The use of gas engines for power generation has become more widespread in recent years. With estimates that up to 30 percent of worldwide electricity demand will be generated from gas by 2020, this trend seems set to continue.
Their growing use has accelerated both commercial and technical demands on gas engine lubricants, and encouraged engine operators to increasingly demand performance expectations beyond the minimum required by the manufacturers.
These factors have pushed traditional gas engine oil (GEO) formulations to their limit, and have highlighted the performance limitations of traditional additive solutions. A careful rebalancing of advanced additive and base oil systems is set to deliver improved performance over traditional lubricants to meet the challenges of current and future gas engine design.
To ensure trouble-free operation of their engines, engine manufacturers essentially dictated minimum performance requirements for GEOs which consequently evolved with engine design.
However, today’s engine operators are also demanding performance features beyond those minimum levels to enable them to achieve cost-effective engine operation. While the engine manufacturers’ requirements are mandatory, those of the engine operators allow lubricant manufacturers to differentiate their products on performance grounds.
Engine Manufacturers’ Requirements
One of the key requirements of engine manufacturers who need trouble-free operation is the avoidance of knocking, which can lead to the destruction of the cylinder unit. In large gas engines, the formation of deposits in the combustion bowl is known to initiate knocking. Lubricants designed with low sulfated ash content reduce this risk.
Gas engine manufacturers specify the range of sulfated ash content that is suitable for each engine they market. This ranges from less than 0.1 percent ash by weight - known as ashless, less than 0.5 percent ash by weight described as low ash, through less than 1 percent ash by weight referred to medium ash, up to greater than 1 percent ash by weight regarded as high ash.
To endorse any lubricant, engine manufacturers require proof of performance in field trials from 4,000 to 10,000 hours in an approved installation. The main areas of interest for the field performance of a GEO include:
Resistance to Oxidation and Nitration
GEOs need to have the ability to neutralize the acidic by-products of oxidation and nitration. The effects are visible on lubricant parameters such as viscosity, rise in acid number, drop in base number, infrared analysis of used oil, and on engine parameters such as engine cleanliness and bearing corrosion.
Control of Deposits
The oil must deliver virtually no deposit to the combustion bowl given the engine sensitivity to knocking. Control of Corrosion This is particularly important when the gas is especially corrosive, and where engines are fitted with bearing technology known for its sensitivity to corrosion.
These data give formulators the information they need to design new GEOs and are provided as guidelines to engine operators to indicate drain intervals. Assurance of these guidelines requires continuous condition monitoring by used oil analysis.
Recent Trends
In an effort to increase engine load and mechanical efficiency, there have been several recent developments in gas engine technology. One key improvement is the increased use of electronics, possibly combined with dual fuel operation, for better combustion control. This involves ignition by diesel fuel rather than a spark plug.
So far, these advanced designs have not led to alteration in the manufacturers’ requirements for the lubricant. However, future changes will need to support control of emissions, exhaust gas deposits and knocking.
Engine Operators’ Requirements
Engine operators expect more from a lubricant than simply trouble-free engine operation. Because engine components have become more durable, it is often the end of the lubricant’s lifetime that requires maintenance work to be performed during scheduled outages. A lubricant’s ability to reach very long drain intervals (4,000 hours) in any engine model is highly desirable.
Because traditional additives and conventional base oil systems have reached their limit in that respect, particularly in the smaller engines, the focus has turned to using higher performance base oils. However, traditional additive chemistries often struggle, particularly in terms of deposit control, in these higher performance base oils.
Like any engine oil, a GEO is a combination of additives and base oil. Given the importance of oxidation/nitration control on the performance assessment of a GEO, appropriate selection of both is essential.
Faster Formulation
Proof of the GEO’s performance is evaluated in the field by engine manufacturers and operators alike. However, with some field tests requiring two years, formulators are recognizing that to keep pace with engineering design developments, there is a need for more flexible and faster methods for evaluation that will give a good indication of field performance.
At a recent American Society of Mechanical Engineers (ASME) conference, Infineum presented data outlining a test sequence for the formulation of high-performance GEOs that used well-established commercial GEO formulations as reference. The relevance of the laboratory test sequence was confirmed by subsequent field performance.
Table 1. Detergents Differ in Performance Features
Depending on Surfactant Composition.
Salicylates for Longer Oil Life
The main constituent of the additive system into the formulation is the detergent system, because it delivers all the required performance characteristics. Detergents differ in their performance features depending on their surfactant composition.
Traditional phenate detergent chemistry is excellent when exposed to high temperatures for short periods. But it is limited in terms of oil life performance at the moderate temperatures and longer operation of gas engines.
This can be overcome by adding more antioxidant, but given their relatively short lifetime, this cannot be an effective solution in a system that is expected to run for 4,000 hours. Salicylate detergent chemistry controls oxidation for a longer time in gas engines and has demonstrated longer oil life in the field.
Base Oil System
GEO formulations have mainly been blended using conventional (Group I) mineral base oils. There has not been significant penetration of the market by synthetic (Group IV) base oils because of their high cost to the operator. Formulators have attempted to eliminate brightstocks from the lubricant because brightstocks have a limited resistance to oxidation.
Recently, formulators have been able to choose alternative base oils such as Group II (hydroprocessed mineral oil) and Group III hydrocracked (high viscosity index base oil). These offer great advantages to the GEO formulator thanks to their improved resistance to nitration and oxidation, compared to the Group I base oils.
However, performance evaluation of these base oils shows that they must be associated with a carefully balanced additive system if they are to deliver any benefit. The optimum formulation consists of combining the most effective salicylate detergent technology and a Group II base oil.
Editor’ s Note
This article is reprinted from Infineum Insight magazine with kind permission from Infineum International Limited (www.infineum.com).
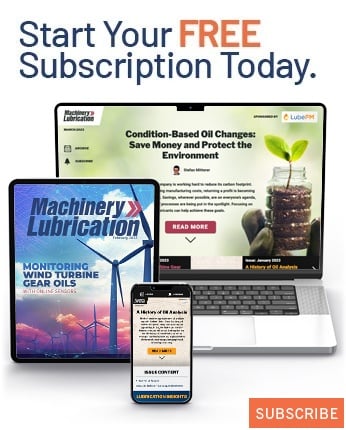