"Get to Know …" features a brief question-and-answer session with a Machinery Lubrication reader. These articles put the spotlight on industry professionals and detail some of the lubrication-related projects they are working on. If you know of an ML reader who deserves to be profiled, e-mail editor-in-chief Paul V. Arnold at parnold@noria.com.
Featured ML reader: Peggy Mumford
Employer: Pfizer Inc.
Job title: Machine lubrication technician II at the pharmaceutical company's facilities in Kalamazoo, Mich.
How many years have you been at this company?: 29 years
Where else have you worked over the years, and what has been your range of job titles?: My first job was with Upjohn, a pharmaceutical company. Due to a series of mergers and acquisitions, I now work for Pfizer. During my career, I have worked as a janitor, packaging line operator, quality lab technician and now a machine lubrication technician.
What types of training have you taken to get you to your current job?: I've attended a wide range of training since becoming a lubricator. I've received training for mechanical seals, bearings, automated lubrication systems, motor lubrication, the types of tools available - the list goes on and on, and I am still learning.
Do you hold any certifications through ICML, STLE or any other body?: I have my Machine Lubrication Technician Level I (MLT I) certification from ICML. I also attended an educational course taught by John H. Marino through the Lubrication Institute in Kansas City, Kan., for which I received certification as a lubrication analyst.
When did you get your start in machinery lubrication, and how did it happen?: In 1997, my job was eliminated and I had an opportunity to apply for a machinery lubrication job at my company. An onsite lubricator trained me and two other women in the basics of lubrication to get us started in our jobs. It was a huge learning curve because I didn't know what a grease zerk was, nor did I know that there was a difference in oils, except for the oil that I put in my car!
What's a normal work day like for you?: Each day is different depending on where I am scheduled to work. I could be lubricating pumps and motors for the building utilities, changing oil in small vacuum pumps, or working on lubricating a packaging line or blender in the manufacturing area. I have many customers that I work with closely in a variety of capacities at the company.
Because I work for a pharmaceutical company, the environment that I work in is clean compared to many businesses. I have realized in my 11 years as a lubricator that we always have work to do.
What is the amount and range of equipment that you service at your plant?: We have more than 9,000 pieces of equipment that are serviced by five machinery lubrication technicians. My areas of responsibility include packaging lines, product manufacturing, lab equipment, utilities, milling and micronizing equipment, automatic lubrication equipment, a purified water plant, and some warehouse equipment.
What lubrication-related projects are you currently working on?: I've been working on getting our oil storage rack installed in our lubrication shop. I also am working on a root cause analysis for gearboxes in the micronizing area. After completing this, I'm hopeful that this will cut down on oil sampling and changes which, in turn, will lead to cost savings.
What have been some of the biggest lubrication project successes for which you have played a part?: There were a couple of packaging lines that were transferred to one of the manufacturing buildings that I service. They were transported and shipped on a boat across the ocean; and because of the salt from the environment, all of the equipment arrived dirty and rusty. The chains needed to be cleaned and the entire line had to be cleaned and relubricated. All of the lube points and lubricants had to be identified as we did not receive any information on what lubrication practices were used previously. I oversaw the whole project, and we worked under a strict timeline. It was completed within the proper timeframe, which gave me a great sense of accomplishment. To this day, I still lubricate this equipment, and it runs great.
Another project for which I am proud involved equipment routing from a database. When I first started in this job, the database was not complete and it took a great deal of work to make sure all the equipment was listed on the routes and that the proper lubricants, points, frequencies and applications were listed. Because I was a new lubricator, I still was learning where the equipment was located by looking at prints of the building and finding the column that the equipment was near. So not only was I learning my responsibilities as a lubricator, but I learned how to read blueprints. This was much work and, once again as a new lubricator, it was a huge learning curve. At present, we are using a different program for our routes and are once again working to ensure everything is listed correctly.
I also worked with our safety and environmental liaison to ensure that the proper waste containers were in place for our used oil and also for our aerosol cans and used batteries. This was a fun project that taught me a great deal about how my job can affect the environment and the safety of others.
Finally, a simple project that I completed was one where I piped out small oven vacuum pumps in a chemistry lab. These pumps were new to me, and they were placed on a shelf that created a situation where I could not drain and change the oil very well without creating an oil mess. I piped out the pumps, and it is now much easier to drain them and complete an oil change in a more efficient manner.
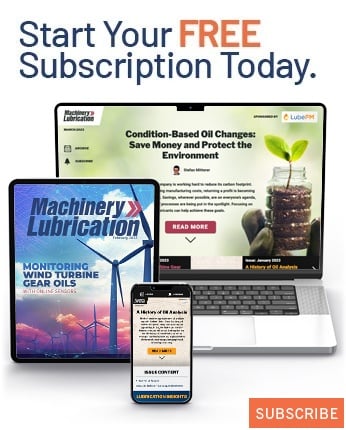