When maintaining lubricated assets in an industrial plant, the common belief is that following the Original Equipment Manufacturer's (OEM) lubricant recommendation is the safest and most effective route. This advice stems from the trust in OEMs' knowledge and their presumed alignment with the best interests of their machines. However, is this universally applicable, especially in large-scale operations?
To thoroughly explore this question, this article delves into two critical areas. First, we'll examine the underlying objectives and considerations behind an OEM's lubricant recommendation. Are these suggestions purely technical, or do other factors come into play? Second, we focus on your plant's unique environment and operating conditions. Here, we'll discuss the primary objectives when selecting lubricants for a diverse range of machinery across a typical plant environment and everyday maintenance challenges.
This discussion aims to underscore the much-needed attention to best practice lubricant selection while challenging the notion that OEM recommendations are always the optimal choice for every situation.
OEM Lubricant Recommendations
A lubricant recommendation from the OEM is expected with just about any lubricated machine, such as compressors, gearboxes, turbines, hydraulic systems, and electric motors. Often, the lubricant may be listed on the nameplate or a sticker near the oil fill point or grease fitting, especially if it's already prepacked or prefilled with a specific lubricant.
At a minimum, the OEM-recommended lubricant is usually found in a lubrication section in the OEM manual. Most will relate to this as we often find this in the manual located in our vehicle's glove box. These recommendations are selected based on many considerations, including four key areas:

- Machine Design and Operating Requirements: OEMs select a lubricant to match the machine design needs and test their machines under specific conditions with certain performance criteria. The focus is typically on reliability and longevity within the target design life. The operating conditions will consider factors like operating temperature ranges, load conditions, speed, and environmental factors like dust, moisture, or chemical exposure. The recommended lubricant must be capable of performing effectively under these varying conditions. For example, it is common for multiple lubricant viscosities to be recommended based on different operating temperature ranges. Also, base oils and additives are selected to consider compatibility, such as with seal materials, metals, or potential interactions with process fluids to avoid corrosion, degradation, or other forms of damage.
- Industry Standards and Certifications: Lubricants must often meet certain industry standards or certifications. This is usually the case for equipment like compressors, turbines, or other machines where the OEMs recommend lubricants that establish standardized approvals for major capital investment or have a higher risk to the environment, health, or safety. Turbine oils, for example, have extensive lab testing and validations for the lubricant's performance in specific equipment categories, often included in the Product Data Sheets under "OEM Approvals."
- Warranty, Liability Concerns, and Other Commercial Factors: Recommended lubricants are often a stipulation for maintaining a warranty. This requirement stems from the OEM's confidence in specific lubricants chosen to minimize the risk of machine failure that could potentially result in warranty claims or legal liabilities. Furthermore, OEMs frequently sell these lubricants directly, sometimes under white-label branding. It is worth noting, however, that commercial agreements between OEMs and lubricant manufacturers may also influence such practices. While these agreements do not inherently imply that the recommended lubricants are of inferior quality, they can shape the OEM's lubricant recommendations. This factor is critical to consider as it may affect the selection of lubricants suggested by OEMs.
- Overall Ease of Maintenance and Cost-Efficiency: OEMs often consider the balance between the cost of the lubricant and the overall cost of operation and maintenance. The goal is to recommend a lubricant that provides cost-effective operation over the equipment's lifespan. This includes considerations like the frequency of lubricant changes and the availability of the lubricant in the market.
Selecting any one lubricant for any one machine can often be easy. For a smaller volume system, the lubricant is a minor cost. The answer in this case is often to "just use the OEM-recommended lubricant. It's easy. It's a safe choice." For a larger volume system that is critical to operations, the lubricant is a much more significant cost, and one bad choice here could cost the organization significantly in repair costs and downtime. Thus, it's often the same answer, "just use the OEM-recommended lubricant. It's easy. It's a safe choice."
This tactic may be adequate at first. However, several shortcomings require a more strategic approach, particularly when considering your plant's specific environment and operating conditions and the typical challenges of managing maintenance across hundreds of machines. In this case, the "safe choice" may have far-reaching implications that flip the script on lubricant selection.
Considerations in Plantwide Lubricant Selection
First, lubricants must be viewed not as consumables but as assets. In the simplest terms, an asset is something with economic value and the expectation that it will continue to provide benefits in the future.
We maintain our assets because they provide us value in return the longer they last. We optimize the selection of assets based on reliability and the potential return. When properly maintained and carefully selected, an adequately selected lubricant has the same potential as an asset.
Organizations that have focused on this as a proactive measure have realized significant short-term savings towards their maintenance budget and several times more in increased uptime of machines.
1. Lubricant Consolidation: Imagine a restaurant allowing every customer to customize their meal. While this approach caters perfectly to each individual's taste, it would require the restaurant to stock an enormous variety of ingredients and significantly complicate the cooking process. This could lead to inefficiencies, increased costs, longer wait times, and potential errors in order fulfillment.

