Open or semi-enclosed gear drives, also known as heavy-duty gear drives or girth gears, have been a common method of power transmission since the beginning of the Industrial Revolution.
Generally, open gear drives are the most economical type of gear drive alternative for use in applications where high load-carrying capacity and long service life under severe shock load conditions are required.
It is these characteristics in addition to flexibility in the machine’s design that have made open gear drives the most common type of drive used for ball mills and grinding mills, kilns, dryers, draglines and shovels. There are two types of open gear drives; Type 1 utilizes a rack whereas Type 2 utilizes a gear or series of gears.
Defining the Application
Type 1 Open Gear Drives
Type 1 open gear drives consist of an actuator and a rack system used to transmit power. This type of open gearing is primarily used on the cable hoist drums, swing motion drives, mechanical boom lifts, shuttle transfer units and in the hoist and drag drives of mining shovels, draglines and excavators.
These open gears can be bidirectional in motion, and in most applications the tooth geometry, surface finish, pitch line and intermittent loads cause them to operate in thin lubrication film or boundary lubrication condition. Type 1 gears are typically spur-type gears.
The primary functions of a lubricant used on a Type 1 open gear drive is to act as a friction-reducing interface between the meshing gear tooth surfaces and as a cushion against shock loads.
If the open gear lubricant is able to provide these characteristics and contaminants and wear debris do not exceed moderate levels, the open gear lubricant can significantly increase the life of the open gearing.
Type 2 Open Gear Drives
Type 2 open gear drives typically consist of an actuator, pinion and a gear or a series of connecting gears used to transmit continuous loads. They are normally used to power stationary or semi-stationary equipment such as kilns, grinding mills, rotary furnaces, dryers, debarkers, rubber mills, paper mills and finishing mills.
Type 2 open gear drives typically operate at or near their design limits and are often exposed to abrasive contaminants and wear debris. They usually consist of single helical and double helical-type gears.
Open Gear Lubricant Requirements and Industry Standards
Open gearing applications, particularly those associated with ball mill and finishing mill applications, are considered some of the most difficult applications a lubricant can encounter. Generally, these types of open gears operate at low pitch line velocities and/or under heavy loads.
However, more recent designs on equipment require open gearing to transmit increasingly higher loads. Because of these considerations, an open gear lubricant must possess the following characteristics and properties:
-
Tackiness (adhesive/cohesive properties) – excellent adhesion to the gears
-
Resistance to water washout and spray-off
-
Load-carrying capability to protect against friction and wear
-
Protection of the gears against wear and corrosion
-
Cushioning ability (vibration reduction)
-
Sprayability and/or ease of dispensability
- Alleviation of housekeeping and maintenance problems
-
Resistance to fling-off
-
No buildup in the roots of the gear teeth
-
Drainable for ease of removal from guards
Several industry-wide specifications and standards have been developed for open gear lubricants by the American Gear Manufacturers Association (AGMA) and different original equipment manufacturers (OEM). The most widely used is AGMA 251.02 (which has been incorporated into AGMA 9005-D94 and AGMA 9005-E02) and U.S. Steel 226 and 236. The requirements are detailed in Table 1.1
Table 1. Open Gear Lubricant Standards
The AGMA 9005-D94 and AGMA 9005-E02 stipulate the use of residual compounds 14R and 15R for open gearing when the open gear lubricant is applied by intermittent application methods, where the pitchline velocity does not exceed 7.5 meters per second (1,500 feet/minute). The stated viscosities for 14R and 15R are 428.5 to 857.0 and 857.0 to 1,714 cSt at 100ºC respectively.
