When evaluating an automatic lubricator on an outdoor fan location, we found that the grease had hardened in the tubing. As a solution, we added a pipe tee with an additional zerk and an isolation valve under the lubricator to ensure that fresh grease gets to the bearing during PMs. We close the valve under the auto lubricator, pump in the grease, then open the valve to let the lubricator work as normal. The photo shows the valve in the closed position for adding grease with a manual grease gun. In normal operation, the valve handle covers the zerk.
Tom Bruhn
Eli Lilly
Greasing Seals
After observing dozens of seal failures over the years, I have discovered a problem that can occur during the seal installation or with the seal life itself. Many lip-style seals utilize a small coiled spring located in a groove on the inner side of the seal. This is obviously designed to maintain a certain amount of lip pressure to the shaft surface. However, upon examining several failures, I discovered that this spring can jump out of its groove in the seal assembly. This is due to the "shocking" that the seal experiences while being driven into place with a hammer/seal driver. The individual blows can cause the spring to pop out of the seal assembly, releasing the pressure on the seal lip. Another problem I've observed is the rubber material that comprises the lip area tends to dry out over time. This results in micro-cracks in the sealing surface and is another source for seal failure. My solution is to fill the back side of the seal with grease compatible with the rubber used for the seal. This "grease pack" accomplishes two things for the seal. First, the grease tends to work as a dampening agent and prevents the spring from jumping out of position. The second benefit is that the grease, if chosen properly, works as a preservative for the seal rubber. The oil releasing from the grease keeps the rubber soft and pliable - even after years of service. For those of you concerned about the grease coming out of the seal and getting into the various oils/fluids - I have been doing this "seal fill" for more than 14 years and have yet to see the grease come out of a seal.
Greg Neuenfeldt
Dow Corning Corporation
Improved Grease Fitting Location Solves Bearing Starvation Problem
Applying the calculated value of grease may not be effective when relubricating antifriction bearings in pillow block housings. After a recent failure investigation, it was determined that a screw conveyor pillow block bearing failed due to a lack of lubrication. The investigation reported that the grease fitting was installed on the top cap close to one edge. In this location, it would place the grease into the cavity adjacent to the bearing. Because the adjacent cavity was not filled with grease, the bearing did not see lubricant even though the bearing housing had been lubricated each month with a small amount of grease.
Upon further investigation, we found the installation of grease fitting locations to be nonstandardized throughout the mill. We consulted the bearing manufacturer's literature, and by using our ultrasonic tool in the field on a number of greased pillow block applications, we determined that the amount of grease required when adding to the cavity adjacent to the bearing versus directly into the bearing was a minimum of three times the calculated amount. Therefore, the position of the grease fitting on the pillow block housing should be in the center of the top cap in most cases. It is paramount to identify the fitting location when considering the regreasing requirements of a bearing.
Ben Staats
Cariboo Pulp and Paper
Selecting an Industrial Sealant
With so many products to choose from, making sure you select the proper sealant is especially important. Selecting the wrong industrial sealant, or applying the correct sealant in the wrong manner, can have serious consequences. Keep the eventual application of your sealant in mind, and ensure it has the following characteristics:
Stability over a wide temperature range - Once fully cured, high-quality sealants perform across a wide range of temperatures. The best sealants can withstand temperatures ranging from -85° to 599°F (-65° to 315°C). Select a sealant that functions reliably at temperatures outside the performance range to accommodate unexpected temperature changes.
Weather resistance and chemical stability - UV rays, radiation and weather can cause low-quality sealants to crack, crumble and become brittle, compromising the seal over time. Look for sealants with good resistance to these and other erosive factors. Some organic sealants react to atmospheric pollutants or chemicals much like iron reacts with water to produce rust. Use a sealant that does not readily degrade after prolonged contact with common elements and industrial chemicals.
Good bond strength - Good industrial assembly sealants provide durable adhesion to a wide variety of industrial materials, including glass, ceramics, wood masonry, metals and plastics. A variety of factors contribute to the bond strength of individual sealants, including chemical composition, cure type and substrate penetration.
Electrical properties - If electrical properties are a concern, be aware that some organic sealants are less suited to applications where they may be exposed to electricity. In such instances, a high-quality silicone sealant may be a better option.
Low flammability - In fire conditions, some sealants are more fire-resistant than others. Silicone sealants, in particular, are especially reluctant to burn and many comply with UL flammability standards.
Most importantly, make sure you select a sealant that can perform at the highest temperature you require but also offers a secure and flexible hold at lower temperatures. When in doubt, consult a qualified expert.
Ross NoelDow Corning
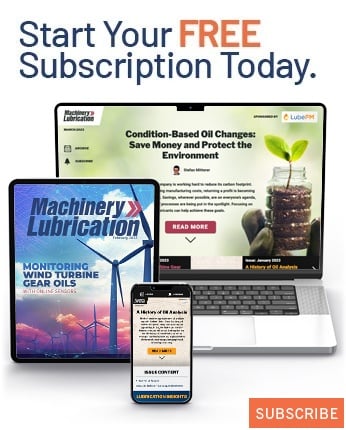