In my previous editorial columns, I described the two most infamous killers of machines: particle and water contamination. While instructing a machinery lubrication seminar recently, I was a bit taken back by the lack of knowledge about air contamination and its effects on lubricants and machine components. Thus, I have decided to make it the topic of this discussion.
Air can exist in oil in four different states of coexistence. They include the following:
1. Dissolved – not visible (no clouding present); can represent as much as 10 percent of the total volume.
2. Entrained – unstable microscopic air bubbles (clouding present).
3. Free – trapped pockets of air in dead zones, high regions and standpipes.
4. Foam – highly aerated tank and sump fluid surfaces (more than 30 percent air).
The problems associated with aerated oil include:
- Oxidation
- Thermal degradation
- Poor heat transfer
- Retarded oil supply
- Cavitation
Depending on the machine design, application and aeration severity, it is possible that all five of these conditions could be happening concurrently.
1. Oxidation
Aeration exposes oil to oxygen. The bubbles produce a high surface area interface between the air and the oil. The interface serves as reaction sites for oil oxidation to initiate, particularly when the oil is hot and moist.
2. Thermal Degradation
Aerated oil generates heat by the following mechanisms:
-
Adiabatic compression of air bubbles (localized heat generation)
-
Aeration-induced oil flow resistance in piping and components (energy is converted to heat)
-
Loss of bulk modulus (air makes oil compressible, which generates heat)
The heating problem is compounded by impaired cooling, as described below. The building heat leads not only to oil oxidation but also to thermal degradation (such as from microdieseling), forming varnish, sludge and carbon insolubles. Additives such as zinc dialkyldithiophosphate (ZDDP) will also deplete prematurely due to the heat.
3. Impaired Heat Transfer
Aeration degrades the heat transfer properties due to the following reasons:
-
Aerated oil is not a good thermal conductor.
-
Restricted oil flow from aeration impedes convection (movement of the heat from movement of the fluid).
While foam retards the oil’s ability to release heat in the reservoir, entrained air also interferes with heat transfer (and movement) in coolers and through machine casing, piping and other thermally conductive surfaces. When oil runs hot, viscosity runs thin, which degrades film strength in frictional zones and leads to wear. Of course, impaired heat transfer properties compound the problems described in numbers 1 and 2 above.
4. Retarded Oil Supply
Many factors contribute to oil supply problems associated with air. Some of these factors include:
-
Oil Compressibility. Aerated oil is hard to pump. It’s like trying to pump against a sponge. The actual delivered oil volume (oil flow rate) may be only a fraction of what the pump normally supplies without the aeration condition.
-
Dampening. Foam causes the dampening of important headspace oil movement in machines that depend on oil-lifting (or oil-throwing) mechanisms, including splash lubrication, paddle gears, flingers and slingers. The foam retards the oil travel (toss) through the air, resulting in it failing to reach critical zones of the machine, including bearings and gears.
-
Reduced Oil Density. Many machines depend on oil flowing efficiently by gravitational forces. A bubbly oil has low density and gravitational pull. For instance, a ring oiler may lift some foamy oil to the upper port of the journal bearing; however, its low density (and increased apparent viscosity) impairs its ability to penetrate downward into the bearing’s channels and grooves for lubrication. The same is true in gravity oil drains and headers from bearings and gears in circulating oil systems.
-
Air-lock. Foamy, low-density oil can cause air-lock, resulting in a complete cessation of oil flow (restricted oil drains, loss of pump prime, redirected oil flow, etc.). An aerated oil has an apparent viscosity sharply greater than that of the oil alone, which compounds the problem.
-
Reduced Oil Level. Foam robs liquid-phase oil from the reservoir or sump, which means the working oil level falls. This often brings the oil level below what is needed to adequately prime pumps (head), supply oil to lifting devices (ring collars, paddles, flingers, slingers, etc.) and supply oil to bath/splash-lubricated gears and bearings. Low oil level is a circular problem causing more aeration, more heat and less air-release residence time.
5. Cavitation
When vapor bubbles become rapidly pressurized, such as in a pump or journal bearing, destructive microjets of oil can collide with machine surfaces at extremely high velocities. Some have estimated that the velocities may approach the speed of sound. The result is a progressive, localized erosion of these surfaces. Note that vapor bubbles cause most erosive damage from cavitation, not air bubbles. Vapor bubbles form from the oil itself (light oil fractions) as well as from water contamination (water vapor).
So, now that we know the effects of aeration on the lubricant and machine components, we can discuss ways of stopping it from becoming a problem. What follows are some steps to take if you notice an air contamination problem.
Step 1. Stop air from becoming entrained. When you control entrained air, by default, you also control foam. Here are the top four ways air becomes entrained in lubricating oils and hydraulic fluids:
-
Elevated oil returns (free falls that cause churning and aeration) vs. return lines with diffusers that ease the oil back to tank.
-
Suction leaks or pump seal leaks that entrain air.
-
Over-agitation of tanks (low oil level or poor tank design), causing turbulence, vortexes and/or lapping (folding in air on tank surfaces).
-
Vented drains where air and oil mix coming down drain lines before returning to the tank.
Step 2. Keep air buoyant to aid its rapid detrainment from your oil. If air does become entrained, utilize the following strategies for rapid release to the atmosphere without forming foam:
-
Ensure healthy condition of defoamant additives.
-
Keep air bubbles large and buoyant by keeping oil interfacial tension high. The smaller the air bubble, the longer it takes to reach the surface and detrain. Factors that reduce interfacial tension include emulsified water, oxides, and polar additives or contaminants.
When entrained air passes through oil filters, pumps and bearings, air bubbles are crushed to such an extent that they don’t release quickly. In extreme cases, the air/oil mixture has the consistency of whipping cream.
Step 3. Give air detrainment sufficient residence time. Given enough time, even finely crushed air bubbles can migrate out of the oil. Strategies for accomplishing this include:
-
Large-volume reservoirs
-
Reservoirs with flow-directed baffling to avoid short circuiting
-
Use of settling and air detrainment tanks
Step 4. Deploy air detrainment practices and technologies to accelerate separation time. Options include:
-
Apply a slight reservoir vacuum.
-
Use an off-line vacuum chamber for both air release and dehydration purposes.
-
Install vortex deaeration technologies.
-
Install wire-cloth air coalescers/separators in the reservoir.
Managing aeration and the air-handling ability of lubricants is no insignificant matter. Air is a real contaminant that requires thoughtful monitoring and control, and left unattended, it can destroy your machines. Perhaps your contamination control program began with particle control, then progressed to moisture – much like discussed in my last few articles. But without a program that considers air as a contaminant, you will suffer losses.
I hope this article sheds some light on the subject for you and that you can now make an informed decision on how to best alleviate your air problems.
References
Jim Fitch. “The Perils of Aerated Oil - Let Your Machine Burp.” Practicing Oil Analysis magazine, January 2005.
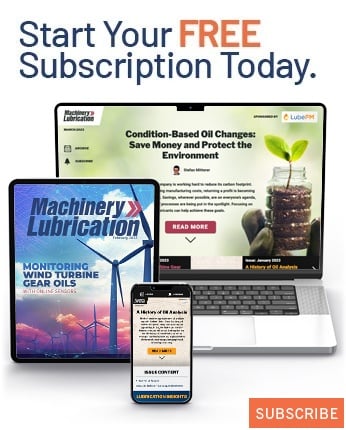