Recently, Lyon Labs has discovered a new lubrication technology that has outperformed conventional technology in a full-scale industrial application. This article describes the differences between conventional technology and this most recent technology.
Conventional Technology
Conventional technology is an extension of classical lubrication theory, which has been verified by a number of investigators, in particular by Sir Hugh Spikes of Imperial College. It describes a condition at the nearest point of contact of smooth bearing surfaces where they deflect under enormous local pressure to form a pocket of lubricant, therefore separating the metal surfaces. This is called the elastohydrodynamic effect and involves viscosity playing a major role in establishing a protective boundary layer.
Not Always the Answer
When applying this theory to real-world applications, serious anomalies arise. The relative speeds of bearing surfaces in modern gear and bearing applications are usually too low to generate a viscous boundary layer thick enough to prevent the asperities of the bearing surfaces from coming in contact with one another and breaking off wear particles.
Wear particles are present in virtually every application. The coefficient of friction generated by this wear is at its highest value upon reaching these low relative velocities where the viscous boundary layer is at its thinnest.
Formulate to Specific Needs
To cope with the asperities of bearing surfaces always being in contact with one another, especially in today's highly loaded, high-temperature applications, chemistry that forms covalent bonds with the working surfaces to retard the rate of wear to a manageable level must be added to the lubricant. The most successful of these lubricants contain antiwear (phosphate-forming compound such as ZDDP), extreme pressure and friction-reducing additives.
Some advanced formulations contain chemistry that increases the pressure-viscosity coefficient, giving the lubricant the benefit of a higher localized viscosity at the bearing surfaces in the contact zone, thus producing a thicker boundary layer at a lower bulk oil viscosity.
Monitoring Performance
Whether an oil lubricant is performing satisfactorily is usually determined by the size and number of wear particles emanating from the point of contact. Wear particle sizes of four to 12 microns are considered normal wear. Larger sizes indicate abnormal wear and dictate using a higher viscosity oil, or the chemistry of the antiwear package may have been consumed and the oil should be replaced.
Grease systems are not easy to monitor. Excessive housing temperatures and periodic inspection of the bearing surfaces for wear are typically used. Grease with a higher base oil viscosity is usually applied if excessive wear is encountered. This practice has its limitations because the higher viscosity obtained is often offset by the loss of fluidity which could produce bare spots on the bearing surfaces.
Matched Molecular Chemistry
An alternate technology is now available that is not dependent on viscosity for protecting the bearing surfaces. It can be used along with conventional technology to decrease the rate of attrition of the protective chemicals or possibly as a complete replacement. By using the enormous molecular forces inherent in certain polymers, a larger, more effective polymer can be created that can establish bonds with the wear surfaces without chemical attack.
A small amount of this polymer can be dissolved in the base oil, which will coalesce on the bearing surfaces and form a continuous quasi-static film on the bearing surfaces. This film is an order of magnitude thicker than the remaining viscous boundary layer created by the base lubricant. This is called matched molecular chemistry (MMC).
Although most of the laboratory experiments on MMC technology were performed on oils, only undocumented trials have been run against conventional oils on full-scale industrial equipment. From this data, it is reasonable to assume that the MMC concept is applicable to oils and documented, full-scale tests of industrial gear oils using MMC are scheduled.
Using the New Method
The MMC concept has been verified in documented, full-scale tests in industrial grease applications. A major steel company conducted comparative tests between grease using the MMC technology and premium greases using conventional technology in a gear-driven spindle transmitting 5,000 horsepower.
The gear set using conventional grease could transmit only 80 percent design load, required water-cooling, and failed in a few months of operation, causing hundreds of hours of unscheduled maintenance. The greases containing MMC ran at 100 percent load without cooling at near-room temperature and without any unscheduled maintenance. Upon inspection six months later, there were no signs of abnormal wear.
In the same series of tests, MMC technology grease was run in a direct comparison with a premium, high-viscosity, synthetic gear oil. The oil-lubricated gear set failed within a month running at 100 percent load with no cooling. Large wear particles were collected on a magnetic plug from the oil-lubricated gear set while none were found in the grease during shut down. A spindle used gears to transmit torque: 48.7 cSt; NLGI #1 with 220 cSt at 40°C.
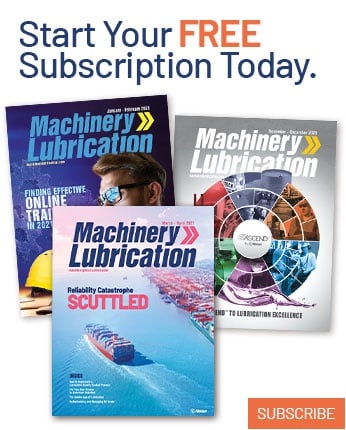