In January 2006, a large inland marine company purchased heat transfer oil from O'Rourke Petroleum's Lubricants Department for a cargo barge in its fleet. The fluid was to be used in the heat transfer system of the barge. The barge, which transports lubricating oil to different destinations, was encountering problems with the heat transfer system within the barge's cargo storage tanks, thus belching oil out of its venting system. The marine company assumed it was due to water leaking inside the heat transfer system, and contacted Lubrecon Systems, Inc., a service branch of O'Rourke Petroleum to analyze the situation.
Where Is the Water?
After the initial analysis, Lubrecon found that the heat transfer oil lines in the barge had been accidentally steamed out, misplacing several gallons of water into the heat transfer system. A plan was then devised involving a vacuum dehydrator and miscellaneous hoses to correct the issue.
When Lubrecon began the job, it discovered the system was much older than expected and the design was not conducive to properly connect with its equipment. The company decided to remove the suction spool of the pump to provide access to the expansion tank. Dried oil was also supplied to the entire system through the discharge of the permanent system. As we dried the oil, it was pumped back into the heat transfer system.
After setting up the dehydrator and connecting the hoses to the system, the marine company fired its heater and circulation pump to bring the oil temperature to 150°F. After the system was circulating properly and the heat was maintained throughout the system, it was time to get to work.
Lubrecon Saves the Day
Within one hour Lubrecon pulled and drained eight gallons of water from the heat transfer system. Over the next 60 hours, Lubrecon removed a total of 65 gallons of water from the system. At this point, the barge needed to be released back into the fleet. Before this could take place, the inland marine company wanted Lubrecon to test the oil to verify the amount of water remaining in the system.
After the oil was tested, the results indicated there was 0.00 ppm water in the oil. (The oil was less than 50 ppm, determined by Karl Fischer testing.) Lubrecon disconnected all of its hoses while a heater mechanic ran the oil temperature up to 250°F. During this time, a small amount of moisture was pulled out of the remainder of the system by boiling it off the oil. The marine company was more than satisfied with Lubrecon's quick response and appropriate actions taken.
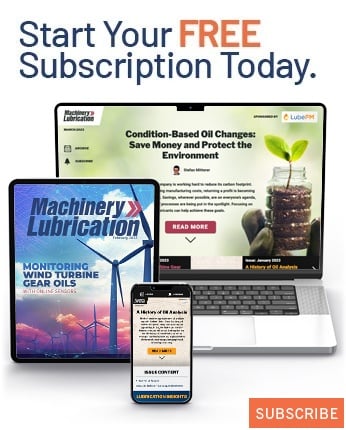