We are all familiar with blood clotting and its role in constricting blood flow after injury. Clotting depends on the coagulation of platelets and blood cells aided by fibrin molecules to trap and bind them together. This coagulated mass effectively plugs capillaries to stop uncontrolled hemorrhaging and bleeding.
Over the years, I've encountered many interesting human-body analogies to machinery lubrication and oil analysis. Blood clotting is one of the best. It is amazingly similar to a variety of conditions relating to leakage and the restricted oil movement in machinery. In both the human body and the machine, clotting can lead to positive and negative consequences. While blood clotting can contain loss of blood after a skin laceration, it can also restrict blood flow in the brain and muscle tissue of the heart. Similarly, oil clotting can mitigate or completely halt in-leakage and out-leakage in machinery. Conversely, it can impair needed movement of oil through orifices, glands, oilways and filters. This can leave critical frictional surfaces starved of lubricant, accelerating wear and failure.
How Oil Clotting Works
As we know, depending on the machine's design, leakage can be internal (oil flows from a higher pressure zone to a lower pressure zone) and external (oil escapes from the machine by leaking past seals and tight-fitting parts). Both conditions are undesirable, yet many lubricants and hydraulic fluids carry their own intrinsic packing material that can be used to clot leakage zones and oil flow passageways.
The process usually starts by the transport of a single particle in the size range of the slit or leakage path; this is the seed particle. This particle gets wedged or jammed in the gap, which might be just a few microns to well over 100 microns. Because the oil prefers the path of least resistance, it is through these larger slits and gaps that more particles are carried and then lodged. As they become lodged, the clearance (opening) constricts even further. With each narrowing iteration, the flow continues to decay, enabling smaller and smaller particles to provide the necessary packing material. Soon, the slit or leakage path is sealed tight. It is interesting that particles of only a single size (large or small) do not enable a packing seal to form; but rather, a distribution of particles sizes is required. The same is true for particles that infamously cause slit-lock and stiction of electrohydraulic valves (for example, servo valves).
Just like blood clotting depends on fibrin molecules to entangle or conjoin platelets and blood cells, oil clotting is aided by soft, gummy oil suspensions and polar molecules to help bind the contaminants together. These binding agents include polar additives (for example, dispersants and rust inhibitors) as well as oil degradation products (additives and base oil) from oxidation and thermal distress. Even free water is known to provide cohesive forces to help paste particles together to form clumpy restrictions in leakage paths.
This is why a sudden change in lubricant chemistry, such as the introduction of an ester-based synthetic lubricant, can dissolve or carry away these binding agents, leading to leakage once again. In some instances, large clumps of particles can become dislodged and resuspended as a result of a fluid chemistry change. These mobilized clumps can later be pulled into orifices and oilways, causing flow restriction and catastrophic lubrication failure.
The Adrenaline Effect
Surprisingly, many moving, close-tolerance machine parts can be aided by particle suspensions, as well. The most notable are hydraulic pumps and actuators. In these components, internal leakage impairs performance (loss of volumetric efficiency), causing more heat generation and energy consumption. In time, the leakage escalates to the point that the components must be replaced due to sluggish operation. This is similar to the loss of combustion efficiency of an engine from piston ring/cylinder bore wear.
Lubricants and hydraulic fluids that carry solid contaminants in the size range of the dynamic gaps, annular zones and slits (that serve as the internal leakage path) will experience a dynamic packing phenomena called the adrenaline effect. When this occurs, a rise in efficiency (and power) is experienced by these components spurred by the sealing mechanism of the particles. Who would have guessed that particles can boost pump flow!
However, control your excitement. There's a dark side to this story. Need I remind you that hard particles cause irreparable damage in dynamic zones by gouging, plowing and scoring of the working surfaces? As this occurs, the temporary gain from the adrenaline effect is lost as the gaps form a widening gulf. This prevents all but the largest particles from bridging the clearance. Therefore, while the surge of adrenaline from particles contamination is real (when components are young), this is a false economy due to rapid aging from accelerated wear and gushing internal leakage that soon develops (See Figure1).
Moral of the Story
Why did I tell this story about oil clotting? For one, I wanted to clarify confusion regarding the role of particle contamination in leakage path constriction. Indeed, this is not lubrication folklore but is a factual physical phenomenon. For instance, we can readily observe the damming effect from particle loading in oil filters as pressure drop rises. Also, common pore-blockage particle counters measure flow decay (or pressure rise) through calibrated membranes to estimate particle concentrations in lubricants and hydraulic fluids. So it is no surprise that the same phenomenon would occur in any narrow orifice or clearance through which oil routinely flows in the machine.
So the moral to the story is this: If you want your contaminants to serve as "stop leak" agents, then a dirty and more sludgy oil is better (I'm kidding, of course). Static seals and leaky fittings/connectors benefit the most. However, if you don't want your oil to carry hard, gummy particles into critical clearances and orifices, I suggest you take a hygienic approach by keeping it clean, dry and healthy. No doubt, you've been given that advice before.
Reference
Gabrial Silva. "The Adrenaline Phenomenon of Silt." TSF Journal, 1987, Volume 7. Fluid Power Research Center, Oklahoma State University.
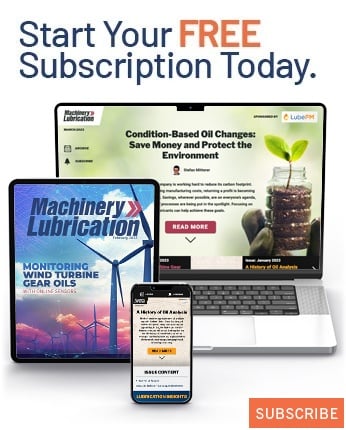