For the last forty years or so, spectrometric analysis of lubricating oils has been used to determine the concentration of wear metals, contaminants and additives present in oil samples.
This type of analysis is sensitive to low levels of particles and dissolved materials, it has good repeatability, and it is fast and economical. Most commercial oil analysis labs provide spectrometric oil analysis for as little as $5-7 per sample in large quantities.
What is often not understood, however, is that the ability to detect and quantify wear, additive and contamination particles is directly related to the size of the particle. All spectrometers suffer from the inability to detect large particles, typically larger than 10 micrometers.
The failure to adequately detect larger particles is due in part to the large amount of electrode arc energy consumed by the lubricating oil present in the sample.
These large particles are precisely those particles which are most indicative of an abnormal wear mode. Severe wear modes such as spalling, severe sliding wear and cutting wear generate large particles which may go undetected by spectroscopy.
Recently, a new technique was introduced which efficiently captures large wear particles in an oil sample prior to analysis with an emission spectrometer. It has been referred to as rotrode filter spectroscopy (RFS) because it uses the porous disc electrode as a filter to capture wear debris particles.
RFS takes advantage of the convenience of rotating disc electrode spectrometers, but is able to detect a larger particle range. To understand how this is accomplished, let’s look at how rotating disc electrode spectrometers work.
A carbon disc is pressed onto the end of a rotating shaft. An oil sample is poured into a sample cap and positioned so that the bottom of the carbon disc rotates through the oil sample. A spark gap is formed between the top of the disc and the tip of a carbon rod electrode.
Oil that is carried by the disc to the top of the electrode is vaporized. The light that is emitted has wavelengths that are characteristic of the elements present in the sample, and the intensity of light is proportional to the quantity of the element present. Multi-element analysis can be obtained in 30 to 40 seconds, and twenty or more elements can be simultaneously determined.
RFS makes use of the fact that the carbon disc electrodes are themselves porous. A fixture was designed to clamp the removed disc so that oil can be vacuumed through it. This filtration process concentrates the particles from a much larger volume of oil than would normally be analyzed by a spectrometer, increasing the sensitivity.
The oil is then washed away with solvent, the disc is allowed to dry, and particles are left on the disc electrode. The disc is then rotated through clean oil. The emission coming from the disc is due to the particles remaining on the disc.
A multi-station fixture is used so that a number of samples can be filtered at once, allowing the procedure to be fast and economical to perform. Sample preparation time of an electrode for rotrode filter spectroscopy varies with the viscosity and contamination of the sample.
Preparation time can be as short as 4 or 5 minutes for relatively clean used lubricating oil samples, such as from turbines, electric motor bearings and hydraulic systems. Engine oil samples with high soot levels require the longest filtration times, sometimes half an hour or more. Use of the multi-station fixture really makes sense in these situations.
The rotrode filter spectroscopic data provides the information to tell when a ferrogram should be made. This is important from a cost standpoint because it is much less expensive to perform the rotrode filtration test than to make and analyze a ferrogram. For more information on the rotrode filter method contact Dan Anderson, Spectro Incorporated, 978-486-0123 or visit the Spectro website.
Ref: Anderson, Daniel, “Rotrode Filter Spectroscopy,” PPM Magazine, 1992
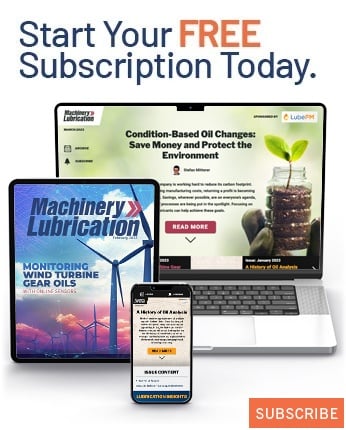