This is the fourth and final part in my series on flushing. We’ve already talked about when to flush, the consequences of not flushing, the differences between flushing and oil reclamation, flushing tactics, flushing strategies and flushing sequence.
This article addresses the role of the voice within your oil and how to let it guide your flushing process. This voice, also known by practitioners as an oil analysis, can provide essential information relating to flush avoidance, when to flush, how to flush, and when your flush has been successfully executed. This guiding role of oil analysis will be discussed in three phases.
Phase 1 - Before the Flush
In relation to flushing, the most important time to perform an oil analysis is well in advance of a required flush. However, it doesn’t just tell you when an impending need is detected.
Instead, its real value is to proactively stabilize the internal-state conditions that avoid the need to perform the flush altogether. In fact, a well-structured oil analysis program should largely focus on proactive maintenance objectives, such as avoiding the future need for a flush. This is due to the fact that nearly all flushes are performed after the following scenarios:
- needed maintenance was not performed
- maintenance was wrongly performed (for example, an incompatible oil was introduced)
- the machine was invaded by a foreign contaminant (for example, glycol, soot, etc.)
A well-designed oil analysis program should enable these common problems to be detected before a flush is required. When successful, only an oil change may be required.
Of course, the effectiveness in catching common flush precursors depends on oil samples being taken at the optimum frequency and the proper use of on-site or laboratory screening tests. In the event the condition was not detected on time, an oil analysis would still be able to provide both the alert and degree of severity (urgency) of the flush condition.
Table 1 lists example tests that could be used to reveal precursor, impending, or severe conditions:
Phase 2 - During the Flush
Many flush strategies involve the use of a program of flush tactics until the original offending contaminant has been scoured from the machine as well as both the flush and rinse fluids. The flush and rinse fluids often contain fluid chemistry that must be thoroughly removed before the lubricant is replaced and the machine is returned to service.
Oil analyses can be used as often as needed to assess what remains in the circulating fluids. In such cases, the analyses can aid in guiding the process by defining the type and duration of each step in the sequence. Perhaps certain flush steps (tactics) will need to be repeated based on the results of the analysis.
This enables flushing decisions to be made or modified in real-time in response to oil analysis data. In addition to laboratory testing of oil samples, various inspections of the machines’ internal surfaces, including gearing, bearings, and tanks, can help confirm the successful execution of the flush program.
Phase 3 - After the Flush
There are unique and often serious problems that can be an unpleasant side effect of machine flushing. However, evidence of these may not occur immediately. Flushing disturbs a machine in many ways that can’t always be predicted or easily observed.
As such, for a period after a flush, oil analyses should be performed regularly on critical machinery to ensure that healthy conditions have been restored. Early detection of a problem could be the difference between costly downtime and a nuisance condition that could have been easily corrected.
The following is a list of potential problems (side effects) associated with flushing where oil analysis might provide a timely alert:
- Demulsibility - remnants from flush fluids can interfere with this important property.
- Oxidation stability - disturbed sludge and machine deposits may adversely affect this property.
- Viscosity excursion - many flushing and rinse fluids are very low in viscosity compared to the lubricant. When these fluids mix with the lubricant, viscosity can be cut back by as much as 50 percent.
- Film strength and rust inhibitor problems - flush and rinse fluids may absorb into machine surface grain boundaries. These absorbed chemicals may interfere with the performance of important surface-active lubricant additives.
- Leakage and seal problems - when new chemistry is added to a machine and/or a violent flushing occurs, seal performance may be affected. This may also be due to changes in lubricant viscosity or interfacial intension from fluid mixing problems.
- Oil way and filter plugging - flushing and rinse fluids can resuspend sludge and insoluble contaminants which can cause flow blockage of glands, orifices, oil ways, and even filters.
In conclusion, the voice in your oil is an opportunity for those who perform or are considering performing a system flush. It would be rare for a machine to have a flush requirement without both the causes and effects appearing in the oil data well in advance, but only when samples are taken and the right tests are performed.
This is just one more reason why learning the language of oil analysis is a valuable, enabling skill in the field of machine reliability.
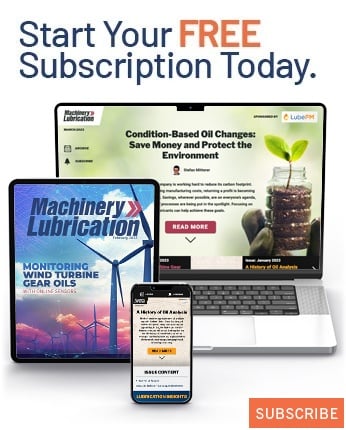