Getting Started
Getting started is the biggest challenge to developing lubrication expertise in a global company. This is always a daunting step, but one that can be overcome. If you’re reading this, you’ve taken the first step––you are interested in lubrication and its impact on your operations. The goal is to take your curiosity and knowledge and expand it to your entire global talent pool.
This interest can exist from the very basic situation of you being the person on the lubrication route, and you wonder what impact your actions have on the plant. You could be the head of the department and determine that a cultural change is necessary to improve your lubrication practices and plant performance. More than likely, you’re probably somewhere in between.
This desire to improve your lubrication knowledge and program stems from necessity, machinery performance, changing requirements, operational demands, warranty considerations, and other factors. The best way to start your lubrication knowledge journey is to begin with what you know. Are you involved in any of the following?
- Performing lubrication tasks
- Oil analysis
- Lubrication program management
- Lubrication specification for machinery
This list is not comprehensive, but it is a general guideline, and many other activities would benefit from increased lubrication knowledge. Once you have identified your strengths and weaknesses and how those match up with your company’s needs, you can begin to build the case for additional knowledge.
The Next Steps
Knowledge is good, and pursuing knowledge for its gain is noble. However, it would help if you also justified the related expenditures. This is where you begin to build the business case for expanding your knowledge via training, certification, and a reference library. All of these can become tools in your journey to improve your program and begin the process of developing talent in your company.
It will incumbent you to take what you’ve learned and spread that knowledge. Find a chance to utilize some training to improve a lubrication route, help develop a storage strategy for your oils and greases, take the analysis knowledge to trend oil sample data, or identify issues before they cause downtime. These tasks and activities will show the value of your increased knowledge and help build your business case. As you build your knowledge base and experience, you’ll become sought after to assist in plant issues. This gives you the opportunity to showcase the advantages of a well-trained lubrication team.
Expanding Talent
This is the point where you will be able to bring in other personnel from outside departments for additional training. There are several potential suppliers that can provide training, but don’t be afraid to approach your selected partner and request modifications to the training regimen. Your chosen company should be willing to work with you to tailor a training program for your needs. You may opt for a certification program for your people or take a couple of different classes and combine them to meet your specific requirements. At this point, with the goal being to expand your talent base and introduce a broader audience to lubrication fundamentals and the impact they can have on your availability and plant health, you might consider passing on a certification course unless you have an employee with the identified desire and aptitude.
Once you have chosen your instruction supplier, it is time to bring in your audience. I would recommend the “shotgun” approach. In addition to maintenance and lubrication technicians, there are a number of other personnel who could benefit from training like this. There are the operators of the equipment, the engineers who design the equipment, the supply and purchasing team who purchase the equipment and lubricants, and the quality team who monitors the incoming supplies and outgoing parts. All of these people interact with lubricants in one way or another on a daily basis, often without thinking about the fact they do.
The operators are the first line of defense against poor lubrication practices. They touch and watch the machinery daily. They will know when something doesn’t sound right, or an operation may be tending abnormal while still in the “acceptable” range. Putting your technicians through such training can help them understand what they see and hear daily, its implications, and how or who to contact to correct a minor problem before the failure becomes catastrophic.
Perhaps more obviously, the engineers who specify and design plant machinery, end products, and the processes to create products should be involved in lubrication training. Hopefully, most of the information in the class will be familiar to them, but there are always some new nuggets of knowledge that can be gleaned and applied to your respective situation. It could improve your lubrication formulations, application technology, filtration and storage, or other factors that could improve your plant’s performance.
These next two might not be as apparent participants as previous choices for attending your training, but remember you’re attempting to build lubrication excellence and talent throughout your organization. The supply and purchasing teams are responsible for ensuring that the materials meet the specifications required for your organization. This means they need to know the basics of the different oil and grease types, the best storage and handling practices, and minimum specification compliance.
The quality department would likewise benefit from training for the reasons listed for the supply/purchasing department and would additionally be the optimal group for validating that the incoming supplies are as ordered and meet any imposed cleanliness requirements. These personnel and technicians validate that the materials meet supply requirements and may be able to identify plant issues based on the materials presented in the lubrication training.
Follow Up Activities
Once you have assembled your diverse team and had your initial training, it is time to take the following steps. First and foremost, continue to encourage your people to utilize the training they just went through. You should identify motivated personnel to further their learning and direct them to various certification paths. Additionally, you should capture the increased knowledge base and expand it to the rest of your facilities. This can be initiated via a knowledge exchange, such as a working group meeting shared task force, or individual encouragement resulting from discussions between counterparts at different facilities.
As you continue to expand your knowledge base and network, you will discover that you are improving your reputation in the company, expanding your influence, and increasing the performance of your facilities. Talent development is a continuous improvement exercise; there’s always something new to learn or share. The more you train and the more you teach, the more people will look to you as the expert and knowledge source. This should be the beginning of a cultural change in your corporate environment. Lubrication expertise should translate into more ownership of production in your facility, increase awareness of maintenance practices, and a general positive shift towards a culture of excellence.
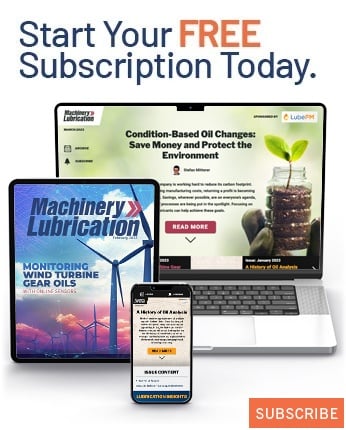