Seminole Electric Cooperative’s Generating Station in Palatka, Florida, began commercial operation in 1984 as the state’s first cooperative-owned generating plant. The station consists of two 650-megawatt coal-fueled generating units that burn 10,000 tons of coal and petroleum coke daily in a 24-hour, 7-day maximum capacity operation. Both of these units incorporate environmental protection systems that originally cost more than $233 million.
Problem
From approximately 1996 to 1998, Seminole Generating Station used a popular environmentally acceptable hydraulic fluid in its hydraulic applications wherever spills or leakage could result in damage to the environment. The product literature claims the product is a readily biodegradable, nontoxic, vegetable-based oil that meets the essential spill control specification outlined in Chapter 62-770 of the Florida Administrative Code.
Maintenance personnel noticed that the product performance fell far short of expectations, especially in the hydraulic systems that pull and position freight cars through the coal unloading rotary dumper. They observed the oil become corrupted due to the moist and dusty operating environment. This spoilage caused problems that necessitated frequent service, such as pump failures, filter plugging, valve sticking and strong odor.
According to Brian Thorp, predictive maintenance technician, each incidence of hydraulic fluid decay required the entire system to be shut down for drainage, flushing and refilling of fluid.
“Every four to six months, we had to conduct extensive maintenance and clean up of all our hydraulic systems and oil reservoirs,” Thorp said. “This cost us an inestimable amount in terms of labor, maintenance expenses, replacement oil costs and loss of efficiency.”
Figure 1. Brian Thorp, predictive maintenance
technician, inspects the hydraulic system that
operates the arm that drops down and
connects with the knuckle between the coal
cars. Once the arm is attached to the knuckle,
the cable system pulls and positions the
cars to dump coal.
Chevron Supplies Solution
Bill Sharp, the predictive maintenance supervisor at the time, consulted ChevronTexaco Products Company’s North America Lubricants business manager Sam Vallas, with whom he had a close association as a result of Seminole Generating Station’s long-standing use of Chevron lubricants.
Vallas suggested that Seminole experiment with Chevron Clarity® Hydraulic Oil AW, with its ashless additive system that provides oxidation stability, water separability, foam suppression and protection against wear, rust and corrosion. It is inherently biodegradable, minimizing long-term environmental concerns, and meets the Florida Administrative Code specification. Seminole agreed to test the Chevron oil in the hydraulic systems of the generating station’s coal-unloading rotary dumper.
Performance and Savings
Since implementing the new hydraulic oil, Seminole Generating Station has not experienced a single costly hydraulic system failure, according to the Seminole maintenance team. This performance convinced the team to employ the oil in additional applications, and it has since successfully eliminated copper leaching from ZDDP in oil coolers and motors. The oil has also successfully been used in other equipment, which has enabled oil change intervals to be extended up to five years and counting.
![]() |
Figure 2. Total view of the forced draft fan, whose fan bearing oil circulation system was experiencing a copper leaching problem from the coolers. |
“We’ve not had a single problem since we started using new hydraulic oil about six years ago,” Thorp said. “It’s a high-quality product that has worked consistently well in our equipment. We’ve been able to extend oil drain intervals from the one year initially recommended by our vendor to as long as five years. With some of our blowers using approximately 300 gallons per reservoir, this adds up to huge savings. This is especially significant given that the total cost of a gallon of oil is actually four to five times higher than its listed price - this figure incorporates the added charges involved in receiving, handling, storage and disposal.”
Relationship and Value
Over the years, Vallas built a valuable and productive relationship with the members of Seminole Generating Station’s maintenance team, based on his industry expertise and the performance and technology of ChevronTexaco lubricants.
Vallas often conducts lubrication training sessions at Seminole’s facility to educate the station’s personnel on the importance of lubricants to their operations.
“Our goal is to give our customers the tools and knowledge necessary for success,” Vallas said. “We take pride in serving as efficient resources for their product and information needs.”
![]() |
Figure 3. Submerged oil cooler in a vertical condensate pump motor. The bright color of the tubing metal shows copper leaching and ZDDP issues. |
Technical Editor’s Note:
Upon complete review of the criteria, one may find that a product that is inherently biodegradable will meet environmental constraints imposed on production environments.
There is a difference in lubricant stability between the inherently biodegradable and the readily biodegradable product types. American Standard for Testing and Materials (ASTM) and Organization for Economic Cooperation and Development (OECD), have developed a biodegradability test that is useful for differentiating between “ready” and “ultimate” biodegradability.
In the test, bacteria is introduced to a sample and the sample is maintained at fixed conditions for 28 days. Production of CO2 is measured to determine relative biodegradability. For a lubricant to achieve a rating of ready biodegradability, there must be greater than 60 percent degradation in 28 days.
Most vegetable oils tested have shown to biodegrade more than 70 percent within that period as compared to petroleum oils biodegrading at about 15 to 35 percent. For more information about environmentally acceptable lubricants, take a look at an article by Lou Honary, University of Northern Iowa ABIL Research Center. Biodegradable/Biobased Lubricants and Greases.
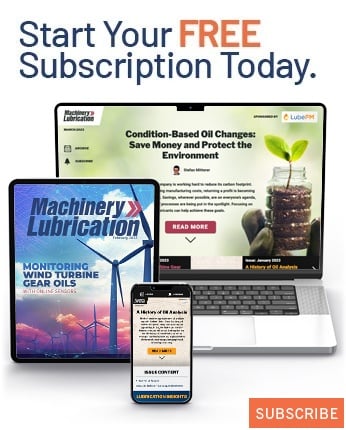