Anybody who has been in the lubrication field for at least a couple of years has likely been badgered by problems relating to air contamination. Indeed, aeration and foam present many serious reliability concerns which merit immediate attention by machinery maintainers. However, for most people, the causes are too complex to troubleshoot, leaving the root-cause mystery unsolved. Sometimes an oil change provides a suitable remedy, but too often it serves as only a temporary fix. In other words, there is a need to find why it happened.
Laboratory researchers have conducted numerous studies over the years relating to air contamination. From this body of work, we've learned many interesting new facts that help us both diagnose the problem and prescribe corrective actions. Some of these new insights into the causes and effects of air entrainment and foaming problems were discussed in the article "The Perils of Aerated Oil - Let Your Machine Burp", published in the January 2005 issue of Practicing Oil Analysis.
In this column, I want to share more snippets of information that can be useful in the control of air contamination. I'm guessing that even seasoned oil analysis and lubrication professionals will pick up a pointer or two. This is my list:
Clues to Curbing Air Contamination
-
Pure mineral oils do not foam. Additives and impurities cause foaming. With few exceptions, the more polar additives (AW, EP, dispersants, etc.) in an oil the more foaming problems that generally occur.
-
Average air bubble size in oil decreases with decreasing interfacial tension. The smaller the air bubble formed, the greater the foam formation tendency and stability.
-
Water contamination in oil reduces interfacial tension which, in turn, leads to air entrainment and foaming problems. Just 1,000 ppm water is enough to induce stable foam formation in many oils.
-
The higher the viscosity the oil and the smaller the entrained air bubble size, the longer the air release time (Stoke's Law), and the greater amount of entrained air an oil will hold. By doubling air bubble size, the time it takes to rise to the surface is reduced to one-fourth.
-
Foam bubble size is inversely proportional to viscosity. Low viscosity oils tend to make large foam bubbles that break and collapse rapidly. High viscosity oil produces small bubbles that are difficult to break, resulting in more stable foam (lasts longer).
-
Low viscosity oils (ISO VG 10 to 32) have the highest foaming tendency at cold startup temperatures (-10°C to 10°C). Conversely, high viscosity oils (VG 460 to 1,000) have the greatest foaming tendency at operating temperatures (30°C to 60°C). Foaming tendency above 100°C is uncommon for oils with viscosities in the range of ISO VG 32 to 1,000.
-
Ten percent entrained air increases viscosity in many oils by about 15 percent. Mixtures of air in oil above 30 percent are generally referred to as foam.
-
After a long time, a stable foam will become dry and fragile and will break at the slightest mechanical or thermal shock. The liquid has drained out of the network of bubbles, leaving a plastic-like film about 12 nanometers thick which appears black due to optical interference.
-
Deep narrow tanks are more prone to foaming than broad flat tanks.
-
Mechanical restrictions (for example, elbows, line restrictions, etc.) called vena contracta regions, lead to air coming out of solution. This can cause cavitation and microdieseling.
That's my list. Do you have information on aeration and foam worth sharing? Have you found new solutions to this old problem? If so, don't be bashful; let us hear from you. And remember, don't underestimate the destructive potential of air.
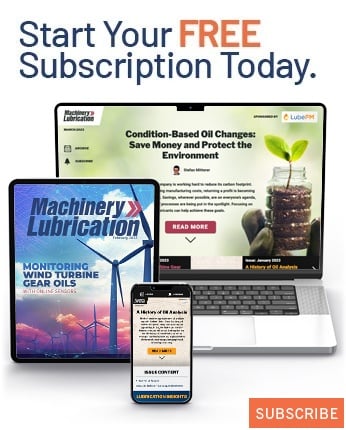