In addition to the AGMA specifications, different OEMs of mining machinery and open gearing units have their own benchmark tests and specifications. Falk specifies that an open gear lubricant must have a minimum viscosity of 857 cSt at 100°C, while Sevedala specifies the open gear lubricants have a minimum viscosity of 150 cSt at 100°C. The remaining OEM requirements for mining machinery are outlined in Table 2.1
Table 2. OEM Open Gear Lubricant
Performance Requirements
Types of Open Gear Lubricants
Currently, the lubricants used by both Type 1 and Type 2 open gears consist of the following:
-
Asphaltic type (also referred to as residual compounds)
-
Semifluid greases (also know as paste type)
-
Semifluid grease cutbacks
-
Gel/polymer-thickened types
-
High-viscosity synthetics
Each of these open gear lubricants possesses performance and compositional characteristics that define their capabilities.
Asphaltic Type
Asphaltic-type open gear lubricants are known as residual compounds or black oils. This type of open gear lubricant has been used for years and is considered a reliable among operators. They are formulated from high-viscosity mineral oils or residual compounds that contain a high level of asphalt or bitumen and a volatile solvent diluent, which is used in the application of the product. Typically the residual black oils used in the formulation have viscosities of 643 cSt or higher at 100ºC.
Asphaltic open gear lubricants operate on the principle of an oil film separating the mating surfaces of the pinion and the gear. They are generally applied through an automatic spray system. Once applied to the gears, the meshing action causes the solvent diluent to flash or it evaporates, leaving behind a viscous coating of lubricant.
In the past, chlorinated solvents such as 1,1,1-trichloroethane, perchloroethane, perchloroethylene and trichloroethylene were used as the volatile solvent diluent due to their nonflammability, rapid evaporation rates, ability to improve pumpability in automatic lubrication systems, to improve efficiency of spraying and their relatively low cost.
Although the chlorinated solvents provided excellent performance, concerns from environmental and health standpoints arose due to their potential as an ozone depletory and the possibility of being carcinogenic, which lead to the ban of their use.
These concerns resulted in lubricant manufacturers of asphaltic-type open gear lubricants to either use hydrocarbon-type solvents or fluorinated hydrocarbon solvents. The use of these solvents raised concerns over the potential for onboard fires on mining machinery and equipment due to their lower flash points, toxicity issues with fluorinated hydrocarbons, volatile organic compound (VOC) emissions reporting and their slow rate of evaporation.
Asphaltic-type open gear lubricants are used due to the high viscosity imparted by these products that inhibit the meshing gears from contact. The high viscosity also enhances the product’s adhesiveness. However, the high viscosity of asphaltic lubricants is not necessary for the proper lubrication and the minimization of wear of open gears. Asphaltic-type open gear lubricants are suitable for use in the lubrication of open gearing provided the gear speeds and operating or ambient temperatures remain steady.
At high operating and ambient temperatures, they become less viscous and adhesive resulting in housekeeping problems and higher lubricant consumption rates. High ambient and operating temperatures can also cause the asphaltic-type open gear lubricants to readily oxidize, harden and buildup in the root zone. At low temperatures they tend to provide less-than-satisfactory performance due to their difficulty to dispense and tendency to stiffen, crack and peel-off leaving the gears unlubricated. They also have a tendency to build up in the root zone in low temperatures.
Due to the adhesive nature of the asphalt and bitumen containing oils, asphaltic-type open gear lubricants attract dust, dirt and other contaminants, which can become abrasive wear particles during the meshing action of the gears.
Semifluid Greases and Semifluid Solvent Cutbacks (Paste Type)
Semifluid greases and semifluid solvent cutbacks were first introduced in Europe approximately 50 years ago. These types of open gear lubricants are widely used and specified in Europe for primary mill open gears and on European manufactured equipment. This type of lubricant is applied before the gear mesh to the loaded side of the tooth in small quantities.
These types of open gear lubricants typically contain a medium- to high-viscosity petroleum base oil, which may contain some asphalt or bitumen. They may also contain a synthetic oil, gelling agent or thickener system such as aluminum complex or lithium complex, solid lubricants such as molybdenum disulfide and graphite, rust inhibitors and extreme pressure (EP) agents.
