Today's lubricants need to meet higher performance requirements than ever before, especially when it comes to extreme pressure situations. That's why many plant managers are turning to synthetic oil lubricants to improve plant efficiency and performance, while reducing cost and energy consumption.
Synthetic lubricants are different from traditional mineral oils in that they are engineered by combining smaller molecular building blocks to meet targeted performance specifications, such as size and structure. This means that synthetic lubricants are available in a wider range of formulations, allowing customers to more closely match a lubricant to their specific service requirements. In addition, because synthetic oils are formulated under carefully controlled conditions, manufacturers can minimize impurities, which often lead to oil degradation and machinery damage.
Although certain additives can boost the performance of traditional mineral oils, new synthetic oil technology offers a high viscosity index, improved thermal and oxidation resistance and viscosity-temperature behavior, low-temperature properties, and resistance to ambient media. Synthetics also have lower evaporation losses and a lower tendency to form residues.
For example, synthetic lubricants have been shown to boost air compressor performance significantly. Industry service life standards for synthetic lubricants such as PAO and polyalkylene glycol (PAG) compressor oils are often reported as at least 8,000 hours, and polyolester (POE) compressor oils can often approach 14,000 hours of service life at discharge temperatures of 180°F. This far exceeds the expected 4,000 hour service life for mineral oils or even less with lower quality oils, motor oils and ATF.
Many new lubricants are food-grade compliant, which makes them an excellent option for food- manufacturing applications where incidental contact with food products may occur. Dow Corning offers a number of food-grade compliant products:
Molykote® Separator Spray is an NSF H1-certified silicone release agent that aids in the removal of food products from machinery components to improve surface quality, provide easier cleaning and reduce costs. Well-suited to improve sliding on conveyor belts, guides, slide plates and tables, Molykote Separator Spray can also be used as a release agent in rubber and plastics processing, cardboard box manufacturing and wood processing. The spray is transparent and has a service range from -40°C to +200°C.
Molykote® Food-grade Spray Oil is an NSF-certified, highly refined oil with special additives formulated for the food, pharmaceutical and similar industries. A multi-purpose mineral oil aerosol, it can be used to lubricate bearings, gears, chains and sliding mechanisms in food and beverage processing application and are suitable for lubrication points with low-to-high loads, moderate-to-high temperatures, and moderate-to-high speed applications. The oil offers good penetration, high corrosion protection and high load capability, and a service temperature range of -10° to 120C° (-13° to 302°F).
Molykote® P-1900 is a mineral oil-based paste that can be used to lubricate sliding surfaces and friction contacts exposed to heavy loads, especially at low to medium speeds. It has a low coefficient of friction, good water resistance and high load carrying capacity. It has a service temperature range of -30° C to 300°C. Molykote P-1900 is available in 400 g cartridges, 1 kg cans, 25 kg pails and 180 kg drums. Samples are available in 1 kg cans.
With the appropriate lubrication management strategy, a high-performance synthetic can cost considerably less than the equivalent mineral oil product type, providing real dollar cost savings in a variety of applications.
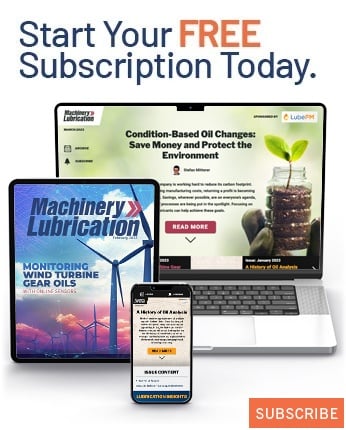