Lincoln, a world-leading manufacturer in automated grease lubrication systems for mining equipment, featured at Hannover Messe its program on lubrication systems for all industries.
Lincoln's comprehensive program includes automated lubrication systems for grease and oil, lubrication tools and service bay equipment for fluid handling – covering all demands for professional industrial lubrication.
Lincoln’s new product is a single-line lubrication system / consisting of:
· Pumps 603S and 653S
· QSL / SL Injectors
· SE1 Suction Elements for Used Lubricant
Equipment that operates in harsh conditions requires regular lubrication to ensure performance. When a bearing or component fails as a result of insufficient lubrication, the result is downtime and losses. The single-line 603S and 653S pumps/systems automatically supply the lubrication points with exact metered quantities in programmed interval while the equipment is in operation.
As a result, the robust system is ideally suited for wind turbines – even offshore applications – and for off-road mobile equipment such as construction and mining machines and heavy-duty commercial vehicles.
In the general industry the system is used to lubricate small to mid-sized stationary machines or machine groups.
Special Features for Wind Turbine Applications – Also for Off-shore Systems
Lincoln single-line systems completely vent during the pause interval. As a result, they are suitable for fast separating lubricants.
For rotating operation in wind turbines the reservoir is equipped with a follower plate and stirring paddle, which also facilitates the usage of fast separating lubricants. For stationary operation, a stirring and fixed paddle is sufficient.
Simple System Design - Easy to Expand
Pump and Accessories - All-in-one
The pump with integrated controller is easy to install. The all-in-one design of the pump includes the programmable controller, a pressure switch/transducer and a vent valve.
Simple System Design – Easy to Expand
The single-line system's design and layout is uncomplicated, making it easy to install and operate. A single mainline reduces material and installation costs.
Easy to Service
It is quick and easy to exchange out an injector. The mainline or neighboring injectors do not have to be removed. The exchange can be performed between lubrication cycles so that there is no wastage of lubricant or excessive costly downtime.
QSL and SL Injectors
The metal-to-metal fit of the injectors makes them suitable for high pressure. Each injector's output can be individually set. The injector function is generally visually monitored, but optional electrical monitoring or a GSM controlled system is available.
Visual Monitoring – To Ensure all is Well
Each injector has an indicator pin that moves with the pressure buildup and venting. This facilitates easy trouble-shooting when required by simply observing the indicator pins.
Additional Pressure Switch
An additional pressure switch at the end of larger systems can be used for added pressure control to ensure correct lubrication.
SE1 Suction Element For the Extraction of Used Lubricant from a Single-line System
The SE1 suction element was especially developed to extract the used lubricant from single-line systems used in wind turbines. The used lubricant is collected in a separate 10-liter container AFB 10 and can be recycled – or used for example for the lubrication of gear drives.
As a result, the problem of used lubricants in bearings is reduced. The lubricant no longer pushes through seals and doesn't spoil or pollute the bearing environment. Additionally, a reusage of the lubricant conserves resources and preserves the environment.
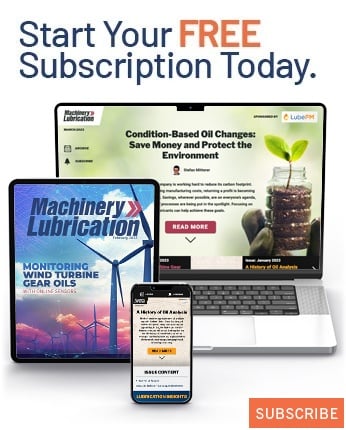