Because these types of open gear lubricants contain a thickener system, they are commonly referred to as paste-type open gear lubes. Their consistency ranges from an NLGI grade 0 to 1. The cutback versions contain a volatile solvent to enhance the product’s ability to be applied with spraying and automatic lubrication systems, especially when low temperatures are encountered.
Paste-type open gear lubricants allow the gear and pinion surfaces to operate under boundary lubrication conditions. The paste type’s EP agents and solid lubricants such as molybdenum disulfide, graphite, acetylene black and other ingredients work together to achieve the desired result of minimizing gear wear under boundary lubrication conditions. Each ingredient has a role to play. First, the thickener system holds the base oils in place.
Secondly, the EP additives protect the base metal of the gears. In short, they prevent welding of the gears. Thirdly, the product’s base oil does not provide a full-film thickness that is needed to separate the gears even with smooth surfaces. The solid lubricants complement the lubricant by maintaining a solid film that separates the contacting gear surfaces.
Paste-type open gear lubricants, when applied to open gearing, produce a thick, tenacious, semi-dry working film that separates the gears during mesh. This semi-dry film does not buildup in the roots of the gears unless it is overapplied or encounters high operating temperature conditions. The formation of this semi-dry film allows the use of paste-type open gear lubricants in moderately dirty and dusty environments without forming abrasive compounds.
Paste-type open gear lubricants can be formulated to be either thixotropic in nature (shear thinning) or dilatent (shear thickening), as required for the application through a change in composition. These properties can be achieved through the amount of thickener used in the formulation of the lubricant or through the use of volatile solvents. When solvents are utilized it evaporates after application, leaving behind a thick layer of grease that clings to the gear tooth surfaces.
These types of open gear lubricants can be used in the lubrication of both Type 1 and 2 open gears. The following has been observed when paste-type open gear lubricants have been used:
-
Less drippage and better housekeeping due to the good adhesion characteristics on vertical surfaces.
-
Use as a multiservice lubricant in open gears, bearings and bushings, resulting in simplified lubrication, a reduction of inventories and elimination of lubricant misapplications, which can result in downtime.
-
Formation of a pliable lubricant film that is easier to clean off the surface of gears for maintenance inspections, repairs and welding.
-
Lubricant consumption rates are typically two to three times higher than other open gear lubricants due to the paste type’s tendency for the base oils to separate from the thickener system when high shock loading conditions or high operating temperatures are encountered.
Gel/Polymer-thickened Type
Gel/polymer thickened-type open gear lubricants were first introduced into the market in the 1980s. These types of lubricants are similar to paste-type open gear lubricants because they contain medium- to high-viscosity petroleum or synthetic base oils that are thickened with a polymeric thickener, EP agents and solid lubricants to enhance their thin film and boundary film performance.
Some products that fall in this classification contain volatile solvents for ease of application. These types of open gear lubricants are typically NLGI 00 to 0 in consistency or are semifluid in consistency.
Gel/polymer-thickened open gear lubricants are thixotropic in nature. The thixotropic property allows friction to be reduced to a minimum, and aids in their ability to be applied by standard intermittent spray systems, or be used in splash or idler immersion systems.
Once applied to the surface of the open gearing, gel/polymer-thickened open gear lubricants form a thick, tenacious, opaque, semitransparent film coating on the gears that can be observed during inspections when using a strobe light while the equipment is operating.
Gel/polymer-thickened open gear lubricants will not build up in the root zones of the gearing. The lubricating film will not rupture, especially during high shock loading conditions. Typically, the stability of the of gel/polymer-thickened open gear lubricants is good while their long-term stability is excellent, because the base oils shows little or no tendency to separate from the gel.
Intermittent spray system maintenance may be reduced and system reliability increased with the use of these open gear lubricants. Due to their good-to-excellent pumpability characteristics, the spray system’s pumps, metering devices and conduits are subjected to less stress.
