. With mobile equipment hydraulic systems becoming increasingly more electronic, oil cleanliness is critical for reliability. I have personally experienced hydraulic problems that have shut down an entire machine. The root cause ended up being dirty oil.
We have improved contamination control in our lubricant delivery system as well. Fine micron filtration has been installed, in some cases, at multiple transfer points along a lubricant delivery system. We’re now confident enough in our internal practices to begin really holding our lubricant supplier accountable for oil cleanliness levels.
Gerry
Yes, everything from oil sampling procedures to filtration beta ratios have been influenced by our oil analysis program. For example, a hydraulic system was continually running with high copper within spectography analysis when five-micron absolute filtration was used. By deploying three-micron absolute filtration, we gained control of this upward wear metal trend.
David
In some cases we are using a filter cart to clean-up the oil instead of performing a drain. This extends the life of the oil and increases component life. It also decreases the disposal fee. For nuclear power plants, this fee is very large.
Has oil analysis helped you uncover or better understand problems with a machine’s design and/or application? If so, please describe one or more of these instances. If not, please describe how oil analysis might be used to support such decisions in your organization.
Michael
Oil analysis should be used as a complement to vibration analysis, thermography and acoustics. In most cases, when a plant has a weak predictive maintenance technology, the results from that technology are often dismissed based on the creditability of the other technologies. This was the case in 2001, when our component cooling water pump inboard bearing (journal type, oil fed via a slinger ring) catastrophically failed. Ironically, the vibration reading was taken just the day before. Later review of oil analysis results indicated very high concentrations of lead, copper, tin, iron, chromium, aluminum; the presence of both zinc and phosphorous (ZDDP); and a wear particle concentration of 2,000. The increase in wear metals began in 1997, but vibration levels were acceptable and consequently the oil analysis was discarded. We recognized that the pump/motor was so overly designed that loosing an inboard bearing would have no effect on the overall vibration. We now recognize that oil analysis is more telling than the other technologies and we regard it as so for this style of bearing configuration.
Brian
Yes. I don’t believe there’s a facility in existence that was designed and built to meet all the capacity ever required of it. The fact is, we push our equipment to extremes whenever we think we can get away with it and still make the extra needed production. I have seen gearboxes turning 50 percent faster than designed (the oil analysis alarms on high wear metals every time). If we push our equipment beyond design limits, we shorten its life and increase the chances for metal-to-metal contact with higher operating temperatures and lower lubricant viscosities. As a result, we live with the problem and pay higher maintenance costs in the long-term. In some cases, maybe it’s justifiable. Most of the time it’s not.
Gerry
Yes, we are just going through a case where, due to the cage design, a group of our process pumps were subjected to severe cavitation and suffered irreversible damage. We are working with our OEM to implement a cage design change.
David
We are increasing our particle count cleanliness requirements for critical governors. In addition, we have set-up procedures that cover sampling techniques and we’ve started using particle count bottles. We also are filtering new oil onsite. The new oil is filtered until the cleanliness requirements are met.
Has oil analysis helped you uncover or better understand operations-related problems that affect equipment reliability, throughput and/or quality? If so, please describe one or more of these instances. If not, please describe how oil analysis might be used to support such decisions in your organization.
Michael
One of our operators was tasked with topping off the emergency diesel generator governor. The governor uses an ISO 68 grade hydraulic oil, which contains an antiwear package containing ZDDP. The operator reviewed the lubrication manual and verified that this was the proper fluid. He then proceeded to his oil “stash” locker to pick up a squeeze bottle of lubricating oil. Because no oil was found at the initial stash spot, he proceeded to another. There he found and used a squeeze bottle of GST 32 to top off the governor. On the walk back to the control room, it occurred to him that he might have used the wrong fluid.
The operator did not know the two oils were different and an operability assessment was needed to determine if the governor would perform as designed with the mixed oil. If we were topping off the crankcase and inadvertently added hydraulic oil, we could potentially destroy the engine because the zinc contained in the ZDDP would interact with the silver bearing wrist pins. This issue was brought to the operator’s attention and it has not happened again.
Brian
Yes. Many of our operations rely heavily on mobile equipment to produce an end product. This being the case, transmissions often contain a series of clutches within them. I can recall a couple of occasions where the presence of copper in conjunction with debris in the transmission strainer has prompted rebuilding part or all of a transmission. In every instance, we found excessive wear on the clutch discs due to an operator not releasing a parking brake or shifting improperly, depending on the machine’s drive train. It doesn’t take many of these rebuilds to realize we need more emphasis on operator training.
