Every day in workshops, garages and factories people use high-pressure grease guns without realizing their potential for serious injury. As a result, a number of nasty hand injuries are reported to the New Zealand Department of Labour each year.
This article addresses the danger to grease gun operators and the few simple steps necessary to eliminate safety risk. It is intended not only for operators but also for workshop supervisors and employers who should ensure that all workers are well aware of the potential for injury.
The Hazard
Needle-point grease gun fittings are widely used, particularly in shop and automotive repair environments. The needle-sharp point is used with “needle” fittings on machinery to puncture and insert grease in polymer-sealed applications.
Grease is delivered at pressures between 1.7 MPa and 40 MPa (246.6 psi and 5801.5 psi) with pneumatic grease guns. The pressure is such that if the needle should slip off the grease point and puncture the hand or finger, grease can be injected and forced under the skin as far as the palm or even the wrist.
Lever- or hand-operated grease guns can pose a similar risk. A high-pressure output-type lever-operated gun can produce pressures as high as 103.4 MPa (15,000 psi). However, the chance of injury to fingers and hands with a hand-operated gun is reduced by the need to use two hands to operate the lever.
Such an injury causes a momentary stab of pain, with little inconvenience at the time. The injured finger swells a little, but otherwise is seemingly unaffected. However, over the following days the finger is likely to become swollen, stiff, and frequently gangrenous - leading to possible amputation. This is why grease gun injuries should receive immediate medical treatment, and why doctors regard them as serious.
Causes
Although high-pressure grease guns have been in use for many years, there continues to be regular serious hand injuries among users. In all such cases, operators have been using the gun without any protective cover (such as a safety sleeve or shroud) over the needle point. The needle has only to slip off the grease point to inflict an injury if the operator’s fingers are close.
During grease injection it is not necessary to place a hand in the danger zone, but it is a natural action when experiencing difficulty in locating the hose or needle fitting, or steadying the gun.
Most accidents occur while greasing flexible brake cables, where the operator usually places one hand behind the nipple to steady it or else holds the cable near the nipple connection and then inserts the needle point. If the needle slips (which is likely over many applications) then it will almost certainly enter the hand or finger.
Prevention
Grease guns are equipped with safety devices, but their effectiveness may be limited by the positioning of grease nipples on certain cars and trucks. Grease guns with needles should have a protective shroud or cover that prevents this type of accidental injury.
The New Zealand Department of Labour requires protective covers on all grease guns. Following this simple rule in every garage and workshop would eliminate serious injuries. However, shrouds are often removed to speed up a process, or are simply not installed properly.
Operators can argue that grease nipples are sometimes inaccessible and located where it is impossible to get to them without first removing the safety sleeve from the gun fitting. However, grease nipples are unlikely to be placed in a position where they cannot be reached at all. “Inaccessibility” probably refers to the operator following common practice - using his hand to feel the gun on to the grease point.
This action may be necessary for the following reasons:
- poor lighting
- the grease nipple is hidden under a layer of dirt and grime
- the wrong type of fitting used for the particular nipple.
Each of these causes can be remedied without using an uncovered needle tip. In the unlikely situation that an unprotected needle point is necessary, ensure that fingers, hands and body are clear of the needle once the trigger is pressed, then return the protective cover immediately.
In recent years, a number of improvements have helped reduce the risks from grease guns. These include the following:
- increased use of hydraulic grease nipples
- more convenient designs of protective covers for guns
- installing automated lubrication systems
In plants, there is often pressure to neglect safety points in the rush to service as many machines as possible. Unlike minor injuries such as cuts and grazes, the effects of grease injected under the skin can be long-term. Consider that you will be able to service more cars and trucks in the future with all your fingers. Whether you're rededicating yourself to follow safety measures, or you're choosing to install an automated lubrication system to do the work for you, safety is always the number one goal for your lubrication practices.
Safe Grease Gun Operation
-
Grease gun injuries are serious and require immediate medical attention.
-
Various safety devices are available for grease gun attachments, depending on the type of nipple encountered.
-
Hydraulic nipples, the most common today, should be used with a push-on injector for maximum safety.
-
The majority of accidents occur while greasing flexible brake cables, but it is possible to do the job just as well when safety devices are attached to the gun. An unprotected needle point should not be used in this operation.
-
Make sure safety sleeves and grease nipples are free of dirt before using guns.
-
Grease guns can be operated safely if the safety fittings are used and correct work methods are adopted.
-
Make sure there is good lighting underneath the vehicle.
-
Safety fittings reduce the danger and risk of serious injury. Don’t be the next to suffer from “grease gun finger.”
Editor’s Note
This article is reprinted with permission from the New Zealand Department of Labour.
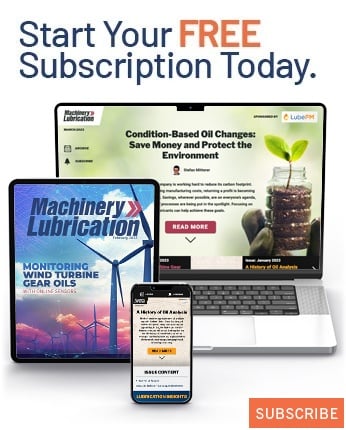