My job is to help organizations do a better job of lubricating and maintaining their machinery. For this reason, the people I work with typically understand the importance of having an effective lubrication program and have made a commitment to improve their lubrication practices. Although good intentions and the desire to improve lubrication are common, world-class lubrication programs are not. Lubrication practices in the average manufacturing facility are often so inadequate that the notion of achieving a world-class program seems like a pipe dream. This, however, is not the case.
With the right game plan, improvement is always possible. Developing and implementing a world-class lubrication program, like many endeavors, should be approached as a continuous process, not as a project of finite scope. So if you are like most folks and have difficulty getting traction in this venture, here are some potential solutions to five common roadblocks you’re likely to face.
Lack of Knowledge
Many people work hard to achieve little; and in some cases, their good intentions cause actual harm. One of the fundamental obstacles to lubrication excellence is a lack of understanding of its key elements. In order to be effective, individuals and organizations must obtain the appropriate level of knowledge and develop the appropriate skills. A lack of understanding is one of the most common causes of lubrication mistakes, such as using the wrong lubricant or contributing to lubricant contamination. Having an elementary knowledge of lubricant formulation, function and management methods enables personnel to become more involved in problem analysis and solution development.
Additionally, this enables personnel to comprehend the impact of their actions throughout their daily activities. This is a rather simple obstacle to overcome because lubrication training is readily available. The trick is to develop training standards and a skills assessment for the entire organization, not just offer a one-time training session to key individuals. A defined training program should be developed that spells out the required training for any job function that affects lubrication and provides skills standards for each.
No Game Plan
Sometimes the hardest part of the process is getting started. The best way to start improving is to assess the current state of your program. Benchmarking performance in key areas of lubrication will identify the greatest threats and the biggest opportunities. Based on the size of the opportunities and the resources required to address them, you can prioritize and develop an action plan, including target dates for completion of each individual action item.
Improvements to the lubricant storage facility and handling procedures are often the best place to start. Because this project doesn’t affect operations, it can be tackled at any time. It is a highly visible and tangible improvement to your program that indicates to others that you are serious about remediating your methods.
Not Enough Money or Time
This is a problem that affects us all. No matter how economically justifiable a project is, it seems there is seldom enough money to fix every problem to the extent we would like. The short answer to this problem is to make due. That doesn’t mean you shouldn’t lobby strongly for the necessary resources to execute lubrication, but rather to use what you have in the most effective way possible.
If you don’t have enough manpower to perform all of your preventive maintenance (PM) and you can’t get more, simply eliminate PMs, starting with those of least importance, until you have a manageable pool of work. Otherwise, you may miss critical PMs while trying to comply with other scheduled activities that have little or no value.
Lack of Support from Other Groups
This one is also quite common. A good lubrication program requires involvement from the entire organization. Production must support and, in some cases, lend a hand to the lubrication program. Procurement must allow the program to excel by not interfering with the selection of lubricants and related products and services. Finally, management must provide the appropriate support to allow the maintenance and reliability programs to flourish.
This requires an understanding of how reliability affects (and is affected by) every aspect of manufacturing and how lubrication fits into the overall goals. The solution is simple: education. It may be your responsibility as a maintenance and reliability professional to educate others in the organization on reliability issues. A good training program should include defined requirements for all who affect lubrication and reliability.
Lack of Documented Success
I am often disheartened when I hear stories of lubrication excellence that have no documented results. It is not enough to improve the program; you must also measure it. Metrics such as PM compliance and asset health should be utilized to track the quality of lubrication, and also to track the benefits realized by the execution of these activities. If you invest the time and expense to develop a world-class program, others will eventually ask for the results. The answer to this question should not be the generic response: “We are experiencing fewer failures.” The correct answer should be: “We are experiencing X percentage fewer failures, and thereby, we’re saving X dollars per year as a direct result of lubrication improvements.”
As you navigate this path, you will certainly encounter other roadblocks that sometimes call for creative solutions. Remember, you cannot fix this problem in one month, or even six months. Develop a game plan, set goals, measure your performance and observe the snowball effect that follows. Eventually, lubrication excellence will become a source of pride and profit for the entire organization.
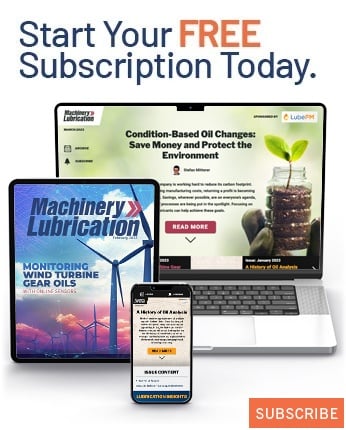