Clean, Dry and Cool
For years, the recommended fluid conditioning advice from original equipment manufacturers was to keep the fluid clean, dry and cool. Unfortunately, the conventional methodology for addressing oil contamination has often led operations to adopt a disjointed solution. In most process systems, some form of full-flow filtration has been incorporated to eliminate particulate contaminants. These filters are routinely monitored and maintained as a critical component of the overall processing system. However moisture, which is equally harmful, is an issue that has rarely been addressed.
Recently, production advances have combined with modern developments in fluid conditioning technology to lead to a convergence that has enabled system operators to address all forms of fluid contamination on an uninterrupted, continuous basis.
With continuous oil conditioning, it is now possible to enhance the performance of lubrication and hydraulic systems. The benefits of continuous oil conditioning include:
-
Particulate contamination - Reduced to levels not generally obtained with conventional full-flow systems.
-
Water contamination - Removal of virtually all free, emulsified and dissolved moisture.
-
Thermal contamination - Unique air/oil exchangers can remove residual heat from oil reservoirs.
Finally, because this advanced conditioning technology is completely scalable, it is economically practical for use with oil reservoirs ranging from a few gallons to systems containing several thousand gallons of oil, as well as viscosities ranging from turbine oils to paper machine lubricants and high-pressure gear oils.
Moisture Contamination
In oil, water can exist in three different phases. Free water will form a distinct phase that settles to the bottom of an oil sample in most mineral and synthetic oils. Emulsified water is a dispersion that will not settle and causes an oil sample to have a cloudy or hazy appearance. Dissolved water is actually in solution with the oil, making removal difficult. Also, similar to relative humidity in air, dissolved moisture gives no obvious indication of its presence or its concentration.
It is assumed that typical lubrication and hydraulic fluids, at normal operating temperatures, can contain from 100 to 400 PPM of dissolved water without any visible indication of contamination. Unfortunately, the presence of moisture will have a detrimental effect on the life of the fluid and the equipment itself. A recent study conducted by the U.S. Navy indicated that reducing the dissolved moisture content of a standard bearing lube oil from 500 to 50 PPM will result in a bearing life extension of 300 percent. This example illustrates that to truly optimize overall system performance, it is necessary to eliminate all free, emulsified and dissolved moisture from the fluid.
Moisture ingression can result from many different situations. The more obvious sources are applications involving leaky seals (a continual form of ingression) and periodic equipment washdown. When the goal is to ensure that fluids are dehydrated to 50 PPM and lower concentration levels, the ambient ingression process becomes a continual method. Because the relative moisture content of the fluid is lower than the moisture in the ambient environment, any contact between the ambient air and the fluid will cause ingression. As a result, the dehydration of the fluid needs to be part of an ongoing and continual process.
Conventional Technologies
Depending on the particular industry, various technologies may have been used to remove moisture from oils. Some technologies, such as centrifuges, coalescing filters and settling tanks have been used for the removal of free water from oil. Water-absorbing filters have also been used; however they tend to become economically impractical when there is a need to remove large quantities of moisture. Another option, and one of the only conventional products that was previously suitable for the removal of water in all three phases, is the vacuum purifier. Unfortunately, due to the complexity of operation and relatively high purchase and operating costs of vacuum dehydrators, they are typically justified only for large or costly pieces of equipment.
One legacy associated with these conventional technologies has been the adoption of periodic oil dehydration. In most applications, if oil dehydration was performed, it was part of a periodic maintenance routine or after a system upset had caused the oil to become contaminated. This leads to an ongoing contamination remediation cycle, where the moisture content of the oil is typically at an elevated state.
Continuous Oil Conditioning
The UltiDriTM oil dehydration system has been developed to address the most stringent requirements placed on lubrication and hydraulic systems. One key characteristic of this technology is the patented membrane dehydration contactor design.
The UltiDriTM functions as a mass transfer or moisture exchanger. The moisture is transferred from an area of high concentration (the oil) to an area of low concentration (a dehydrated stream of air). It is important to note that the moisture diffuses through the contactor, therefore there is no potential for air entrainment in the oil or oil carryover in the air stream.
Because the air used for the mass transfer of moisture is completely dry (less than one percent relative humidity), the system can reach extremely low levels of moisture content within the oil. In many cases, dissolved moisture levels of 25 to 50 PPM or lower have been attained. And because the system runs continuously, the oil is constantly maintained at this level. In addition, the moisture is transported out of the dehydrator via a dry air stream, therefore the oil is dehydrated without creating any waste byproducts.
How It Works
-
GenesisTM particulate filter eliminates solid contaminants.
-
Oil flows through patented dehydration contactor.
-
Dry air flows through opposite side of dehydration contactor.
-
Air with absorbed moisture is exhausted.
-
Dehydrated oil is returned to reservoir.
For the dehydration system to be practical for reservoirs of all sizes, the contactor has been engineered to be scalable, providing the appropriate amount of dehydration capacity required for each application. In large-volume or high-ingression situations, a larger dehydration contactor(s) can be used. For smaller reservoirs or low-ingression environments, relatively small contactors can be designed. This helps ensure the systems remain economically viable for all types of applications.
The system was engineered for ease of use, and the need for routine maintenance and service has been eliminated. There are no pressure/vacuum valves to adjust, no level controls to maintain and no need to drain water. The concept of transparent operation means that, once installed, the system will remove both moisture and particulate contaminants in a continuous manner without routine operator intervention.
Finally, each dehydrator is engineered to operate at the normal oil reservoir temperature. There is no need for additional equipment and expense or the potential damage to the oil associated with either heating or cooling.
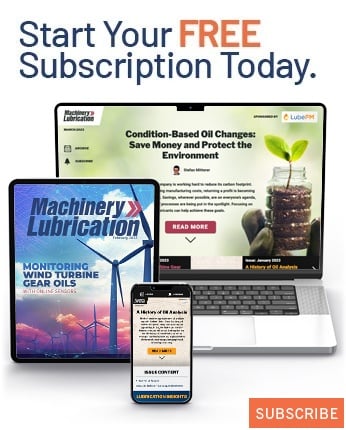