We've addressed the virtues of training numerous times on the pages of Machinery Lubrication and other Noria publications. Still today, we encounter a national workforce in the lubrication field that seems largely oblivious to many of the fundamental concepts that embody excellence in the profession.
We are not sure if it is due to them not knowing what they don't know, or not caring about what they don't know. To become aware of what you don't know requires becoming aware of your incompetencies and leaving the comfort of ignorance.
This editorial column seeks to define a minimum threshold of knowledge and awareness to qualify a person to work in the field rather than addressing the broader topics of educating a lubrication workforce.
Horns should blare and flags should shoot upward if your lubrication technicians are unable to answer each of the following questions relating to the specific machines they service. Let's get started:
About Your Machines
-
What is the description and name of the lubricant used? The answer should include the viscosity (for example, ISO viscosity grade) and lubricant classification (for example, synthetic EP gear oil). Next, either the commercial product designation or the identification naming system used by the company should be known (or is quickly accessible).
-
What is the relubrication frequency or criteria? Some machines are set up on relubrication routes while others get only occasional top-ups as needed. Still others may be serviced in response to a measured or inspected condition, such as remaining useful life from oil analysis.
-
What is the correct relubrication procedure as documented by the OEM or qualified lubrication specialist? Lubrication procedures often vary from technician to technician based on convenience or preconceived notions of best practice. These methods of personal choice can depart significantly from OEM- or industry-defined best practices. The correct procedure needs to be established and routinely applied.
-
How is the machine tracking to the three proactive maintenance targets: cleanliness, dryness and temperature? These are the silent assumptions of machine reliability (among others). These targets need to be known, as well as the current state of the machine against these targets. Of course, a remediation strategy needs to be established and scheduled if the machine falls out of compliance.
-
What are the daily inspection PMs? How is lubricant volume or level confirmed? How about filter condition, flow rate, pressure, ventilation, oil color and BS&W? What are the alarming criteria for these inspections? How is nonconformance reported and corrected?
-
When, where and how are oil samples taken? Who takes them? For critical machines, oil analysis is definitely not a trivial matter. A host of important decisions can emerge from this data. Oil analysis quality begins with oil sampling quality. Being sophisticated about sampling methods is a fundamental precept of lubrication excellence.
Of course knowing and doing are mutually exclusive concepts. As the motivational author Stephen Covey has said, "to know and not to do is really not to know." Therefore, being able to answer these questions is indeed an important and fundamental starting point. However, daily execution of this knowledge is what sets apart the average organization from best in class.
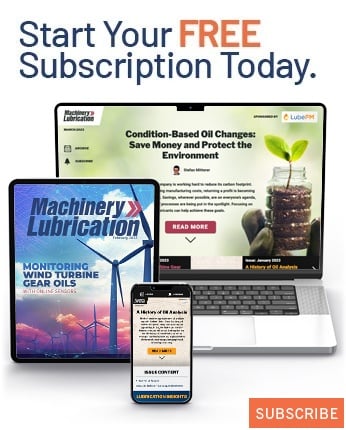