Several years ago, a large 2,300-volt motor failed on custom-made equipment after only 18 months of operation. The motor came from a reputable manufacturer, and the company had experienced no similar problems with other motors from the same manufacturer.
The mode of failure was total destruction of one motor bearing, allowing the rotor to hit the stator, followed by massive electrical failure. The condition of the bearings and housings after the failure suggested either a lack of lubrication or improper lubrication.
The manufacturer of this motor requires 1.25 cubic inches of an approved polyurea-based lubricant to be added to each bearing cavity on a regular greasing interval.
Initial questions to the end-user regarding history of lubrication were met with replies that their global manufacturing operations enforce rigid lubrication procedures for all their equipment, with all greasing intervals documented.
In fact, this end-user was quick to offer printed documentation showing the exact times when the motor bearings had been lubricated, as well as written procedures that were to be followed by all plant personnel. In addition, there was one deviation report that had been filed approximately one month prior to the failure.
Faxed copies of these documents were informative. Proper greasing intervals were recorded as promised; however, the grease used was an in-house lubricant that turned out to be a lithium-thickened product.
Polyurea grease, as supplied in motors from the motor manufacturer, should not be mixed with lithium-based lubricants. When combined, these two incompatible thickeners allow the base oil to bleed from the thickener, leaving a mixture with a lower consistency (softer) than either lubricant would be independently.
The deviation report from a month prior stated that oil was seen leaking from the pipe-plugs at the grease relief ports. The corrective action was to apply Teflon tape to the threads of the pipe plugs!
Another error confirmed in the documentation involved the amount of grease added at each interval. The end-user’s written procedure required that the maintenance mechanic pump new grease into the bearing housing until old grease appears at the relief port.
The document further instructed to continue pumping more grease into the housing until fresh, clean grease is seen at the relief port! Needless to say, the amount of grease applied was much more than the required 1.25 cubic inches!
Experience also shows that filling a bearing housing 100 percent full of grease typically causes the bearing operating temperature to become 25°C higher than normal.
The point to remember when relubricating electric motor bearings is to always follow the motor manufacturer’s specific instructions and do not use any lubricants other than those approved by the manufacturer.
There are many greases on the market that are recommended as “excellent for use in high-speed rolling element bearings.” However, even the latest and greatest formulation may become worthless if combined with another fantastic, but incompatible, lubricant already residing in the bearing housings.
Technical Editor’s Note:
This is good advice where the motor manufacturer offers a systematic recommendation for lubricant volume, frequency and method. Good lubrication procedures are often not uniform across motor manufacturers.
Also, there is a well-reported concern over incompatibilities between polyurea-thickened and lithium/lithium complex-thickened grease lubricants. Incompatibilities are productspecific. Some modern versions of polyurea thickeners are reported by their manufacturers to be compatible with lithium/lithium complex products. It is important to verify compatibility before considering mixing greases.
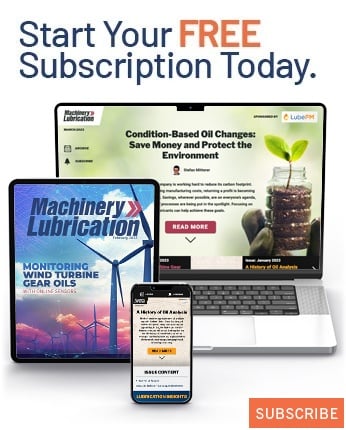