Whether producing weapons, foods, medicines or the wide spectrum of lubricating fluids, centrifuges have successfully performed their superior separating duties for many decades. A bypass centrifugal fluid cleaner falls into one of two broad categories: powered and self-powered.
Powered centrifuges use either a properly sized pump and motor package or a mechanical direct couple that will easily drive the centrifuge when insufficient or no system pressure is available. Self-powered centrifuges use system pressure that may require a suitable regulator to maintain a constant oil supply pressure (85 to 100 psi) if the system pressure is too high for safe operation.
Either way, a centrifuge takes approximately 2 to 10 percent of the total fluid flow from the main circuit, filters the fluid to a high cleanliness level and then returns it to the sump in a continuous loop (Figure 1).
Figure 1. Route of Fluid Flow
Principles of Centrifuging
Centrifuging works to accomplish the following:
-
Contaminant removal based on the relative particle density
-
Achieve maximum number of passes per hour without exceeding excess flow capacity of the pump
-
Oil flow efficiency through the centrifuge maintained throughout the service interval
Though centrifuges vary in size to correctly match sump size and the ingression rate of contaminant, they all operate in a similar method. The centrifuge separation chamber is driven at high speeds (3,500 to 8,000 rpm) by a built-in turbine powered by the pressure of the fluid being cleaned.
Table 1. Evaluation Specifics
How it Cleans
A typical centrifuge incorporates four primary components: a separation chamber, a turbine, a housing and a level control base. The fluid is cleaned by the following process:
-
The dirty fluid enters the separation chamber under pressure (45 to 100 psig) and flows up through a rifle-drilled vertical spindle.
-
This pressure and flow is converted into rotational energy as the oil exits through a pair of tangentially opposed nozzles that power the centrifuge from 3,500 to 8,000 rpm.
-
Forces on the fluid in the rotating turbine assembly can exceed 3,000 times that of gravity which separates contaminants from the fluid.
-
Particles with a higher density than the fluid migrate radially outward and accumulate around the inner wall of the rotor as a dense, hard cake.
-
The clean fluid returns to the sump or reservoir from the level control base (LCB). The LCB allows for easy, flexible mounting and installation.
For the most efficient operation of centrifugal cleaner, it is important that fluid reaches the centrifuge in the optimum condition. This effectively means that the fluid should be hot so that the viscosity is at its lowest and supplied at high pressure so that the centrifuge rotor spins at its fastest.
Therefore, on an engine application, the ideal oil supply tapping point for a bypass centrifugal oil cleaner is immediately downstream of the oil pump and upstream of the full-flow filter. In addition to tapping position, consideration should be given to selecting the shortest possible, adequately sized supply line to minimize pressure energy losses.
Oil Drainage
Oil drainage is vital to the efficient operation of a centrifuge. Fluid exiting from the rotor nozzles must be able to escape freely and allowed to return to the sump. Flooding of the rotor occurs when the drain passage is insufficient to allow natural atmospheric drainage of the centrifuge rotor housing. This causes the fluid level to rise, impinging on the rotor and significantly reducing its speed and performance.
Drainage can easily be facilitated with an LCB or by ensuring a sufficient size of drain and endeavoring to return the oil to the sump above the normal oil level. This allows air to travel up the drain pipe and maintain a free airspace around the rotor.
Because of the high gravitational forces, a centrifuge removes not only large particles but also fine, submicron contaminants. Effectiveness and efficiency are not dependent upon particle size as with a barrier filter. Rather, a centrifuge consistently removes small abrasive wear particles down to 1/10 micron. When fit to a diesel engine, analysis shows that 98 percent of the particles collected in the centrifuge are 10 microns or less. This is significant because film thicknesses of critical wear areas in the engine are also small:
0 to 2 microns - rings, liners and turbochargers
2 to 3 microns - main and large end bearings
0 to 7 microns - camshafts
Advantages
A centrifugal oil cleaner has two major advantages over a barrier media filter. First, the cleaning efficiency of a centrifuge remains constant throughout the service interval. Second, the lower limit of particle size which can be removed by a centrifuge is the point where the viscous drag forces between the fluid and the particle equal the centrifugal force to which the particle is subjected. In practice, this lower limit is well below one micron in a hydraulic fluid power application.
Maintenance-conscious managers apply centrifuges to engines, pumps, generator sets and a variety of industrial applications to clean oils and glycols, as well as hydraulic, wash and cutting fluids to improve equipment life and profitability.
Case Study: Stationary Gas Turbine
In Alberta, Canada, a compressor station moves sales-grade natural gas. The company experienced ongoing high particle counts of abrasive material in its turbine lubricant, even after several upgrades in full-flow filter type and number. The company added a centrifuge to ensure total sump turnover in less than three minutes.
The company recorded the pre-centrifuge particle count several months after initiating full-flow filter upgrades. It recorded the second particle count three months after the centrifuge installation. The evaluation specifics are shown in Table 1.
The addition of a centrifuge proved significant, demonstrating a much higher level of lubricant cleanliness than previously achieved through other methods. This brought the equipment owner significant reductions in component wear. Because of the large debris-holding capacity of the centrifuge, the end-user needs to service the centrifuge only annually, or perhaps even longer intervals in this application.
About the Author
Bob Clayton is business development manager for the Spinner II products division of T.F. Hudgins. The company provides Spinner II fluid-cleaning centrifuges and other lubrication products for a range of industrial applications. For more information, visit www.tfhudgins.com.
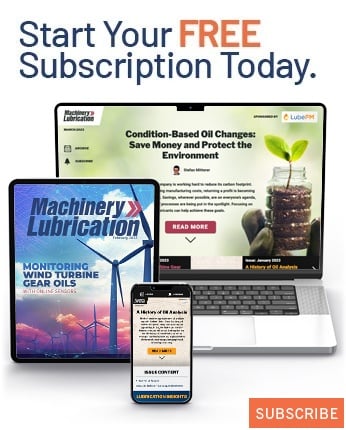