What’s life like inside a rolling element bearing? Let’s say you are a dollop of grease and you’ve just been pushed by a grease gun into the dark recesses of a bearing cavity. You are now in a combat zone. What are your orders? Maybe you are on a suicide mission. Your bearing has been screaming for reinforcements and you are it - the new recruit - all gooey and slimy.
Inside you see grease casualties all around. There’s the stench of oil oxidation on one side and the stiff lifeless remains of a soap-based thickener on the other. In an instant, the floor and walls begin to vibrate, then you hear a low rumbling sound. You are pushed deeper into the bearing cavity and suddenly you can’t move - the heat and the pressure are excruciating. Then more pressure … crack … silence.
What just happened? How could regreasing a bearing have contributed to sudden-death failure? Doesn’t fresh grease prolong bearing life and restore reliability? Not so fast. The problem here is new grease entering an old, infrequently lubricated (and overly lubricated) bearing. As the new grease enters, it must make room, and in doing so, it pushes around the crusty remnants of grease past.
Before the new grease arrived, the soap-based thickener from several earlier relubes is often packed against the inlet port and along the grease cavity walls - adjacent to the bearing’s moving elements. The oil from the thickener bled out slowly over time. Some of this oil entered the bearing race providing needed time-released lubrication.
The principal contributors to a hard, crusty build-up in the bearing cavity are heat, long relube intervals, overlubrication (too much grease) and old bearings. There are other factors too, including grease quality, vibration, centrifugal forces, contamination, pressure and the relube procedure. In addition to the thickener, hard particles are sometimes deposited along with the thickener forming a wall next to the bearing. These include wear particles, dirt, rust and manufacturing debris.
For the new grease to reach the bearing core, it must break through this rock-like formation, creating a channel. Hydrostatic forces from a grease gun can reach levels exceeding 15,000 psi (103,421 kPa) - more than enough pressure to send chunks of solids careening into the bearing track.
Imagine the new grease acting like an ice-breaker on a frozen river, mobilizing large blocks of ice as it moves. Sometimes fresh grease never reaches the bearing because of the wall-like barricade. Instead, it detours out the shaft seal or the vent port. The bearing is eventually starved to death.
Large bearings (especially large electric motor bearings) are often lubricated through supply pipes (line extensions) from a grease fitting. Hardened thickener, rust and other solids can build up in these pipes over time. On relubrication, the new grease functions like a plunger, driving the solids into the bearing cavity below.
So what lessons can be learned from this? Remember the maintenance paradox: “It’s broken because we didn’t work on it. It’s broken because we did work on it.” The key here is knowing when to work on it, how to work on it, what tools/hardware to use, and what lubricant to use. In the case of the bearing, there are a number of questions to be answered before regreasing begins, including:
-
Whether to use grease at all, vs. oil (mist, bath lubricated, circulating, etc.).
-
If grease is to be used, what type or formulation (complex soap, nonsoap, high- temperature, solid additives, synthetic, high viscosity, NLGI number, etc.).
-
How to gauge the quantity of grease needed. Whether to use feedback tools such as vibration, heat guns, acoustics, etc.
-
How frequently to regrease the bearing based on factors such as operating conditions, environment, bearing type and orientation, temperature, grease type, vibration, etc. Use our bearing grease frequency and volume calculator.
-
Whether to use a grease gun, single-point automatic lubricator, centralized lubrication, etc.
-
What procedure to use when regreasing the bearing if lubricated manually.
-
Whether to switch to sealed or shielded bearings.
-
Whether to periodically analyze used grease samples.
World-class lubrication requires precision and skill. While there may be more than one right way to do something, there are many more wrong ways. The answers to these questions are rarely intuitive. Training and education develops top-drawer lubrication skills and can give the dollop of grease and the rolling element bearing a long, happy life.
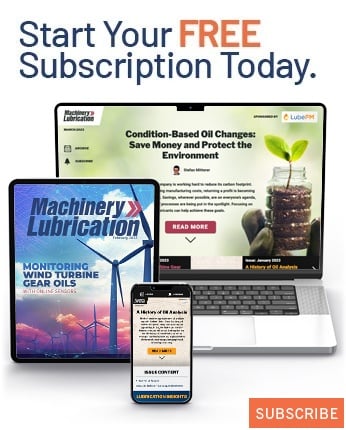