In leading maintenance organizations, managers don't shrug off the importance of cleanliness. Instead, we are seeing these companies intrepidly improve fluid cleanliness targets over and over in their quest to enhance machine reliability. However, this practice has led to new challenges relating to both the ability to achieve the new targets and the cost of cleanliness. Filter flow rate is the opportunity.
Consider this: When you reset your target cleanliness by reducing the ISO Code by one number in each range-number slot, say from ISO 19/16/13 to ISO 18/15/12, then you will have approximately half as many particles in each gallon (or liter) of oil. This will, of course, reduce the number of potential abrasive contacts within your machine by around 50 percent - your goal.
Once you achieve this new cleanliness target (say, with the aid of a portable flushing filter), your system filter will be removing half as many particles as before. After all, a filter can remove only those particles it sees. If you reduce the number of particles it sees by 50 percent (caused by the new ISO target) then your particle removal rate will be lowered by the equivalent number unless you change something else. The risk is a gradual increase to previous contaminant levels (ISO 19/16/13).
When Beta Ratio is Not Enough
So what else could you change to stabilize your cleanliness? Try reducing ingression. Figure out where your particles are coming from and block their entry. Sometimes improved cleanliness alone can sharply deter ingression from internally generated wear debris and seal damage. Ingression management is always the sensible choice in terms of contamination control economics. All other things being equal, when ingression is cut in half, filters have the amazing ability to last twice as long.
You can also change your filter performance. Many companies upgrade their filters to higher Beta Ratios (capture efficiency). However, if you went from a Beta (X) of 10 to a Beta (X) of 1,000 you only get around a 10 percent increase in the number of particles removed per minute of filtration time. This helps and is often a smart move, but if your ingression level stays the same (number of particles entering your oil per minute) then you may still have a hard time stabilizing your new target ISO Code. Remember, your filter now sees 50 percent fewer particles per gallon (liter) of oil.
The Unheralded Strategy
So what's left? We've reduced ingression somewhat and improved our Beta Ratios but we still can't stabilize cleanliness. One approach is to add a filter. Many companies are retrofitting their machines with off-line filters (also known as kidney loop filters) to increase filtration flow rate. When you double your collective filter flow rate (that is, flow through all machine filters) with the same upstream contaminant level, then you remove twice as many particles per minutes of filtration time. However, if your upstream particle count has 50 percent fewer particle than before (remember your new cleanliness target) and your filter flow rate doubles with no change in Beta Ratio, then at last, you are able to stabilize to your target cleanliness level!
There are many advantages to installing off-line filters in addition to higher filtration flow rate. These include:
-
Better filtration economy (low dirt-removal cost) compared to many full-flow, pressure-line filters
-
Better life-cycle capture efficiency (Beta)
-
You can easily combine water and dirt removal filtration
-
Convenient oil sampling (install your sampling valve between the pump and the filter). You can also install a variety of online oil analysis sensors on the market today (particle counters, moisture, viscosity, wear debris, etc.).
-
Ability to use your off-line pump and filter to charge your machine with oil after a drain or add filtered makeup fluid periodically
-
Addition of heat exchanger or system preheater
-
Convenience in changing filters (no need to use a duplex canister with a switching valve)
-
You can run your off-line filter even when your machine is off (a one-shift machine can be filtered 24/7).
Of course there are a few disadvantages to installing an off-line filter. The main ones are the hardware cost (pump, motor, filter, gauges, sampling port, valves, etc.) and installation. Many filter suppliers have prepackaged off-line filters covering a range of filter flow rate options, features and accessories. I recommend that you go with one of these integrated do-it-for-me systems. But mostly, I recommend that you make wise choices in pursuing your contamination control game plan.
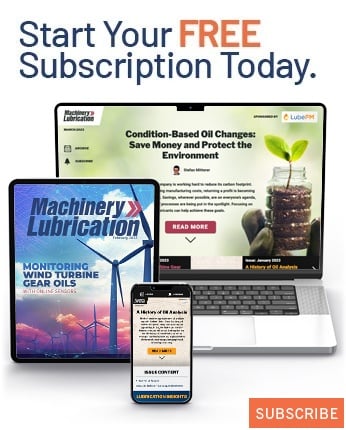