Oil analysis is becoming an integral part of most companies’ lubrication program. However, the success of any oil analysis program, and its ability to provide vital supportive information to the maintenance team is criticality dependent on how oil analysis data is managed.
If the data is managed efficiently and effectively, it can provide valuable information to everyone involved in maintenance practices and oil analysis, acting as a gauge or yardstick by which the success or failure of the lubrication program can be measured.
The most effective programs combine information from all the maintenance team members, including original equipment manufacturers (OEM), lubricant suppliers, onsite and off-site laboratory personnel and other sources, creating an integrated, holistic approach to precision lubrication.
The biggest challenge this presents is the need to gather data from multiple sources and compile it into one centralized database. The next challenge is to create a user-friendly interface that allows anyone on the team to access the data they need anytime, anywhere, without having to mine through unnecessary data.
Making the Transition - Optimizing the Data Interface
Optimizing the data interface requires more than just compiling data in one location. It requires training and conditioning those empowered individuals to make lubrication related decision about how to use the available data most effectively.
Experience shows that to create any real value from raw data, the information from the desktop must be transferred to those trusted individuals in a timely fashion. The data must also be easy to comprehend, yet detailed enough to provide the team members with the roadmap they need to help them make informed decisions.
Because data is constantly flowing in from various sources, and out to various team members who may be hundreds or even thousands of miles apart, the information needs to be gathered and displayed across a seamless platform.
While five to 10 years ago this may have presented an insurmountable challenge, in today’s world of broadband T1 or DSL lines, the Internet is the obvious tool that can be used to let everyone involved view the data in real time, from a single centralized database.
The primary goal for a successful system is to use the Internet to leverage the data. However, just because information is on a Web browser doesn’t mean it’s of any real value unless everyone is using a Web-based platform that has the data-mining capabilities needed to use the information to its fullest extent. The individuals must also understand how to best use the data.
For example, consider a system in which a single on-site oil sample shows signs of distress. A single bad sample reading may not be sufficient evidence to warrant a shutdown, so a second sample is taken.
Even though the second sample confirms the findings of the first, a production manager, whose mandate is to maximize equipment uptime at all costs, may be reluctant to order a shutdown, since this will impact production quotas. While this may help keep production running - in the short term - the decision, which is based on a dearth of data and a calculated risk, may ultimately lead to a more serious failure, resulting in excessive and unnecessary downtime.
Now consider the same example, but with the addition of six months worth of trended oil analysis data combined from an on-site lab, an off-site lab and the lubricant supplier’s lab. This data is presented in graphical format and includes vibration analysis readings that support and confirm the oil analysis results and thermographic data - complete with color images - that illustrate localized hot-spots within the components. With this overwhelming data, even the most cynical production manager may be more inclined to make the correct decision and shut down the system for repair.
The users in this example are empowered to make informed decisions regardless of the data source. This data source independence eliminates the constraints of a typical single-source laboratory information management system (LIMS).
A management system like the one described here provides a customer-centric database to monitor and manage information. It gives users freedom to select from multiple labs and facilitate testing across multiple platforms. It gives users the ability to use a comprehensive program of on-site screening and deeper laboratory diagnostic evaluation without risk of losing key data.
Empowering Users
Users should have the ability to select options such as having their laboratory evaluate the samples or establish a global set of rules for automatic evaluation of test data based on lubricant, OEM recommendations, customer goals or other input guidelines. Again, any of these options should be available within one database environment that includes proper access for each team member.
Through the example, it is clear to see how the Internet and its collaboration capabilities make sense. Using hierarchical permissions, program sponsors can view all the data in their branded oil analysis offering to see how their equipment, lubricant, filter, etc. are performing. This can be viewed in cross sections of the database by industry, geography, or any other variable or sets of variables.
Distributors/dealers, as a trusted solution provider, should have the ability to access their customers’ data; perhaps only scanning some customer information or digging deep into their most valued customers’ operating environments.
Customers’ viewing capabilities should be enhanced as well. Local operations can focus on their equipment, while the corporate office can view maintenance and performance activities across a broader spectrum, such as all their plants or fleets. It is important to remember, however, that this online platform is not all about reading data. The parties should constantly be updating and improving the database by contributing information online.
Value-added Benefits
This online platform should include other items that will increase the data’s value. For example, items such as online kit ordering, new asset registration, powerful management reports, label printing, regression analysis and automatic e-mail alerts, can provide additional value. Let’s take a closer look at each of these.
