During the Lean, Reliable and Lubed 2008 conference earlier this year in Nashville, Tenn., ICML presented Cargill’s corn milling operations in Wahpeton, N.D., with the 2007 John R. Battle Award for Excellence in Lubrication.
Cargill Wahpeton’s journey to attaining world-class status started several years ago. In 2003, the plant identified its lubrication program as a target for improvement as part of the site’s overall reliability program. Although lubrication was beginning to be addressed, the plant lacked the on-site expertise and skill required to effectively deploy a world-class lubrication program.
In December 2003, a lubrication specialist was added to the Wahpeton team and immediately began assessing its status and formulating a plan to improve lubrication effectiveness. A benchmark assessment of the plant’s lubrication practices was performed to identify strengths and opportunities for improvement. Industry-recognized best practices were put into place, including the following:
-
Air filtering and desiccating breathers replaced standard toadstool breathers, plugs and dipsticks.
-
Visual sight gauges replaced dipsticks for non-intrusive level monitoring.
-
Filtering connections were installed on sumps to allow quick and easy removal of contamination and oil changes.
-
Regular oil analysis and strict target cleanliness levels were put into place.
-
Performance metrics such as lubrication asset health and overall lubrication effectiveness (OLE) were implemented.
It took more than two years to perform all planned equipment upgrades and preventive maintenance (PM) changes. PM reviews and program adjustments are now discussed and implemented as needed. The implementation strategy focused on common-sense changes that were easy to justify and would make significant improvements to the quality of the program. Areas which offered the greatest opportunity for results were selected.
Electric Motor Regreasing
Electric motor regreasing is a common area in industry that offers opportunity for improvement. Mixing incompatible greases in the bearings is one of the leading failure modes for electric motors. The solution was to replace the standard grease zerk with a buttonhead-style zerk that is used at this plant only on electric motor bearings. Replacing the fitting was an easy swap that took the lube technician only a few moments during each regreasing route to accomplish. Only the electric motor grease gun has the mating applicator tip. This change resulted in significant improvement, eliminating the accidental introduction of incompatible grease.
Modifications
Some equipment modification was required to make lubrication tasks more efficient and prevent contamination. Installations were accomplished over time; asset criticality and degree of contamination or oil degradation were considered priority factors in scheduling. Using the results of oil analysis, remediation efforts were prioritized. Machines with degraded oil and high wear debris were targeted as the first to be modified and where cleanup efforts would begin. Machines with high contamination levels were next in priority. Post-remediation oil sampling was used to verify effectiveness of the efforts. The targeted machinery was identified through equipment list validation and criticality ranking.
Filtration
Filtration was a key component of the effort. If the equipment had its own filtered lubrication system, the effectiveness of the stock filter was evaluated for the possibility of upgrading to a better filter. Portable filters are used to maintain oil cleanliness in equipment without a circulating lubrication system. At the onset of the program, only one portable filtration unit was used for the entire plant. Cargill Wahpeton now has eight units available. Portable filters are dedicated to different oil types to avoid cross-contamination of oil products.
Portability
Portability is important in a plant like Cargill Wahpeton. The team soon realized that most commercial portable filters are too large, heavy and bulky to get to the most remote areas such as conveyor heads and tank agitators which may be located at the end of a maze of stairways and vertical ladders. A lightweight, modular system that addressed the portability requirement was developed.
Oil Analysis
On-site oil analysis is the monitoring technology tool that identifies targets for improvement. Contamination is the biggest threat to equipment and is easily identified with the on-site lab. Adding a technician who was familiar with the needs of a lubrication program had two benefits: It improved data analysis and was instrumental in moving the program forward.
Lubrication training is required and certification is encouraged for the field technicians.
The Wahpeton plant has a well-developed reliability program that incorporates a balance among preventive, predictive and proactive maintenance strategies. The program has allowed the maintenance staff to be reduced by approximately 50 percent from its high of eight years ago to its current levels. Ninety percent of all maintenance is planned, and approximately 35 percent of the planned maintenance is generated as a direct result of the plant’s condition-monitoring program.
Other Recognitions
“Team Wahpeton” is the motto of the Wahpeton facility and is demonstrated by the integration of Cargill personnel along with embedded contractors such as Allied Reliability Inc. and UGL Unicco Services Inc. These companies work together to make this plant operate at peak efficiency and reliability. The Wahpeton facility demonstrates what may be accomplished when traditional barriers between a parent company and contracted service providers can be bridged to make the whole “team” a family unit.
Besides winning the 2007 John R. Battle Award, Team Wahpeton has received two other prestigious awards recently that attest to its dedication to comprehensive excellence; the plant’s equipment reliability program was a key component to these honors. Team Wahpeton was selected by Cargill corporate management to receive the “Cargill Best Plant Award” for the second time in four years. This was the first time any Cargill plant has been recognized a second time with this award. Cargill operates more than 1,200 plants worldwide.
Last year, IndustryWeek magazine recognized Team Wahpeton as a winner in its annual Best Plants Awards competition for comprehensive excellence in manufacturing.
For more information or to nominate your company for the John R. Battle Award, visit www.lubecouncil.org or e-mail info@lubecouncil.org.
History of the John R. Battle Award
The John R. Battle Award recognizes organizations that have exhibited excellence in the application of machinery lubrication. The award was designed to motivate companies to improve machine reliability and maintenance quality through development, implementation and management of a best-in-class machinery lubrication program. ICML’s focus is not only to identify award recipients, but also to encourage excellence and share best practices among user organizations on a global scale. The Battle Award recognizes role models for benchmarking and setting performance standards by the lubrication and reliability community. To become a John R. Battle Award recipient, the ideal organization must demonstrate a solid lubrication program, supported by multidisciplinary efforts and approaches, with sustainable results and continued improvements.
About ICML:
The International Council for Machinery Lubrication (ICML) is a vendor-neutral, not-for-profit organization founded to facilitate growth and development of machine lubrication as a technical field of endeavor. Among its various activities, ICML offers skill certification testing for individuals in the fields of machine condition monitoring, lubrication and oil analysis. ICML is an independently chartered organization consisting of both paid professional staff members and volunteer advisors. It provides lubrication and oil analysis standard development support, scholarship, skill-based testing and certification, and recognition of excellence.
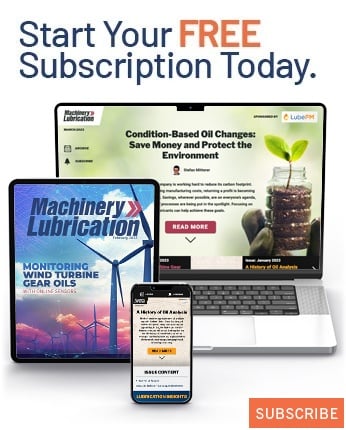