It is common to guess at the cost of a project in its planning phase, only to realize later that your initial estimate was way off. Every project in maintenance follows a similar path from planning to execution. And in every project, there are unforeseen circumstances that can take your initial cost estimates for time, materials and labor and turn them upside down.
Cost estimating is simply the exercise of developing an approximation of the cost of resources required to complete a project. This definition is simple enough in theory. In fact, we all cost estimate every day. The cost of dinner, the cost of groceries and the cost of gas are all expenses many of us estimate before the bill actually arrives. Modest skills are required to accurately estimate cost for everyday items and activities. When estimating cost for large projects like a lubrication excellence project, many considerations must be identified.
These include considerations such as identifying various costing alternatives and estimating all costs for scheduled activities like labor, materials, equipment, services and facilities. Many don't realize that initial cost estimates should be refined over the project life cycle. Changes in market conditions and the corporate landscape can have a significant effect on costs over the life of a project. Therefore, estimating is a crucial and critical component in any project accomplished internally or with external contractors.
Figure 1
Estimating Methods
There are three common estimating methods: analogous, parametric and bottom-up.
Analogous
Analogous estimating is also referred to as top-down estimating. This is one of the most common estimating tools because it uses the actual costs of a previous project as the basis for cost estimating the new project. This method, though widely used, is simply a best-guess. The logic behind this estimate is that if this project is twice as big as the previous project, it is likely to cost twice as much. Although this estimate is based on expert judgment, it is also inaccurate unless projects are, in fact, the same.
Parametric
Parametric estimating is a method that uses statistical relationships between historical data and as many other variables as possible. We see this method commonly used in construction, as in price per square foot; or in software development, as in cost per line of code written. Parametric estimating is still not significantly detailed but is an excellent tool when quick budget or planning numbers are available. Parametric estimating also requires that an up-to-date and populous historical database exists that includes details and costs on many previous projects.
Bottom-up
Bottom-up estimating is done when individual project tasks or work packages are cost estimated, and then the sums of all tasks are averaged to get a project total. This is the most sophisticated estimating method of the three methods and is the only one that should be considered legally binding. To complete a bottom-up project estimate, you need to have a fully developed and detailed scope of work. The scope of work will include detailed drawings, specifications, vendor quotes and any other details necessary to complete an accurate estimate. In addition to an accurate scope of work document, the bottom-up method requires the following elements:
-
Identification of required resources
-
Material estimates
-
Historical cost data needs to be analyzed by subject matter experts
-
Appropriate quotes on services where required
-
Calculation of composite rates for labor
Though the bottom-up method is typically the most accurate, many tend to use analogous or parametric estimates. Regardless of the method used, remember that any estimate must be adjusted over the life of the project. Therefore, it is easiest to use the most accurate method in the planning phase and adjust from there.
Dos and Don'ts
Of course, there will always be issues when estimating. Simple rules to follow include:
Don't work backward from the time constraint. In the project management field, we are constantly aware of the triple constraint of time, cost and scope (Figure 1). Many project managers will incorrectly plan their projects backward from the deadline. The schedule should be used to coordinate resources and manage against variance. Scheduling backward from a deadline does not allow us to manage against variances that are likely to occur.
Do realistically manage trade-offs. This means we want to start with a normal baseline time estimate and compare that to the time constraint. If the baseline exceeds the constraint, we need to manage the trade-offs. The triple constraint is a synergistic relationship of driving factors in all projects. If the completion time for a project is adjusted, then one or both of the other constraints (cost or scope) must also be adjusted. To reduce the time a project can take, either the scope will decrease (less work can be done) or the cost of the project will increase (more resources to do the job in less time will cost more).
Don't ignore your customers' perceptions. Whether your customer is internal or external, his or her perception of what you estimate carries a lot of weight. If your manager asks you for a budget number for a project approved for the following year, his perception of what you tell him can dramatically change the scope of the deliverable or prevent the risk from going over budget. Providing ballpark figures is dangerous business. If you tell your manager the ballpark figure is in the $100,000 to $400,000 range thinking you are covering all your bases, your manager will likely hear $100,000. Estimates should never be given without some detail or scope behind it.
Do standardize the way estimates are refined over the life of a project. Initial planning should include an estimate based on a high-level product or service definition. Upon completion of the formal scope or work, further refinement should occur. Scope changes, material specifications and outsourced labor will help to further the cost refinement. The true cost of a project will not be known until the project is complete.
Cost estimating in any project, including lubrication excellence, is one of the few metrics noticed by all levels of management, and the one measurement that will be used to provide status reports at a given point in time. Most project success will be measured against cost and cost alone. Inaccurate cost estimating can literally make or break a project. The more work done in the planning and estimating phase of your project will produce a more manageable project in later phases.
Reference
Project Management Institute. A Guide to the Project Management Body of Knowledge, Third Edition. 2004.
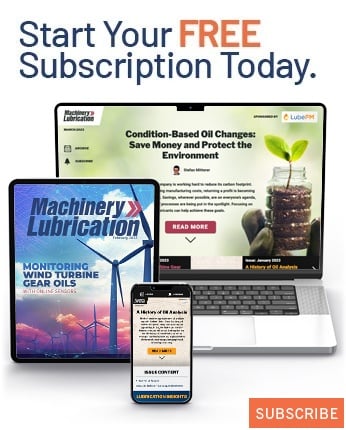