Plant and equipment lubrication is often focused on bearing lubrication, with too little attention paid to seal lubrication. Labyrinth seals provide very efficient sealing of housings, contributing to good bearing life when properly grease purged but if this is not done correctly then maintenance and productivity suffers from bearing failures and production losses. A simple low cost improvement in this area can bring substantial benefits.
Typically labyrinth seals are greased by hand on a routine basis but with relatively long re-lubrication intervals compared to what is needed for efficient sealing outcomes. A labyrinth seal needs a correct grease fill to be maintained for the best sealing effect, and preferably a positive grease flow. Hand greasing will only provide a correct fill and sealing over a limited time frame and outside this the seal will be susceptible to the ingress of foreign matter. Poor sealing leads to premature bearing failures.
With hand greasing excess grease is typically applied in an attempt to improve the sealing outcome. The excess grease builds up around the seal, creating another problem, particularly in mining, as dirt becomes mixed into the excess grease, which can then be drawn back into the seal. This creates the need for periodic clean ups. Long doses of high pressure water are routinely used in mining operations to clean off this excess grease however this can result in dirt and water being forced back through the seals into the housing. The dirt creates a sort of grinding paste and as little as 0.05 percent of water in the grease will substantially shorten the life of a bearing with a reduction of the grease's lubrication properties which in turn leads to bearing failures. With GreaseMax these excesses of grease, and the problems that go with it, are avoided.
GreaseMax lubricators offer a much improved outcome for labyrinth seal greasing and have proven results in this application. Continuous grease pressure, a correct grease fill and a positive grease flow is maintained in the seal. Foreign matter is prevented from entering. This low-cost improvement can provide considerable maintenance and productivity benefits.
GreaseMax automatic lubricators are proven in industries around the world. One of the important features of GreaseMax is that they have no electrical or mechanical components. GreaseMax units work efficiently in all conditions. They can be mounted in any position, on moving and vibrating applications and on feed lines. They can be used in wet conditions – even underwater. To ensure total functional integrity GreaseMax is fully sealed and is not refillable or adjustable.
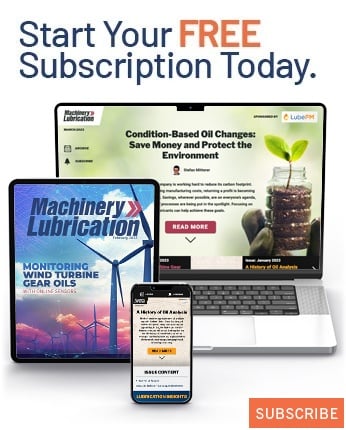