In June 2005, Shell Chemical’s Process Engineering Group set out to chemically clean two reboilers involved with the benzene, toluene and xylene chemical process. The reboilers were not transferring heat to the product and the heating oil was losing its capacity to transfer heat in other areas of the units.
Shell Chemical knew that changing the degraded heating oil would improve production and effectively transfer heat throughout the units. Mechanical cleaning of the reboilers was too time-consuming and therefore was not an option for the short shutdown.
The sludge factor of the old oil was expected to be a challenge. Shell felt it could remove most of the sludge in the initial drain and that the flushing process would remove most of the remaining sludge during filtration. A new furnace was put into one of the units in 1983, but no flushing occurred at that time. The 47,000-gallon heating oil system was last changed in January 2001. Thermia Oil C was selected for use.
Figure 1. Customized Flushing
Equipment per Specific Site
Shell planned to shutdown the units for 12 days, allowing the product to cool off, and for degassing, draining and refilling the system with new heating oil.
Given the size of the unit under consideration, all recognized that the project would require careful planning and scheduling to achieve a successful outcome. The goal was to complete chemical cleaning on two reboilers, as well as flush the entire system to be operational and on-spec before the deadline.
Lubrecon Systems Inc., the service branch of O’Rourke Petroleum, proposed to flush the remainder of the piping with the new product to remove the remaining solids from the interior of the system.
The proposal was based on flushing the new oil at temperatures ranging from 150ºF to 160ºF, cycling through different flow paths of the system in designated groups to achieve the velocities needed to remove the degraded oil deposits and remaining sludge. Filtration was to be conducted using 25- to 100-micron (pore size) media.
The system was to be shutdown from July 8 to 18, 2005, but the timeframe for the flush required that Lubrecon Systems service team complete the work in a three-day period.
Major Considerations
The heat transfer system was designed to operate at temperatures greater than 450ºF. There was some concern about worker safety when handling oil at these temperatures. Management was also concerned that allowing the oil to cool before draining would produce sludge and cause problems when draining the total volume.
Finally, planners recognized that all high-point vents would need to be purged with nitrogen while allowing the oil to drain from each bottom section of piping.
Figure 2. Filtration System
The furnace was shut down on July 8, and the pumps circulated the process to keep the fluid moving while it cooled to 150ºF. After the temperatures reached 150ºF, the draining process began. Temporary pipes were fixed to low points in the piping system to collect the old fluid.
Other low points that could not be piped to the storage tanks were opened and the remainder of the oil was gravity-drained into various containers. The old product was transferred from the totes to the storage tank utilizing AbCleans vacuum trucks.
Devising a Plan
The challenge was filtering and flushing a great deal of solids from the system – a process that would require constant changing of filters if the filtration units were not matched with the proper pumps. Interrupting the shutdown schedule was unacceptable, therefore the plan had to be precise from its inception.
Anticipating the likelihood of filter plugging, each temporary pump and filter unit was configured to allow fluid bypass and system cleaning without disturbing the balance of the project. Lubrecon Systems forecasted and planned for multiple filter changes.
A plan was devised to simultaneously operate two 2,000 GPM flushing systems. Each system would be equipped with a pump, system heater and two filter units per system. Each filtration unit had eight filters for a combined total of 32 filter elements.
Flushing of the Heat Medium System
The initial circulation stage was intended to remove the most solids from the system over a 12-hour period. The plan focused on the entire heat medium system with every flow path opened to reflect normal operating conditions. After removing the heating oil and refilling with new Thermia C, the system was turned over to Lubrecon System to begin the high-velocity flushing at 12:50 a.m. on July 13.
Each cleaning system pump was started with a combination of 100-micron and 50-micron filters in each of the filtration units. Elements were changed when the differential pressure reached 25 PSI. Within minutes of starting the flush, every element became plugged and the bypasses had to be opened.
Over the next 12 hours, filters were changed approximately every two hours. The procedure was followed for two and a half days through four stages where certain sections of piping were allowed to flush while other circuits were isolated from the flow path.
In each circulation stage, the circuits experienced greater flow at higher velocities than normal operating conditions. The filtration units would eventually plug after each section of the system was purged, which indicated the removal of solids from that particular part of the system. This process continued until the deadline.
Shell Chemical asked that Lubrecon Systems clean the system as much as possible before startup. Because the system had not previously been cleaned, there was no predefined cleanliness standard established to mark completion of the project. In response, the system was flushed and filtered for 66 hours. Lubrecon changed out approximately 244 filters, proof of a huge amount of solids removed from a very dirty system.
Productive Units
Chemical engineer Stefan Martula offered the following comments after completion of the project: “Prior to the outage, the aromatics units at Deer Park were experiencing overall production losses of about five percent due to degradation of heat medium oil, which was fouling the heat medium system.
These losses were expected to increase to 25 percent before the next turnaround if no action was taken. After shutting down for oil replacement and flushing, the units returned to maximum production capacity and are expected to maintain those rates until the next turnaround.”
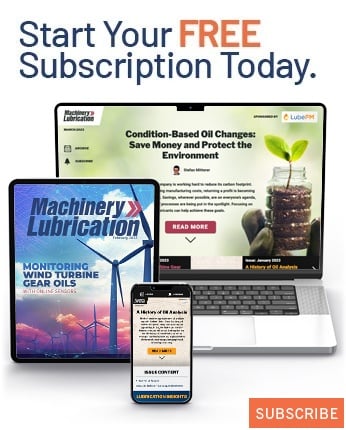