Gerry
Yes. Our housekeeping practices have been impacted by the findings brought to the forefront because of our oil analysis program.
David
Because of chronic problems with water intrusion in our non-safety related gear boxes, we are installing dessicating breathers.
Describe other ways in which oil analysis has or might be used to support decisions to minimize equipment life-cycle costs.
Michael
A common problem is overgreasing bearings, and in some cases, undergreasing. Recently, we reevaluated all rotating equipment, primarily motor bearings and fan bearings, and determined the optimum greasing interval and a maximum grease amount, as described in the EPRI (formerly Electric Power Research Institute) Electric Motor Predictive and Preventive Maintenance Guide (NP-7502). In general, the study pointed to bearing overgreasing. Initial estimates indicate an overall plant savings of approximately 1.5 to 2 million dollars over a five-year period, based on restructuring preventive maintenance activities. This should allow our maintenance division to continue its focus on oil cleanliness, water control, breather upgrades and sample valve installations. This evaluation is coupled with the use of acoustic bearing measurements to confirm the effectiveness of our lubrication activities. In addition, whenever a bearing is removed from a component, it is delivered to the reliability engineering group for investigation. We believe this examination reveals the effectiveness of predictive and preventive maintenance practices. This practice increased our awareness of the effectiveness of not just the lubricant’s properties and function, but also of bearing to shaft and housing fits, overloading and ball bearing integrity.
Brian
It’s difficult to convince anyone that proper oil analysis and lubrication will keep machinery from ever wearing out. However, oil analysis and a bit of common sense can increase the life of machine components tremendously. For example, we have numerous gear trains in operation. I’ve seen oil samples with large amounts of visible metal in the bottom of the bottle, yet the lab results come back and indicate there are no problems. Only after I called the lab back and changed the types of tests conducted for those sample points did the problems become evident to everyone.
Gerry
Monthly onsite particle counting is our first line of defense and is an integral part of our maintenance program, which we totally rely on to determine our portable filtration priorities.
David
We are installing minimess oil sampling valves. These valves will allow us to obtain oil samples without shutting down the equipment, reduce radiation dose and ensure we have representative and repeatable oil sample data. In addition, this will allow us to extend several costly oil change PMs.
Proper lubrication influences the life-cycle costs associated with owning and operating mechanical equipment. Proper lubrication can reduce maintenance costs, downtime costs and energy costs. Oil analysis serves as a scorecard for effective lubrication, driving lubrication decisions that influence overall life-cycle costs. Likewise, oil analysis provides information about a machine, which can be used to uncover design defects, misapplications and improper operation. To determine the role oil analysis actually plays in the field, we asked some end-users to share their views and tell us about oil analysis best practices at their facilities. Following, are the survey participants’ comments about oil analysis and its role in making smart life-cycle cost management decisions.
Michael Bryson
Michael is a lubrication engineer at Southern California Edison’s San Onofre Nuclear Generating Station, where he manages all lubrication related activities, including the oil analysis program. He is currently involved in implementing an acoustic monitoring program as part of a site-wide equipment reliability improvement plan. Michael is certified as a Level I Machine Lubricant Analyst. Michael has a Bachelor of Science degree in nuclear engineering and a Master of Science degree in mechanical engineering.
Brian Goff
Brian is currently a maintenance supervisor for Cargill. He is certified as a Level I Machine Lubricant Analyst and a Level I Vibration Analyst. Brian has a Bachelor of Science degree in mining engineering.
David LaGuardia
For the past year, David has been a predictive maintenance analyst in the newly developed predictive maintenance group at Florida Power and Light. Prior to this assignment, David spent 12 years in FP&L’s engineering department as part of the system performance group. He is certified as a Level I Machine Lubricant Analyst, and is also certified in thermography by ITC.
Gerry Trodd
For the past 25 years, Gerry has been involved in all aspects of equipment maintenance and reliability. He is an active member of the Society of Tribologists and Lubrication Engineers and is certified as a Level I Oil Monitoring Analyst. He is also a Certified Lubrication Specialist, as well as a member of the Canadian Machinery Vibration Association.
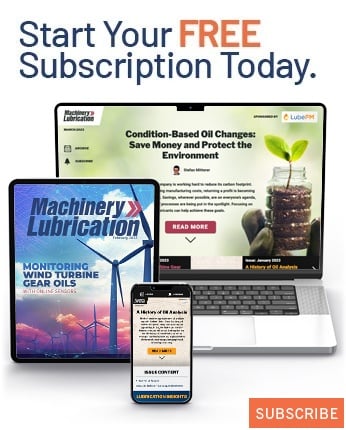