Online Ordering
Ordering of kits and supplies may be done as a self-help process. As more users become familiar with and begin to prefer online ordering from large commercial sites, it’s only right that they should be empowered with online ordering. This frees up time for the commercial lab or fulfillment center and can include custom pricing matrices for larger volume orders or for preferred customers who require special pricing parameters. This method allows for electronic notification to the supplier, once again providing seamless integration of supplies in the value proposition. This order can include an e-commerce payment gateway or a simple purchase order feature that allows the customer to pay the dealer, who in turn, may have his account charged directly by the laboratory.
Registering New Assets
The ability to add equipment, components or other sampling points, including storage tanks for fuels and liquids to assure baseline performance, is another important feature of successful equipment and lubricant management system. These assets can be registered online by the end user or by the distributor, through a value-added service to the customer.
They can even be added dynamically by any lab source exporting the data as new samples arrive. The benefit here is the ability of approved team players to collaborate once again, and draw from this information in order to complete their piece of the value chain.
For example, because the records are housed in one master database accessible 24 hours a day, seven days a week over the Web, the customer can integrate the data with the company’s fixed asset records or maintenance systems, while the equipment dealer monitors the warranty testing requirements. All the while, the lab simultaneously compares equipment degradation to a normalized population of the same machinery.
Management Reports
Managers today are under constant time restraints and pressures to do more with less. While most lubrication program managers want to maximize performance through the use of effective information technologies, it can become a quagmire to extract all of this information into summarized, easy-to-understand reports.
An online interface can not only have this functionality, but the process can also be automated to save even more time. Managers can once again have the ability to turn on and set the parameters of management reports.
For example, a manager could log into the site and select the desired reports and tell the system when these reports are to appear in someone’s inbox and in what format. The manager can also decide on the frequency - weekly, monthly, quarterly or whenever desired - for each of these reports without further intervention.
These management reports can include information such as sample summaries (Figures 1 and 2), overall unit conditions, samples due, location profiles and equipment profiles. A distribution list for the reports can even be set up.
Figure 1
Figure 2
Label Printing
Users appreciate the niceties of some of the most basic things in lubrication program management. This includes an easy-to-read label for the sample bottle without someone’s hard-to-read handwriting, which often results in sampling errors. These errors must be manually corrected by the lab, which must then resend a report. Sometimes these little errors turn into huge headaches for everyone involved.
Label printing greatly reduces these errors and delivers a professional value addition to the person on the other end of the sampling equation. This label can include a bar code for technology partners who wish to employ just one more time-saving step to ensure correct results.
Regression Analysis
This “go forward by looking backward” approach to fluid analysis is just now taking managers by storm. The model system can include this functionality to allow the “power user” to take a look at the historical data and compare it side-by-side to other units or components in his or her hierarchy.
This data can be displayed in an easy-to-read online chart where the parameters are first entered in an online form and filtered to focus on just a few key components. This form can include the option to bring in an independent variable, such as “time on component” or “time on oil” (Figure 3).
Figure 3
Of course, the user would then want to select the elements being scrutinized for this linear regression graph. After selecting the units or components and makes/models, etc. to be included, the user clicks the submit button and the work begins on the server to process and interpret the data.
Once the process is complete, in only moments, the user is presented with the regression analysis comparison chart, which includes sloping, colored lines that represent the data and trends.
The manager can then use this information to make meaningful decisions based on data rather than a guess; decisions such as which vendors and manufacturers are providing the best value. The manager can also determine which operating conditions within the entire fleet or plant are most effective.
Auto E-mail Alerts
E-mail is the communication tool of choice for many managers and collaborative team members. It’s a quick and efficient means of getting the message out and around to the team. It should not be ignored. When using e-mail, it is important to consider the auto-driven notifications of action items as significant process performance improvements.
These improvements range from the customer establishing desired e-mail notification of severe oil samples to corporate maintenance managers. E-mail can also be used to notify lubricant distributors when a new piece of equipment has been added to the customer records. The possibilities are endless. The value of monitoring the database 24 hours a day, seven days a week to improve job performance is really what it is all about.
Editor’s Note
The benefits of an online lubrication management tool can be enormously powerful to lubrication managers, laboratories, end users, lubricant dealers, plant maintenance personnel and many others. For more information on companies that provide lubrication management software, and the features they offer, see the Oil Analysis Software Buyers’ Guide on page 34 of the November - December issue of Practicing Oil Analysis.
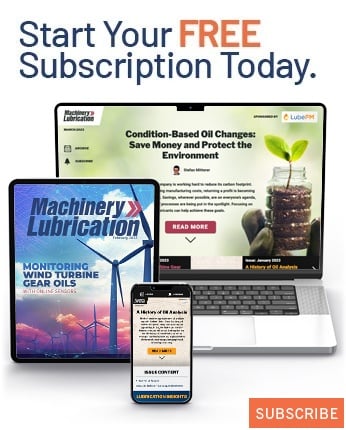