It is less likely that a spray nozzle will foul due to the lubricant drying out, which often occurs when using asphaltic-type open gear lubricants or a product that contains solvents. When the intermittent spray is functioning properly, gel/polymer-thickened open gear lubricants can provide reduced consumption rates below the recommended AGMA guidelines. Even at a reduced application rate, these types of open gear lubricants can reduce pinion temperatures by as much as 30ºF.
Gel/polymer thickened-type open gear lubricants drain from gear guards and readily flush and remove contaminants from the wearing surfaces of the gears. They do not adhere to dust or dirt contamination and do not present any housekeeping problems other than those associated with over application of the product to the gearing.
High-viscosity Synthetic Oils
High-viscosity synthetic oils appeared in the marketplace in the early 1990s. These are formulated from medium- to very high-synthetic base fluids, such as polyalphaolefin (PAO) and polyol esters, or a combination of both, and contain EP agents and rust and corrosion additive systems.
Some products may also contain solid lubricants such as molybdenum disulfide that is dispersed into the lubricant in a colloidal suspension, or contain viscosity index improvers to enhance the viscometric properties of the synthetic base fluids. Also, the use of viscosity index improvers has traditionally been considered unacceptable by gear manufacturers.
Although these products exhibit high viscosities, concerns exist when under conditions of high loads and shear, the product’s viscosity index improvers can be sheared. This results in a permanent loss of viscosity that is contributed to the viscosity index improvers.
Various types of synthetic base fluids such as PAOs have inherently low traction properties, which result in low fluid friction in the load zone of the mating gears. This reduced fluid friction produces lower pinion and gear operating temperature and improved gear efficiency.
These types of open gear lubricants conform to the AGMA 14R and 15R viscosity requirements. Like asphaltic-type open gear compounds, they operate on the principle of an oil film separating the surfaces of the gear and pinion and are applied in the same manner as asphaltic-type open gear lubricants.
In some cases, modifications including increasing the operation pressure of intermittent spray systems may be necessary to properly apply the lubricant due to its high viscosity. These types of open gear lubricants, when applied by intermittent systems, need to be utilized according to the guidelines found in ANSI/AGMA standards 9005-D95 and AGMA 9005-E02. If application rates below the AGMA guidelines are used, increased pinion operating temperatures and gear scuffing can occur.
High-viscosity synthetic lubricants are used because of the high viscosity imparted by these products. This viscosity also enhances the product’s adhesiveness. However, the high viscosity of these gear lubricants is not necessary for the proper lubrication and minimization of wear for open gears. These lubricants are acceptable for use in the lubrication of open gearing provided the gear speeds and operating or ambient temperatures are at optimum levels.
They are primarily used where high operating temperatures are encountered due to their inherent oxidative and thermal stability. At low operating temperatures, heat tracing and drums heaters may be necessary to obtain a proper spray pattern. Though they contain synthetic base fluids, the high-viscosity synthetic base fluids have pour points ranging from -5ºF to 15ºF.
High-viscosity synthetic lubricants have a substantially higher initial purchase cost than traditional open gear lubricants. Their economic justification is claimed through reduced lubricant consumption in total loss systems, extended service life in splash, transfer pinion and circulating systems, and reduced lubricant disposal costs.
Reference
- Nicholas Samman and Shek N. Lau. “Grease-based Open Gear Lubricant Multi-service Product Development and Evaluation.” Lubrication Engineering magazine, April 1999.
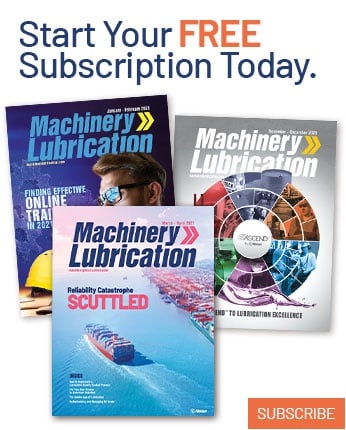