
What should you do when a lubricant doesn’t get a clean bill of health?
More specifically, what must be done with the machine that contained a degraded or contaminated lubricant after the oil drain?
If the answer is yes, there are a few other questions that follow, such as:
-
What was the root cause that led to a need to flush? Who is to blame?
-
How urgent is the need to flush? Can’t we wait?
-
What are the risks of not flushing? What is the worst that can happen?
-
Are there negative side effects to performing a flush? What dark cloud is hidden beneath the silver lining?
-
What is the best way to perform the flush to reduce cost, risks and business interruption?
To Flush or Not to Flush
While the broader, procedural subject of flushing goes well beyond the word-count limit of this column, let’s take a closer look at the fundamental question of when performing a flush is justified. When we understand the conditions that trigger the need for a flush, we are better equipped to answer the remaining questions on the list above.
From my experience, the items listed below are the most common reasons a flush is justified.

Often, the need to flush is first observed during an inspection or the appearance of sludge in a sight glass, on a used filter, or on the bottom of a sump. This can be confirmed by oil analysis and further inspection.
Remediation involves both the removal of the sludge, varnishing or debris (flushing) plus the removal of the root cause before the system is returned to service with normal life expectancy. The flow chart below can help in deciding whether to perform a flush.

Risky Business
What are the risks associated with a flush? These vary considerably and depend on the flushing procedure, the machine, and the lubricating oil. If the flush procedure involves introducing foreign chemistry (solvents, detergents, etc.) into the oil or machine, this could impair the performance of the lubricant and attack seals and machine surfaces.
Lab testing in advance can hedge the risks. In certain cases, flushing can also lead to leakage when deposits are removed around aged seals and gaskets. In addition, problems can also come from the disturbance and resuspension of settled, low-lying contaminants that are not fully carried out of the system during the flush. In general, there are risks any time a machine is invaded by human agency.
A quality flushing service will design a custom plan for each machine, ensuring that the task is performed properly and that sensitive components are unharmed.
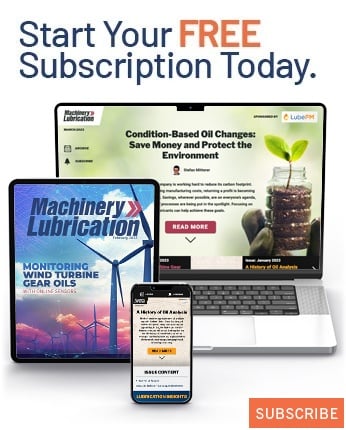