In contrast, consider a restaurant with a well-thought-out menu. This menu may not cater to every specific customer preference, but it offers a balanced variety of dishes that satisfy the majority of patrons. By doing so, the restaurant operates more efficiently: the kitchen can manage stock better, prepare meals faster, and maintain higher quality and consistency, all while reducing costs and complexity.
This scenario parallels the situation in a large plant with numerous machines. If each machine uses an OEM-recommended lubricant, the variety (like the fully customizable menu) becomes unmanageable, leading to logistical challenges and increased costs. However, by selecting a consolidated list of lubricants (like a set menu), the plant can adequately meet most machinery's needs. This approach enhances overall operational efficiency, simplifies inventory management, and reduces costs, even if only some machines have their ideal, specific lubricant.
Typically, more favorable lubricant supplier agreements can be arranged, providing immediate cost savings. However, the most prominent savings may be from reduced machine failures often associated with undocumented root causes like cross-contamination.
2. Optimum Lubricant Selection: Like most other maintenance decisions on a machine, factors of criticality, safety, cost, and environmental impact will influence. This means that even across multiple identical machines, it may require different machine modifications, condition monitoring needs, lubrication practices, and lubricants selected, all based on what is optimal to meet reliability objectives. This is called the Optimum Reference State (ORS).

The OEM-recommended lubricant is typically a single lubricant (or specification) that considers their machines' most intended use case. However, any one machine may have very different operation environments.
For example, based on ORS factors such as criticality, one specific machine may be sufficient with a simple economically selected lubricant. In contrast, in another area of the plant, the same type of machine may require a premium lubricant with more diligent monitoring of lubricant condition changes over time. Both may be in the Optimum Reference State and the most cost-effective choice considering the Total Cost of Ownership (TCO) and impact on machine reliability.
Even strictly speaking about the machine's specific operating conditions, lubricants need meticulous selection. Operating temperature, workload, and operational frequency are fundamental factors that can significantly affect lubricant performance. These can be counteracted with adjustments in lubricant selection, such as with viscosity (such as with operating temperature and load) or additive or base oil robustness (such as for oxidative stability or seal compatibility).
3. Upgraded Lubricant Selection: Lubricant technology is constantly evolving. New formulations and additives are developed regularly, offering enhanced performance characteristics such as better temperature stability, improved wear protection, and extended lubricant life. In some cases, newer aftermarket lubricants may outperform the OEM-recommended products, especially in harsh or unusual operating conditions.
Many new products in the growing aftermarket lubricant industry offer comparable or superior quality to OEM-recommended lubricants. These products often undergo rigorous testing and certification processes, ensuring they meet or exceed industry standards. Additionally, some aftermarket lubricants are specifically designed to address issues commonly found in certain types of machinery, offering tailored solutions that OEM products may not provide.
Think Broad When Making Your Lubricant Selections
In this article, we've challenged the default reliance on OEM recommendations, encompassing many factors, including machine design, industry standards, warranty concerns, and cost-efficiency considerations. Meanwhile, with a plantwide perspective, lubricant selection is altered with broader operational objectives like daily efficiencies, TCO, and machine reliability. From the viewpoint of an asset rather than mere consumables, lubricants must require a much more careful selection.
So, what are your motives for selecting a machine's lubricant? For some in maintenance, the primary concern might be finding a readily available "approved lubricant." Period. While sharing this need, maintenance managers and reliability engineers are likely more attuned to how lubricant choices enhance equipment reliability. Then, there are operations supervisors, inventory clerks, and plant managers, each with unique considerations and their own perspective on how it impacts costs.
Wait, there's more!... to this decision-making process. There is often special consideration for environmental impact, necessitating environmentally acceptable lubricants (EALs) or industry-specific needs like food-grade lubricants in food and beverage facilities. Moreover, the common belief that using alternate lubricants automatically voids warranties is a myth provided these lubricants meet the required specifications. Companies like Noria that specialize in lubrication recommendations offer a wealth of expertise when tailoring to specific operational needs - an aspect sometimes overlooked in OEM recommendations.
TCO, the intricacies of maintenance culture, and the impact of lubricant selection on plantwide reliability make lubricant selection much more than just technical questions. This is a paradigm shift in how we perceive and embrace lubricants as vital assets that significantly impact the efficiency and longevity of machinery.
Operators and maintenance managers can make more informed decisions by integrating the lessons learned here. This enhanced decision-making process has the potential not only to improve equipment performance and lifespan but also to optimize operational costs and environmental footprint.
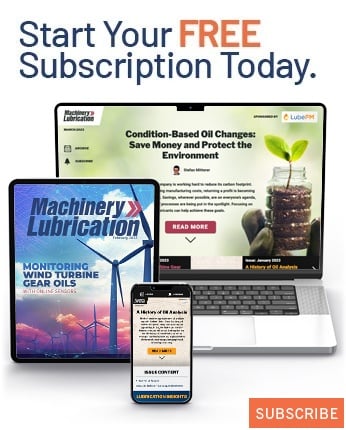