Liberty Paper, a paper mill in northern Minnesota, manufactures linerboard from recycled corrugated containers. The mill runs 24 hours a day, 7 days a week. A Valmet paper machine operates at a maximum speed of 2,000 fpm and produces up to 1.9 million square feet of linerboard per hour. The paper machine main lube system services both wet and dry ends.
The Problem
Paper machine oil temperature normally operates near 120°F. During planned mini shutdowns (several hours), tank heaters prevent the lube oil from cooling below 95°F. However, upon restarting oil flow, the cooler and more viscous paper machine oil was collapsing full-flow filters in the main lube system. Collapse of the main lube filters caused previously collected contamination in the filter element to be released downstream. During one of these catastrophic filter failures, filter wrap material actually passed into the main lube circuit.
A second problem occurred during regular filter change-outs. When removing a filter element from its housing, contamination collected on the upstream surface of the element (outside to inside flow) was dislodged. Liberty Paper was concerned that some of these damaging contaminants passed downstream and got into the bearings.
Liberty Paper needed improved filter technology for better reliability.
The Solution
The mill had recently installed new Donaldson T.R.A.P.™ regenerable air breathers to prevent moisture ingression into hydraulic power units and gearboxes. Liberty Paper again turned to the filtration company for its offering of filter media and efficiency.
The optimal solution was a double duplex arrangement of four HRK10 housings. HRK10 housings have a robust heavy-duty design and construction. The housings for Liberty Paper included 50 psid bypass relief valves, electrical indicator ports, and visual indicators. Figure 1 shows the actual installation at the mill.
Each housing contains one Triboguard™ DT filter element with Synteq™ media rated at ß(c)5 = 1000. Lubricant flows from the inside of the element to the outside. This basket-like arrangement ensures contaminants captured by the filter stay in the element during change-out. This more sturdy design also prevents collapse of the filter element during restarts with the cooler, more viscous oil.
Because the housings are only 33 inches in length (compared to 46 inches for comparable elements) they are lower to the ground which makes them easier to service. The HRK10 also includes a twist-and-lift cover design that eliminates the need to remove bolts, reducing the time and cost of service. The filter attaches to the bypass assembly with a finger-activated clip for convenient element removal. This ergonometric design is highly valued by maintenance personnel.
To keep production running, installation was coordinated between Liberty Paper, Donaldson and its distributor. Installation was completed and the new assembly up and running within one mini-shutdown.
-
The first set of HRK10 filter elements lasted for more than five months. Subsequent filters are expected to last as long or longer. This is well above the four months average life of previous elements.
-
Clean DP was measured at 7.5 psid.
-
Particle counts of ISO 16/14/11 are well within the mill's target cleanliness levels.
Conclusion
The paper mill asked for a more reliable and robust design. It is pleased with the serviceability, construction and performance of the HRK10 installation.
For more information, contact Donaldson Company, Inc., www.donaldson.com.
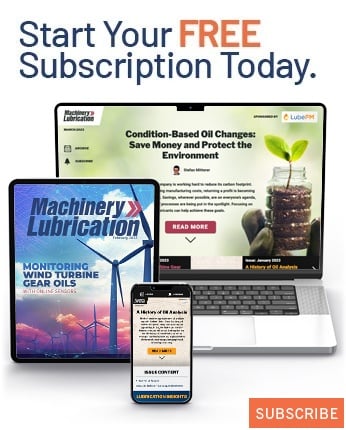